Ich habe seit einigen Jahren eine Kapp- und Gehrungssäge von Bosch im Einsatz. Diese wird überwiegend benutzt um Aluminiumprofile auf die richtige Länge zu sägen. Dafür ist ein spezielles Blatt erforderlich. Das Blatt ist von Kaindl und es hält tatsächlich, was versprochen wurde. Maschine und Blatt sind übrigens über die Menüauswahl „Mein Equipment“ zu finden.
An der Sägemaschine stört mich seit Langem, dass ich meine Profile beim Absägen nicht komfortabel und gut fixieren kann. Nach einigem Überlegen kam ich auf die im Folgenden beschriebene Lösung.
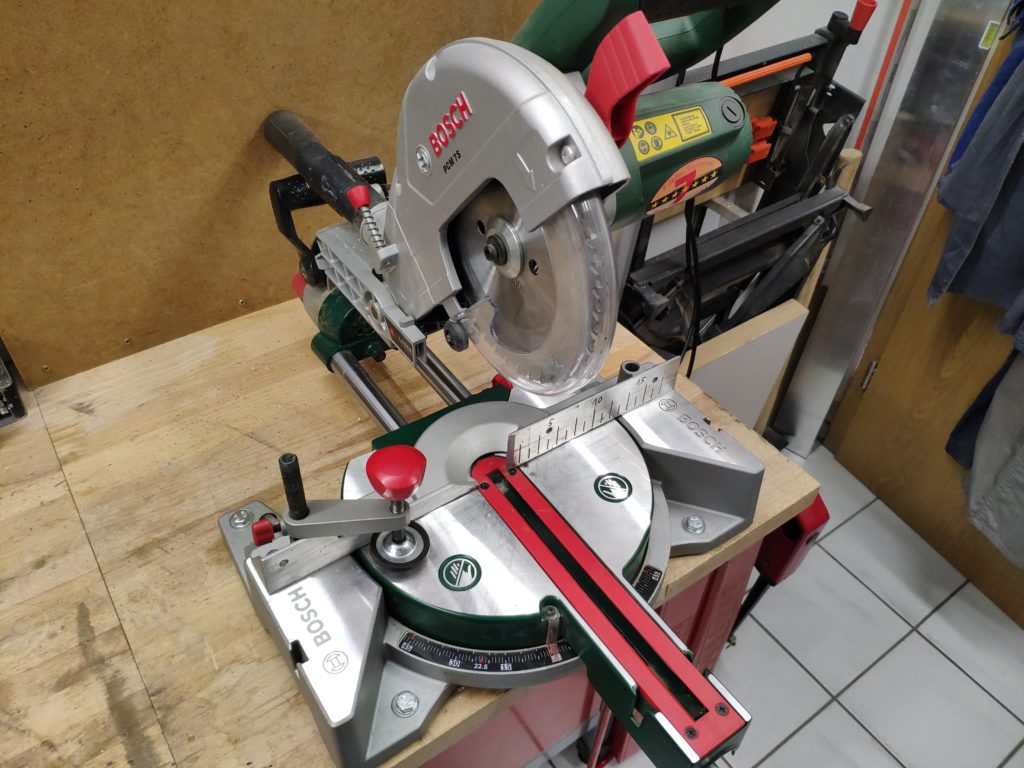
Das ist meine Metallsäge, – eigentlich eine Kapp- und Gehrungssäge. Die hintere Anlegeleiste bietet keinerlei Möglichkeit einer Spannung eines Werkstückes. Sie ist viel zu zerklüftet und eher ein Designstück als eine Hilfe.
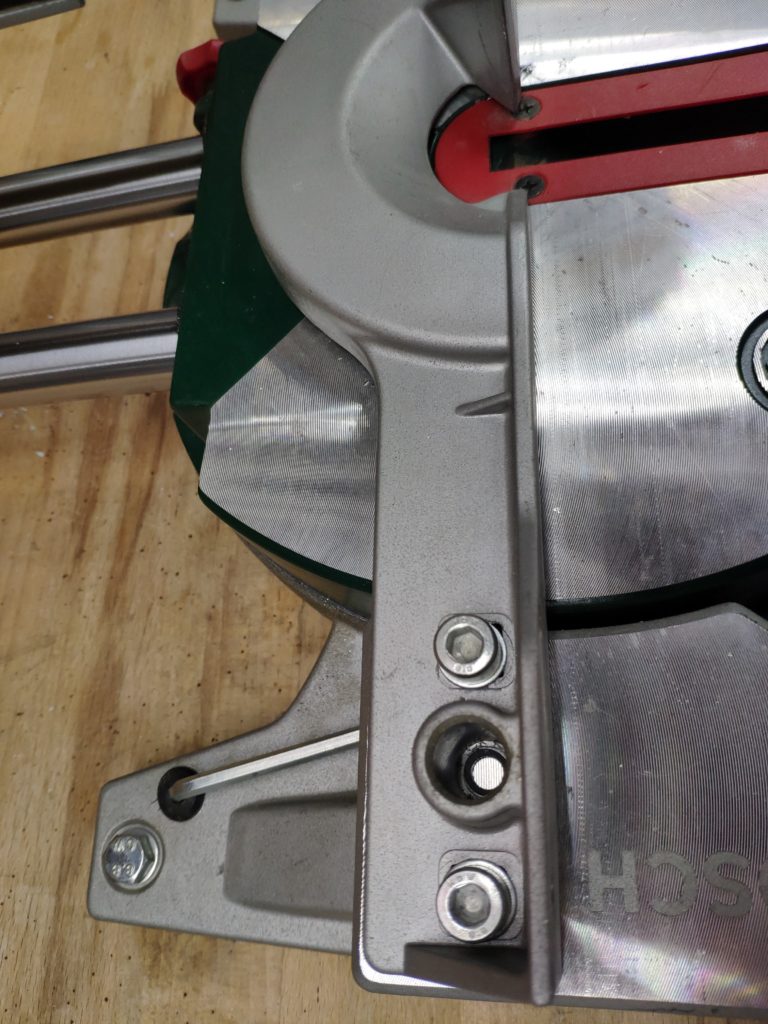
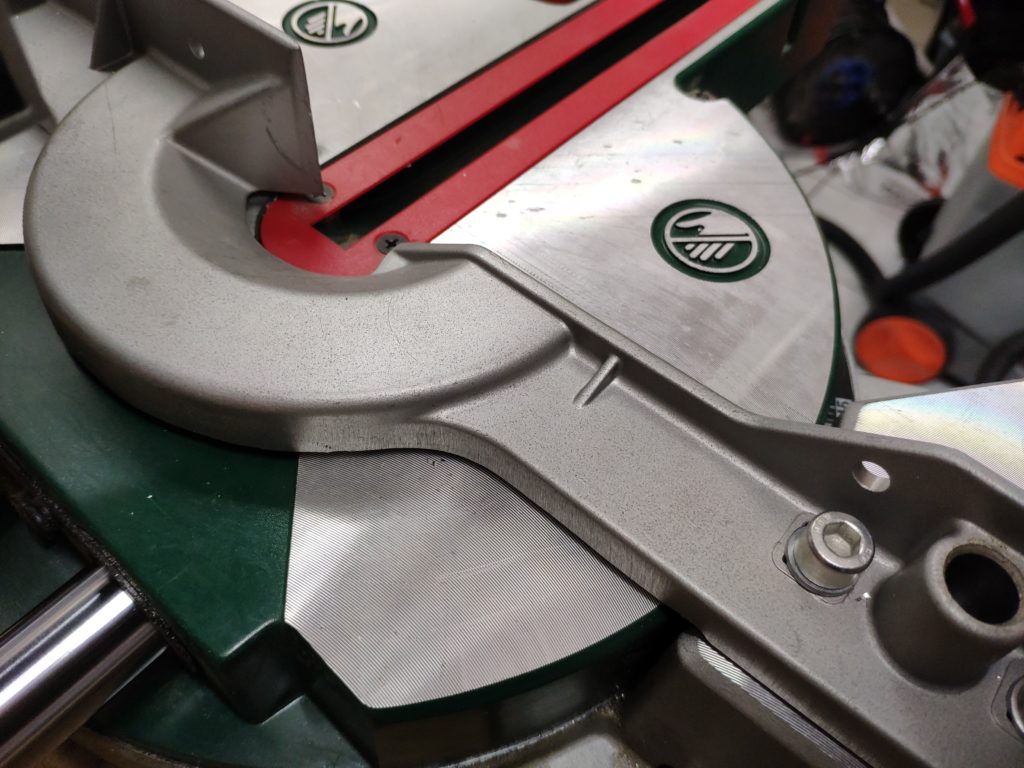
Die mitgelieferte Klemme ist ohne Unterlage unter dem Teller gar nicht zu gebrauchen, da das Werkstück durch den zu langen Gewindebolzen sofort verkratzt wird. Zudem basiert seine Fixierfähigkeit auf der Verkantung eines Metallbolzens.
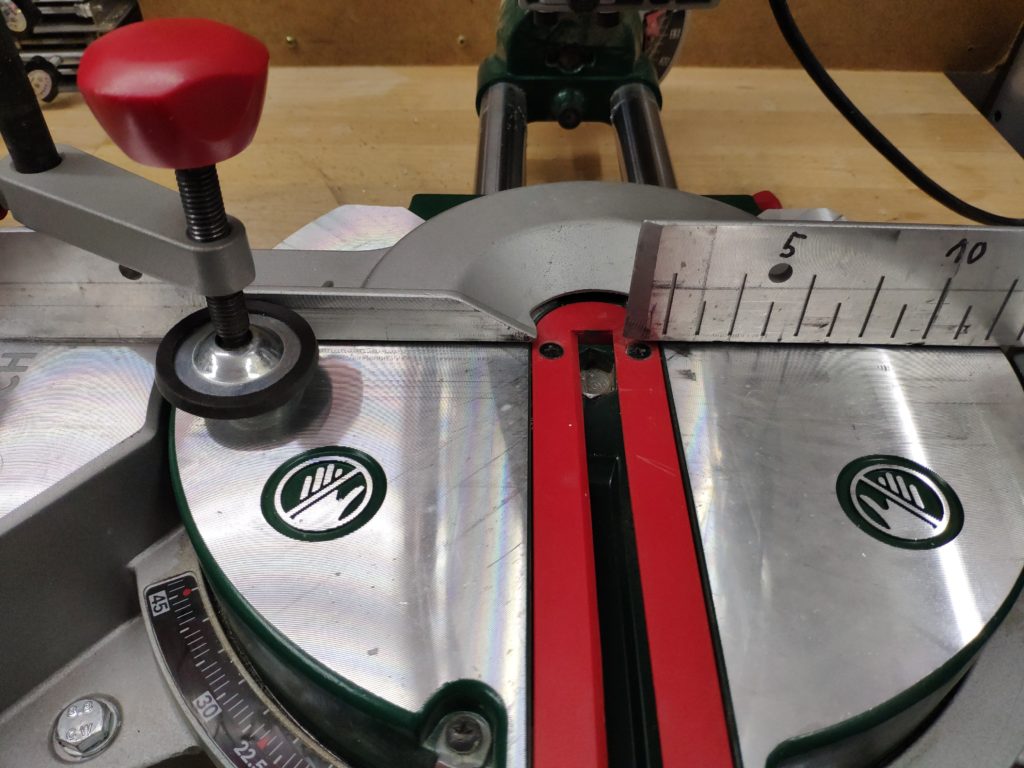
Wenn man die Anlegeleiste abnimmt, was problemlos nach Lösen von drei Schrauben möglich ist, sieht man eine glatte Oberfläche, die ohne weitere Änderungen nur an eben diesen drei Schraubenpositionen eine Adaptierung zulässt.
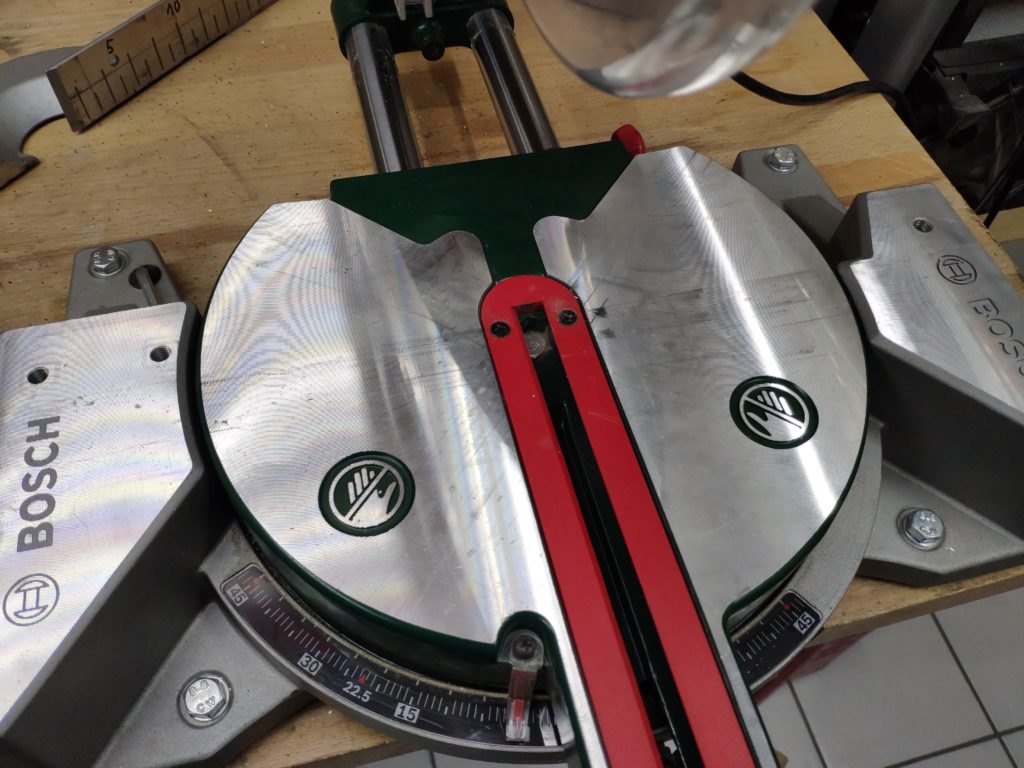
Meine Wahl für eine neue Anlegeleiste fiel auf zwei Alusystemprofile vom Typ 3030 mit Systemnut.
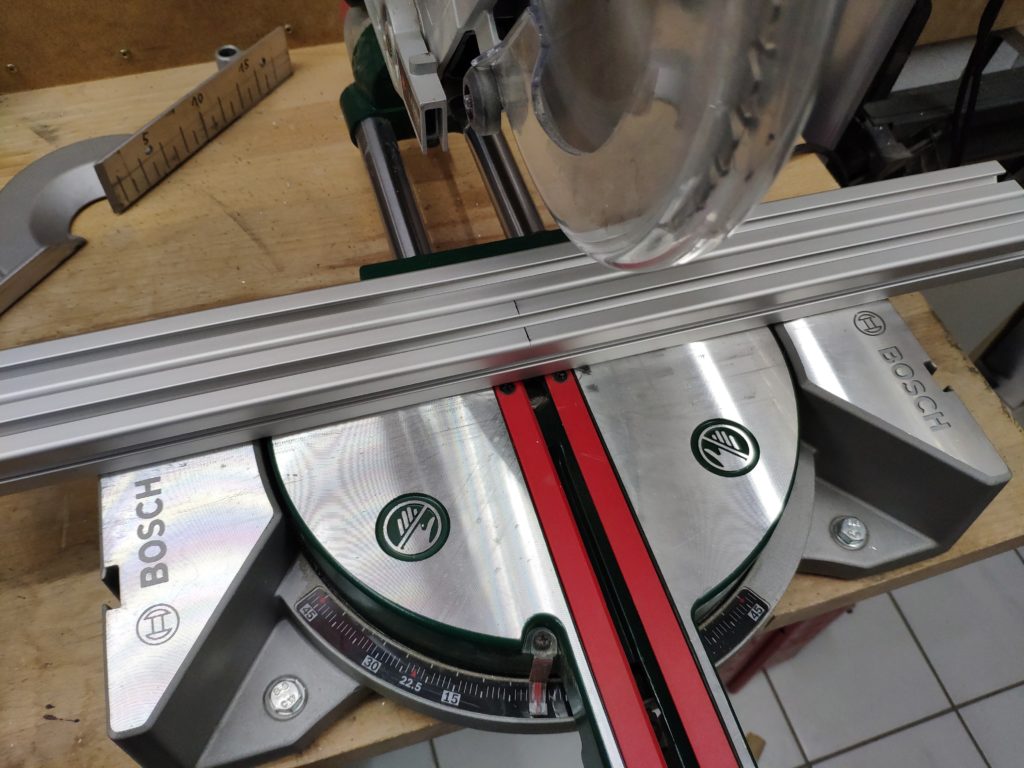
Zwei Profile müssen es sein. Wenn man sich die ursprünglich verbaute Anlegeleiste ansieht, weiß man schnell warum. Damit das Sägeblatt auch tatsächlich ein angelegtes Werkstück vollständig durchtrennen kann, muss das Blatt zwar an der unteren Kante nur knapp hinter die Anlegeleiste laufen aber aufgrund der Rundung des Blattes ist dann an der Oberkante das Blatt schon wesentlich weiter. Ein 30er Profil wird nahezu komplett durchschnitten und hätte dann keine Stabilität mehr. Kombiniert man zwei 30er Profile, wird das hintere nur ganz leicht angeritzt und man hat wieder Stabilität gewonnen.
Die Verbindung zweier Profile lässt sich ganz einfach mit Einschiebenutensteinen und Schrauben erreichen. Das hintere Profil wird durchbohrt damit es die Nutensteine auf der Rückseite des vorderen Profils fixieren kann. 6mm für die Durchgangsbohrungen und 10mm für den Schraubenkopf reichen aus. Mit der Fräse waren schnell die notwendigen 6 Schraubenpositionen bearbeitet.
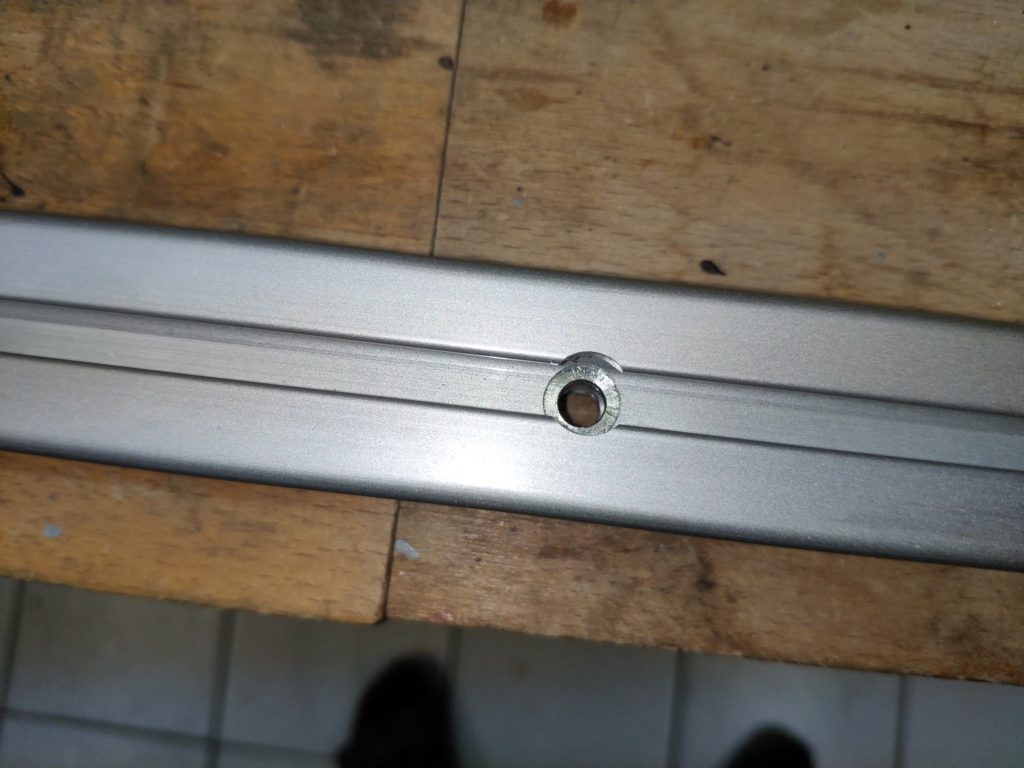
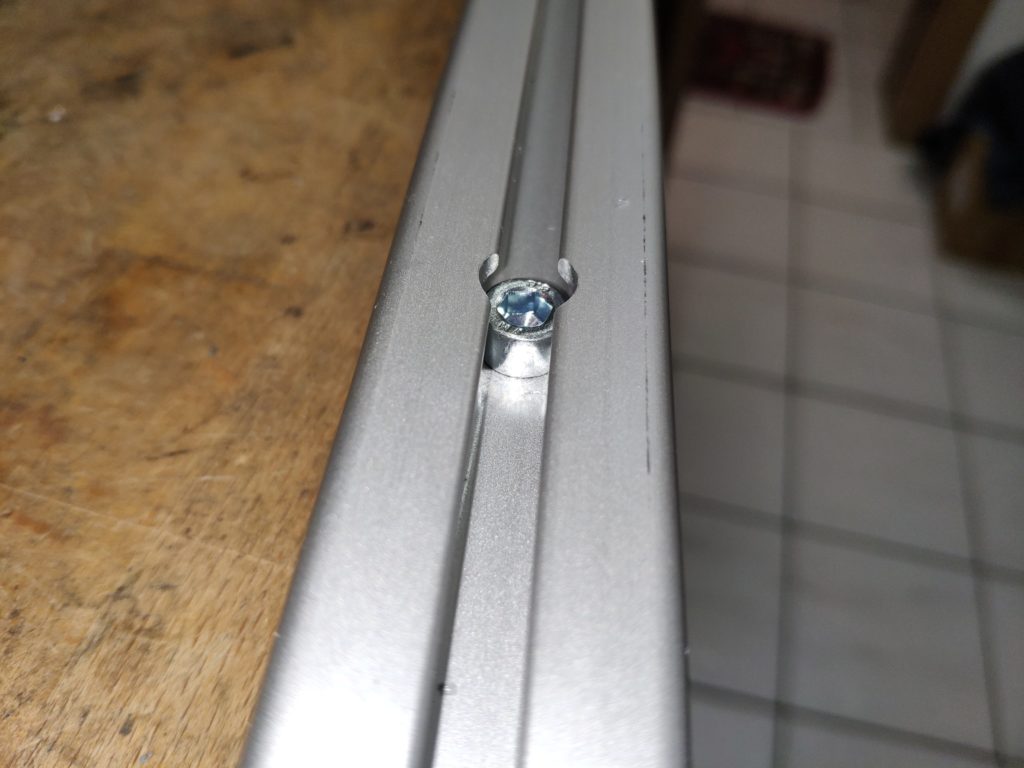
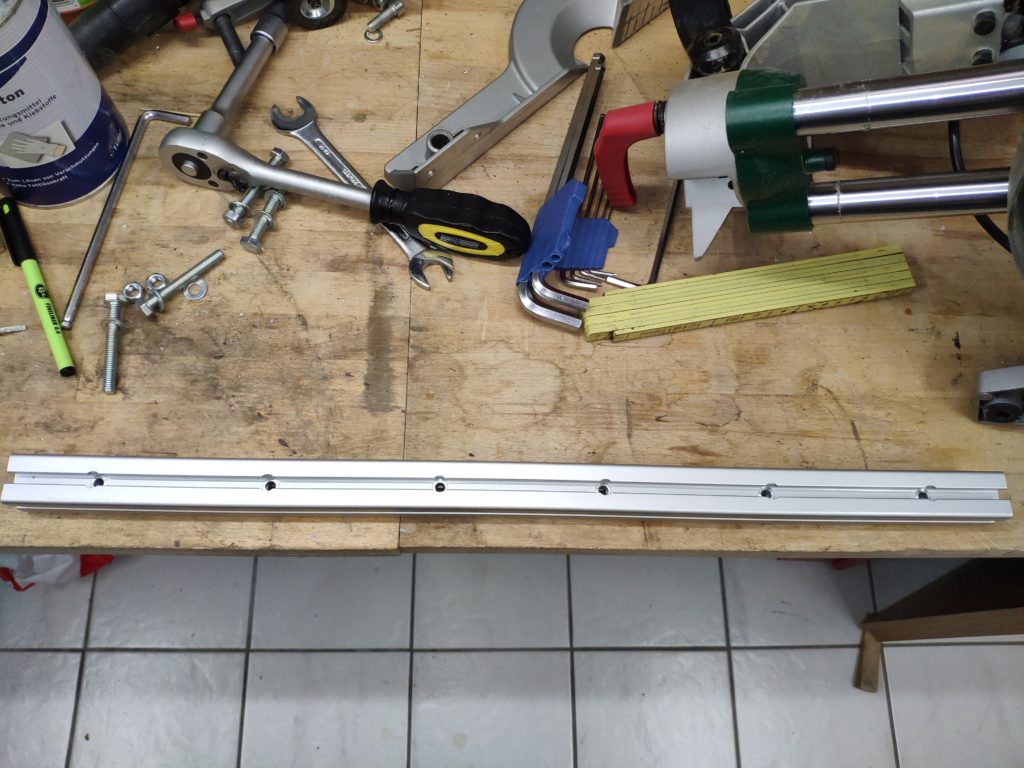
Die beiden Profile können dadurch miteinander fest verbunden werden.
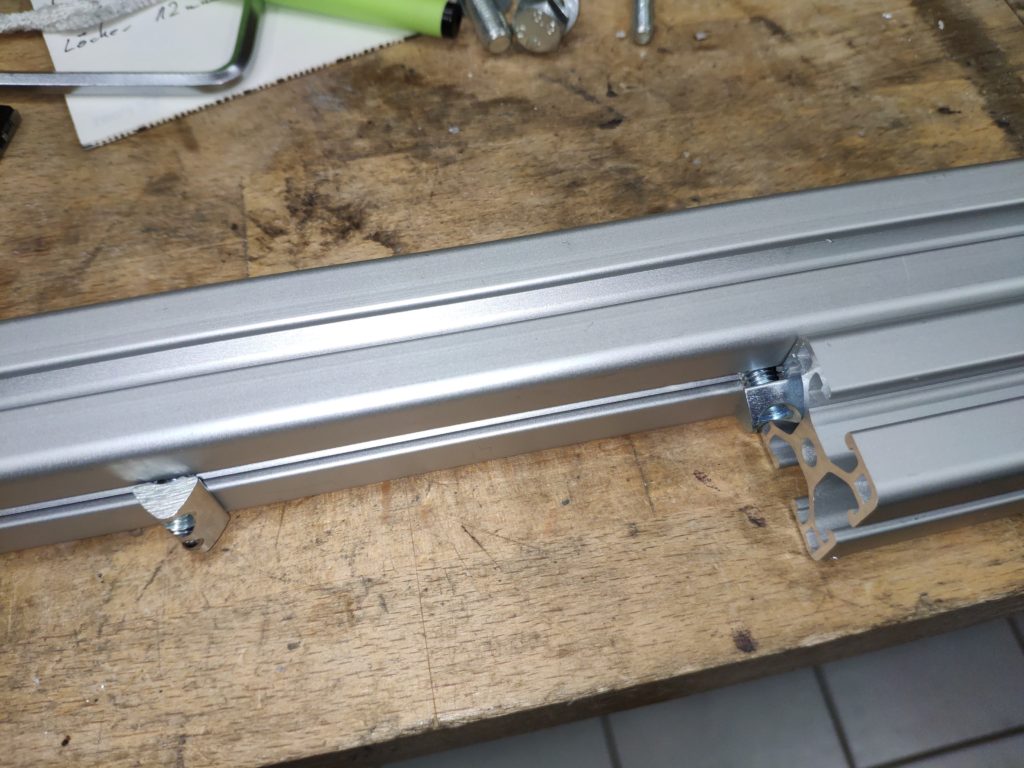
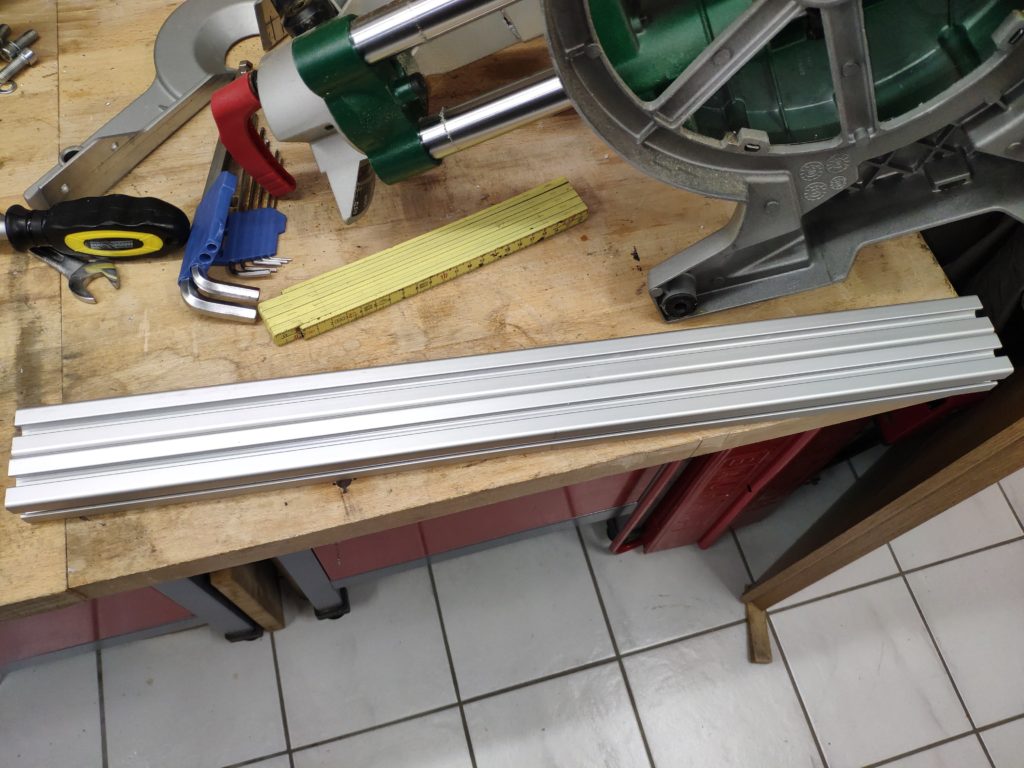
Im nächsten Schritt kommt jetzt die Fixierung auf der Arbeitsplatte. Dafür stehen ja nur die drei Bohrungen zur Verfügung, die die alte Anlegeleiste gehalten haben. Die Bohrungen sind mit M8-Gewinde versehen. Meine Nutensteine für die Profile haben 6mm Gewinde. 6mm Schrauben lassen sich problemlos durch die 8mm Löcher führen, – wie schon gesagt: Ich will an der Maschine möglichst nicht verändern. Die Frage, die sich stellt, ist: Wie ist denn die Beschaffenheit der Bohrungen in der Maschine?
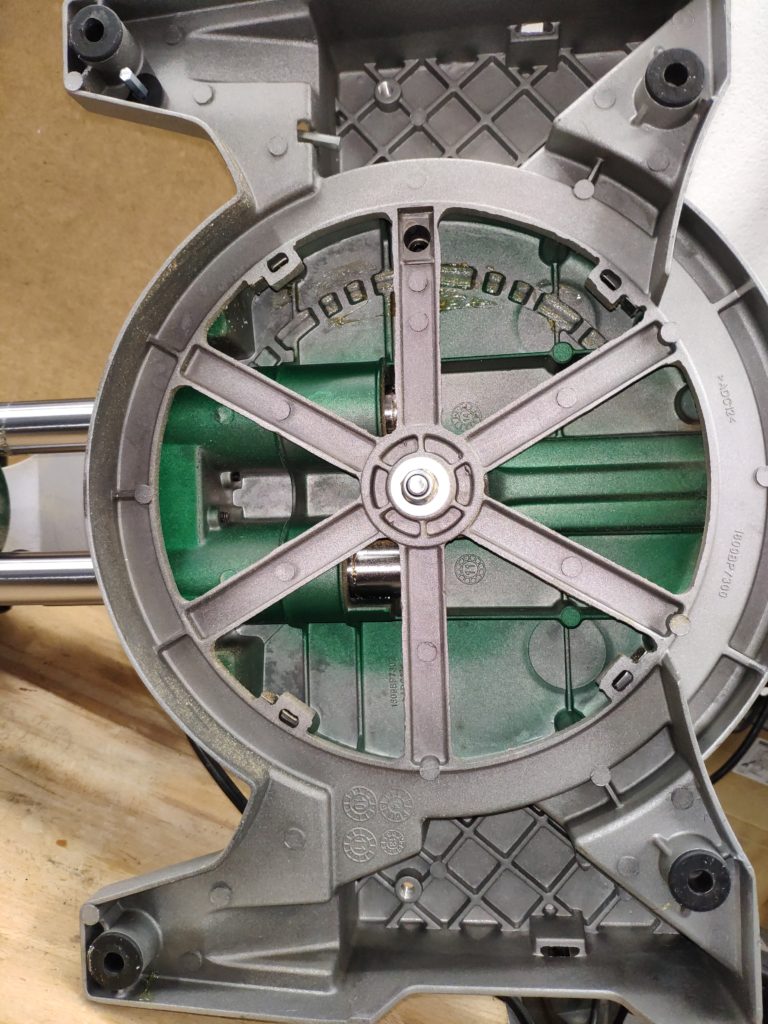
Wie man sieht, sind die Bohrungen mit den Gewinden im Guss etwas verstärkt ausgeführt worden. Dieser Sitz reicht für eine sichere Verbindung der Anlegeleiste.
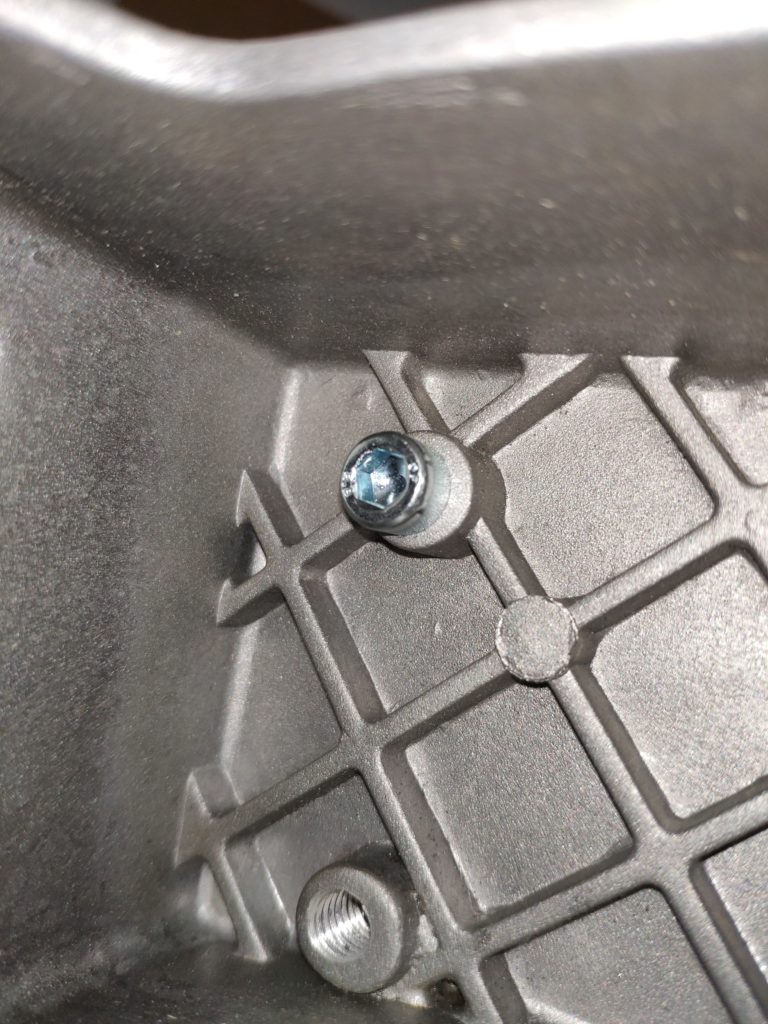
Im Gegensatz zum Bild habe ich dann aber doch noch Unterlegscheiben verwendet um die Pressung möglichst weit über den Guss zu verteilen.
Auf der Oberseite ist dass dann recht einfach ausgeführt. Es werden einfach 3 Nuts auf den Schrauben angebracht und das Profil (bzw. später die beiden Profile) werden aufgeschoben. Schließlich wird das Ganze noch mit den Schrauben fixiert.
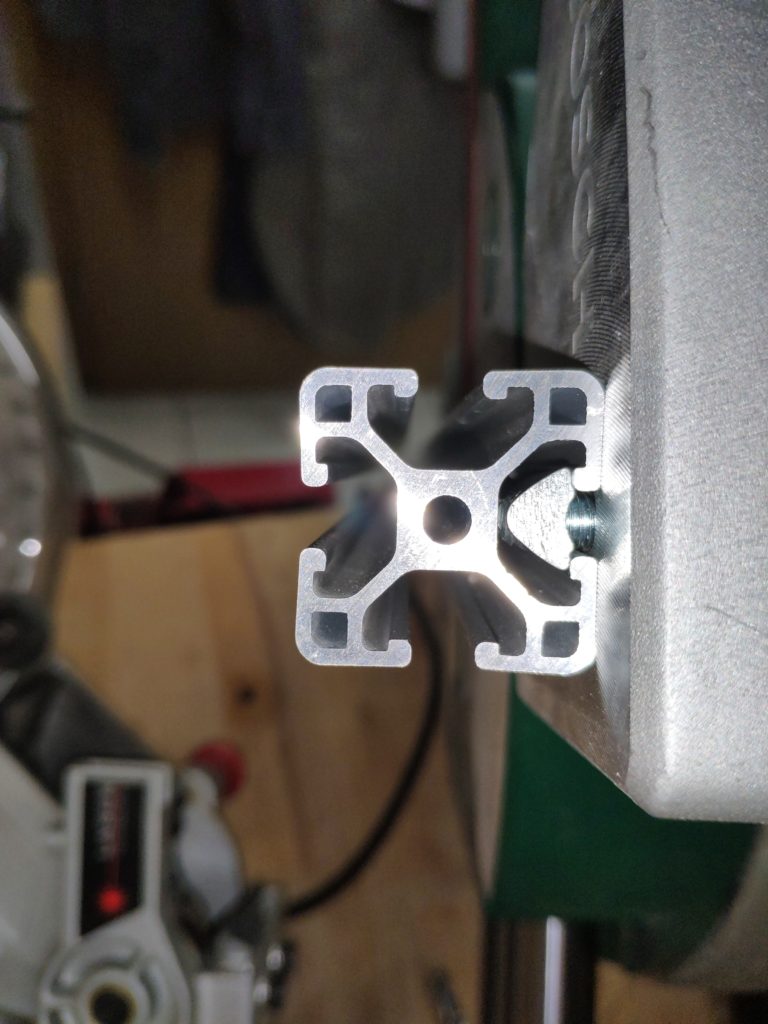
Es ist unbedingt darauf zu achten, dass die Schrauben nicht den Grund der Profilnut berühren. Die Fixierung kommt zustande, weil der Nutenstein auf das Profil aufgepresst wird und nicht weil die Schraube gegen den Nutgrund gedreht wird! Im folgenden Bild noch die verwendeten Nutensteine.
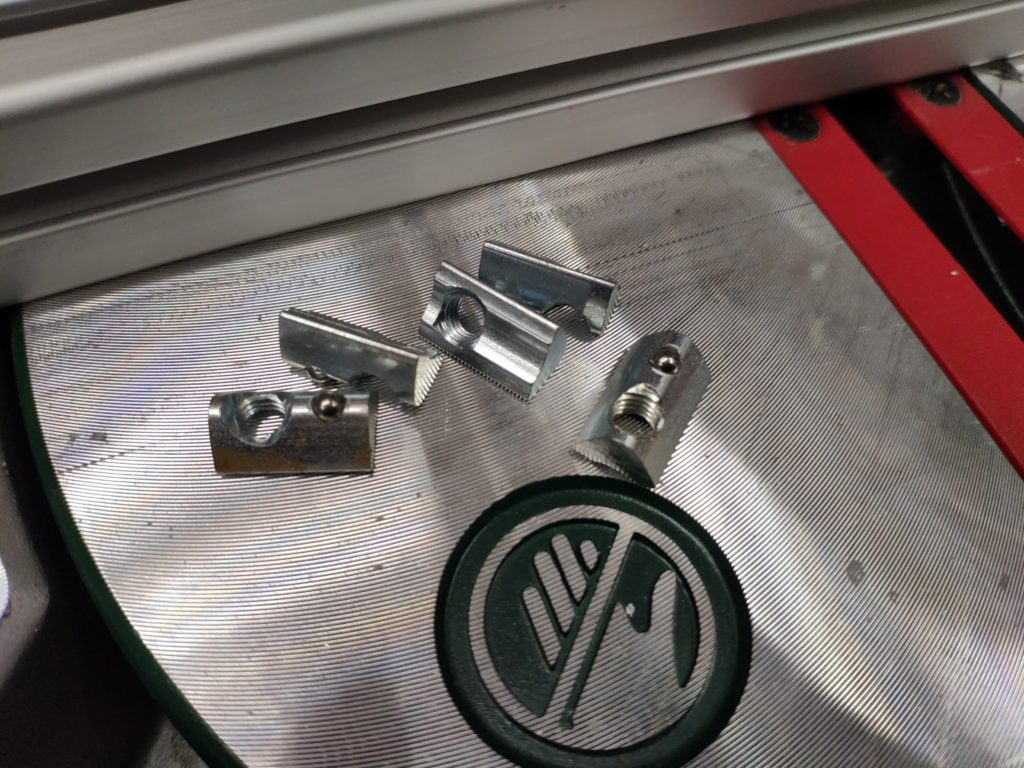
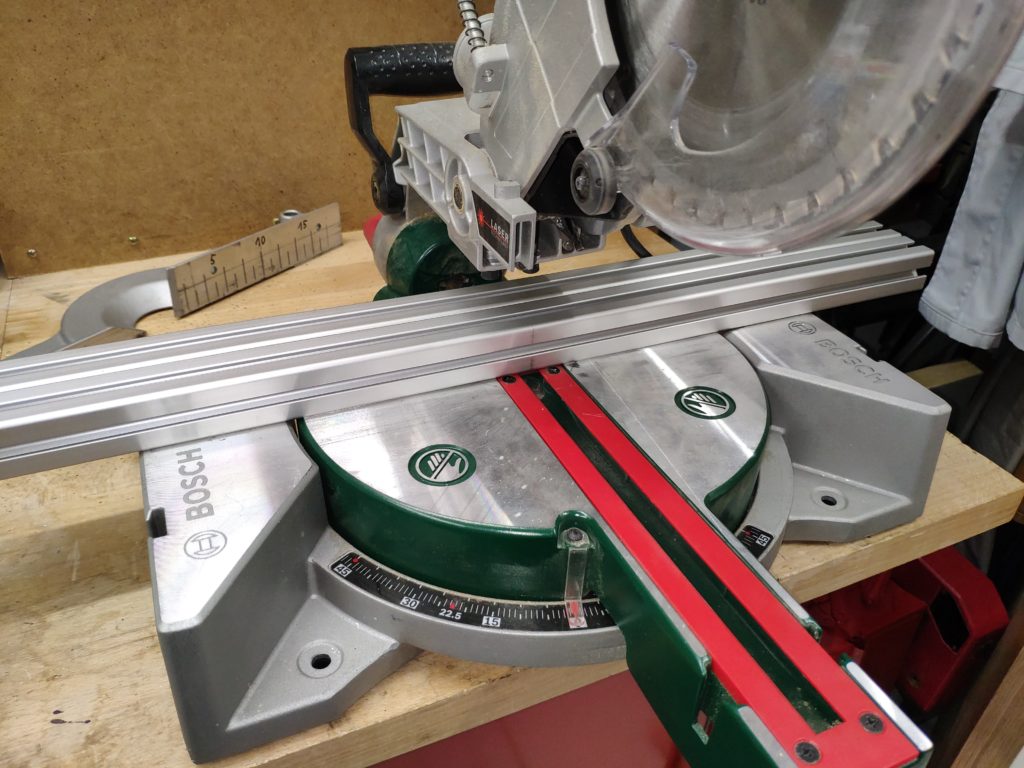
Und wie wird jetzt das Werkstück befestigt? Ganz einfach mit Zwingen.
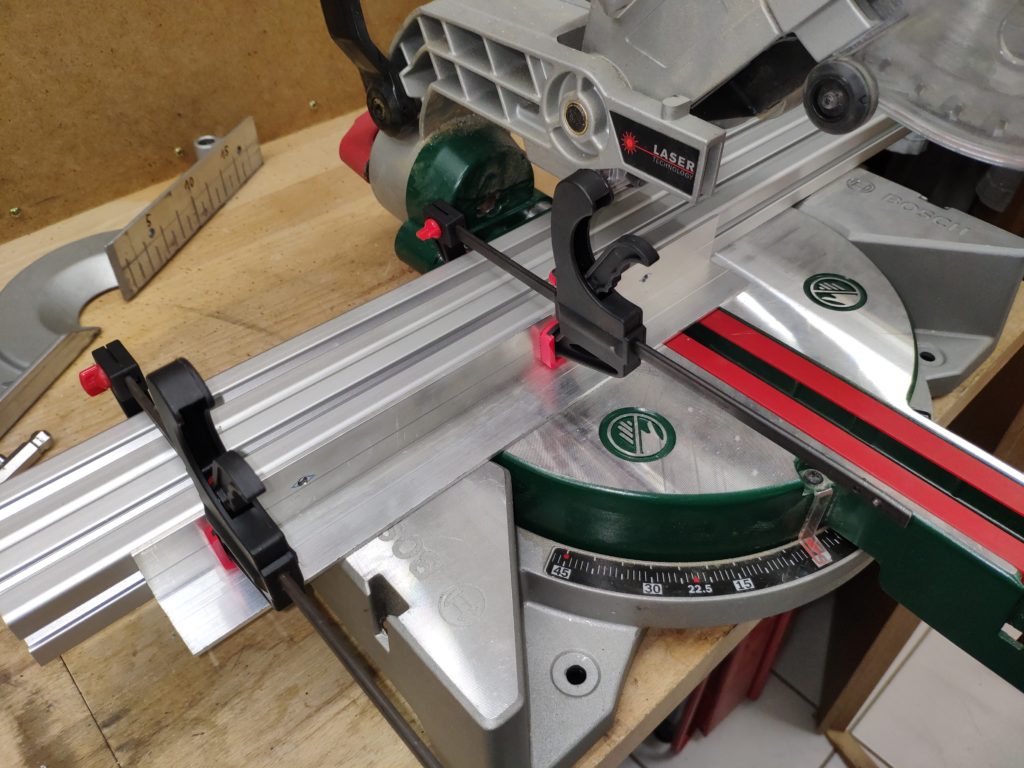
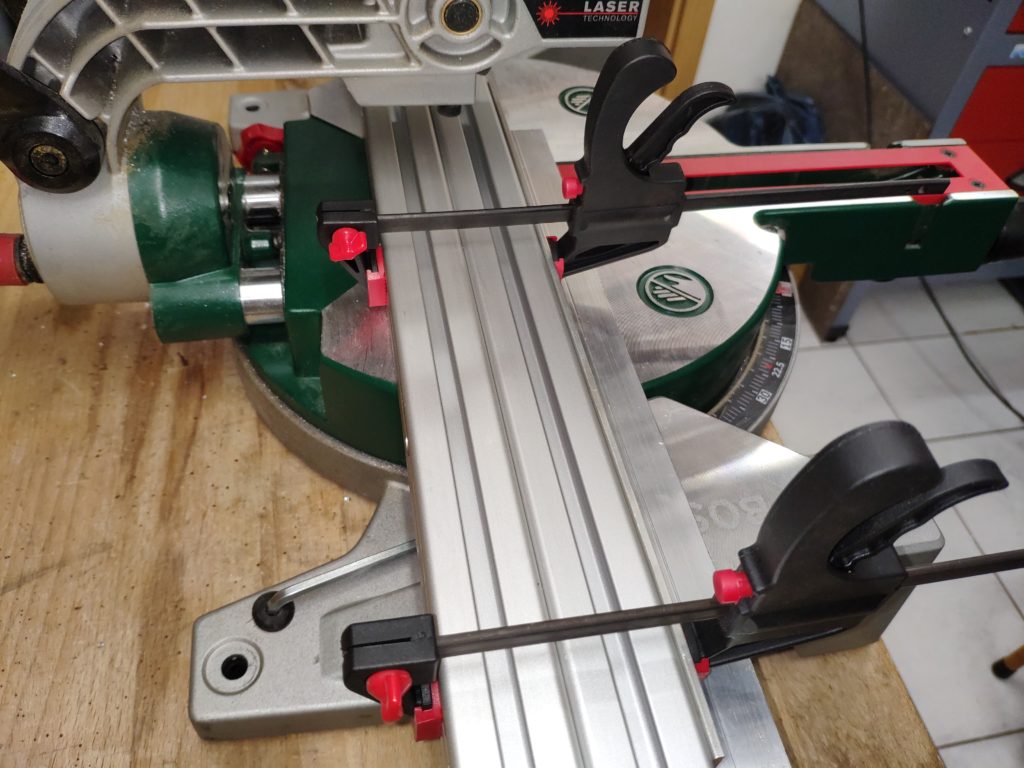
Schon weiter oben habe ich den Hinweis gegeben, dass das vordere Profil etwas Material opfern muss. Die Stabilität wird vom hinteren Profil übernommen. Der Moment des Opferns war da. Die Maschine wurde eingeschaltet und der komplette Weg durch fahren.
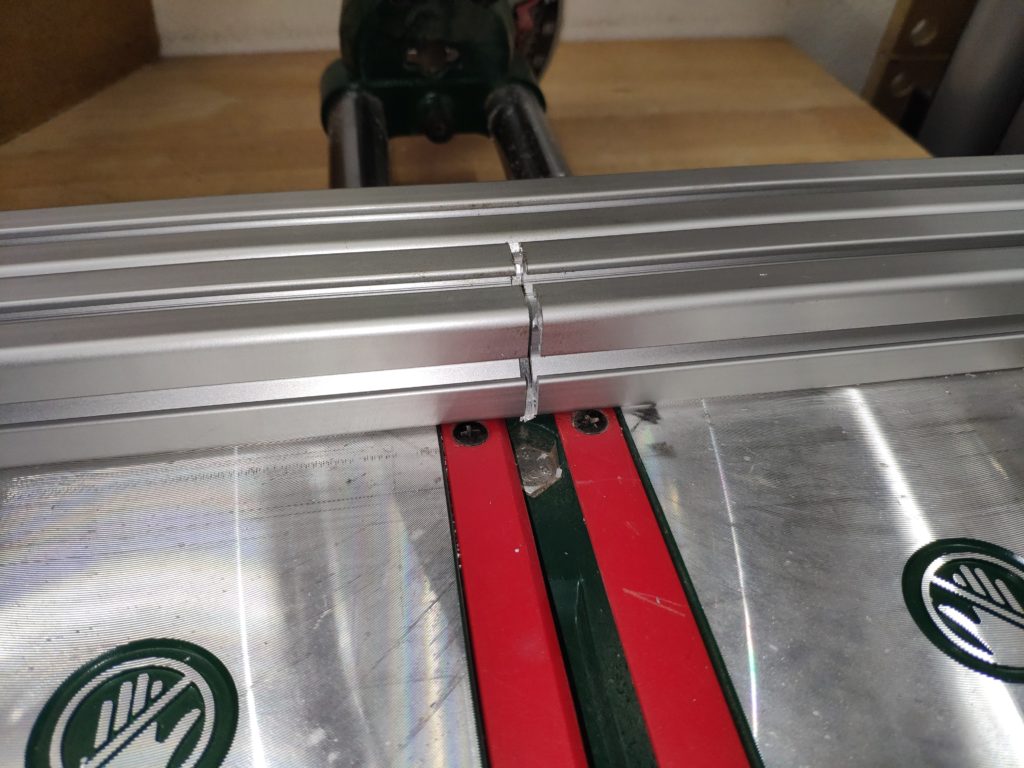
Soweit – so gut! Wenn der Tisch jetzt gedreht wird um eine Gehrung zu sägen, wird sogar noch mehr geopfert. Irgendwann fehlt ein Dreieck.
Bei diesen Gedanken wurde mir bewusst, dass ich etwas übersehen hatte: Der Tisch ließ sich so nämlich gar nicht mehr drehen. Das kam dadurch, dass der Tisch die gleiche Höhe hat wie die Randflächen auf die das Profilpärchen aufgepresst war. Damit fehlte natürlich die Beweglichkeit. Der Tisch saß fest. Wieder demontieren!
Ich markierte zunächst mal die Position des Drehtisches um später sehen zu können, welchen Bereich ich bearbeiten muss. Die originale Anlegeleiste hat im Bereich des Drehtisches eine Aussparung von knapp zwei Millimetern.
Ich packte also mein Profilpärchen auf die Fräse und nahm im bezeichneten Bereich 1mm Material ab.
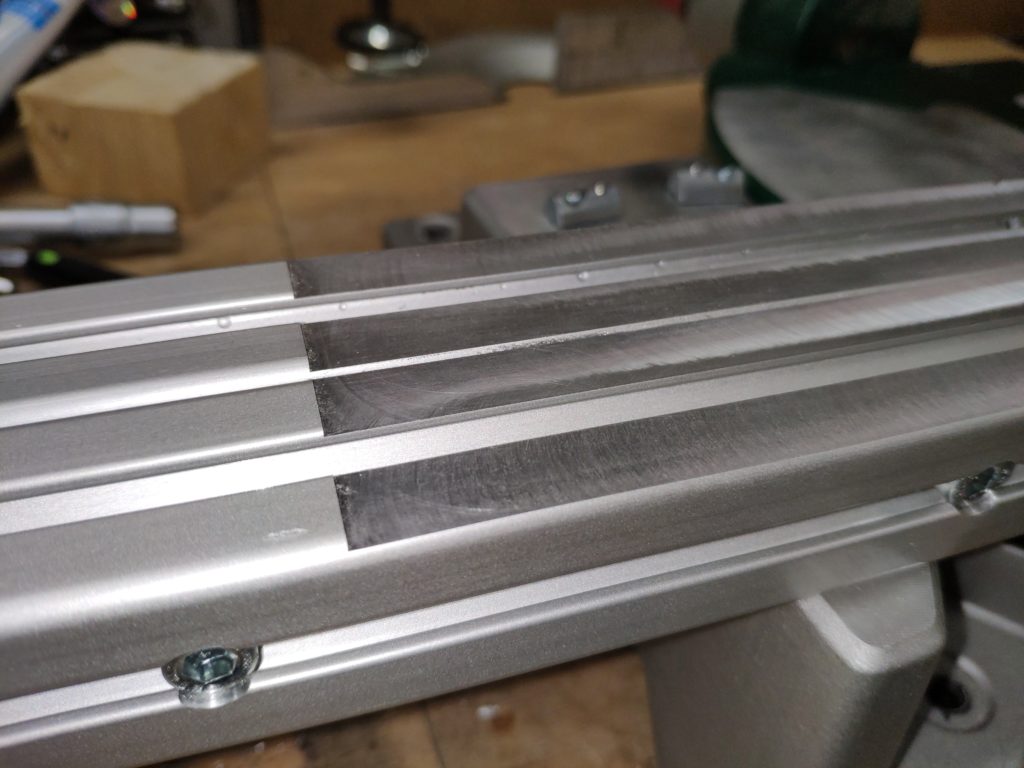
Das hat zwar massiv Aluminiumspäne über meine Fräse und ihr Umfeld verteilt, ging aber andererseits auch sehr schnell und einfach von der Hand. Leider kann ich meine Werkstatt nicht mal richtig reinigen, da mein Nass-Trockensauger vor zwei Tagen, – nämlich gerade bei den Arbeiten zu diesem Artikel, einen Motorschaden erlitten hat. Ein Neuer ist unterwegs.
Ich habe dann alles wieder zusammengebaut.
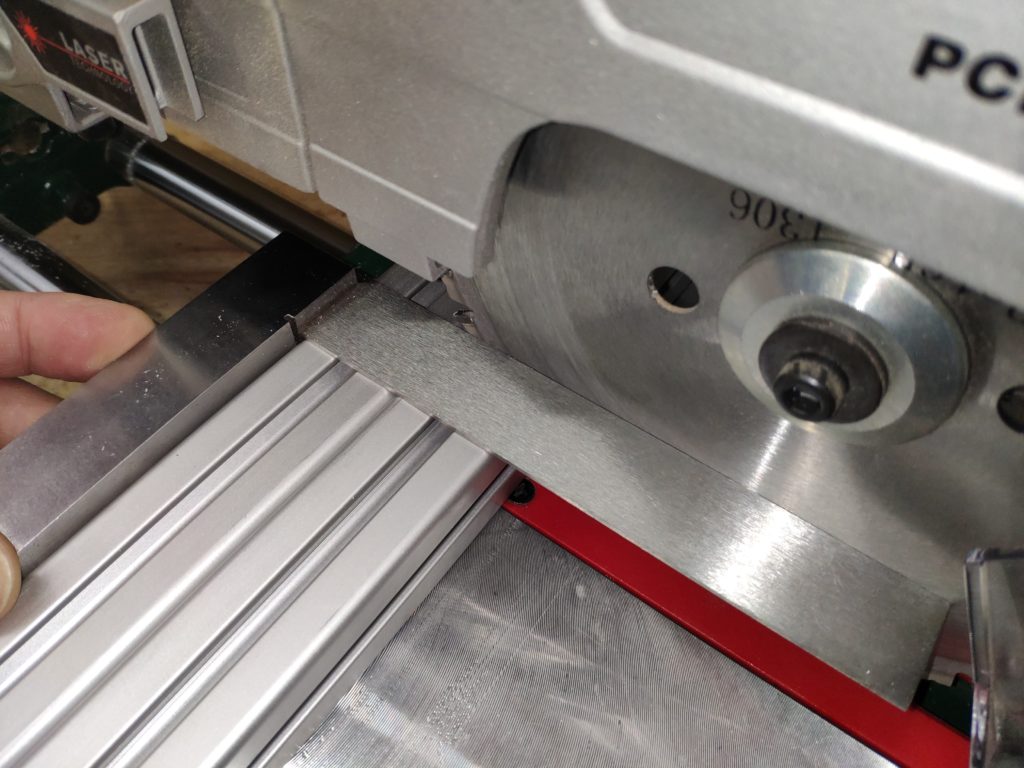
Beim Fixieren der neuen Anlegeleiste habe ich darauf geachtet, dass der Winkel auch stimmt. Der Tisch wurde auf 0° eingestellt und dann die Profilrückseite mit einem Winkel gegen das Sägeblatt ausgerichtet. Ich gehe mal davon aus, dass wenn die Profilrückseite stimmt auch die Vorderseite stimmt. Es war halt einfacher zu messen.
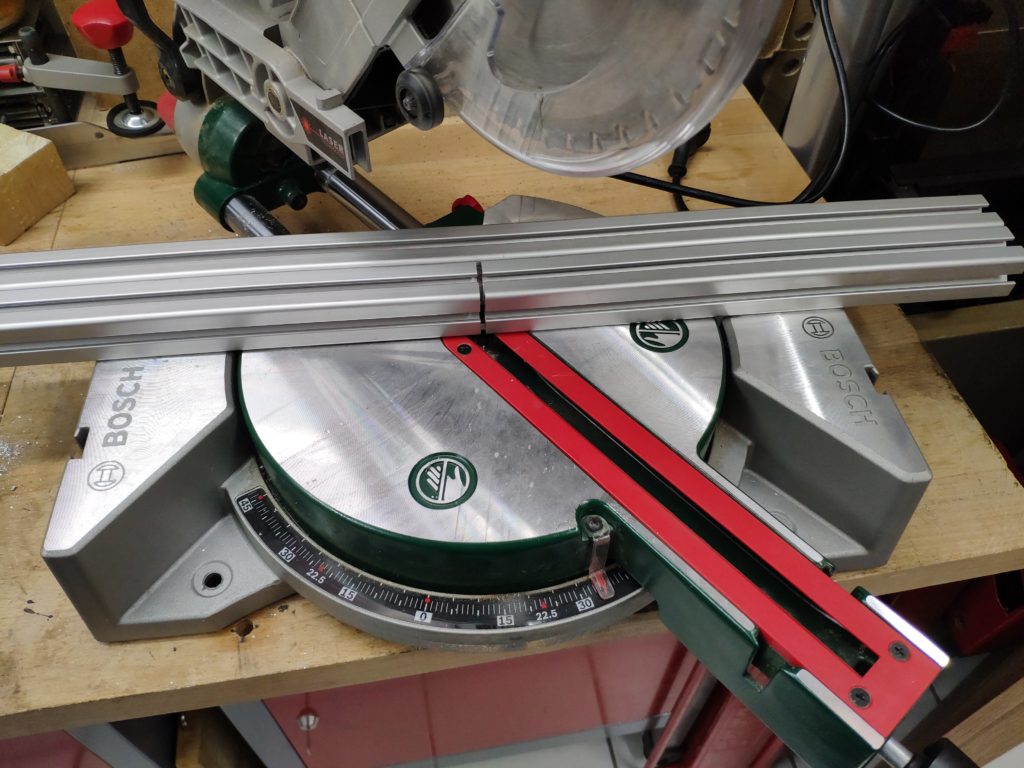
Es war nicht anders zu erwarten: Der Tisch lässt sich jetzt problemlos drehen.
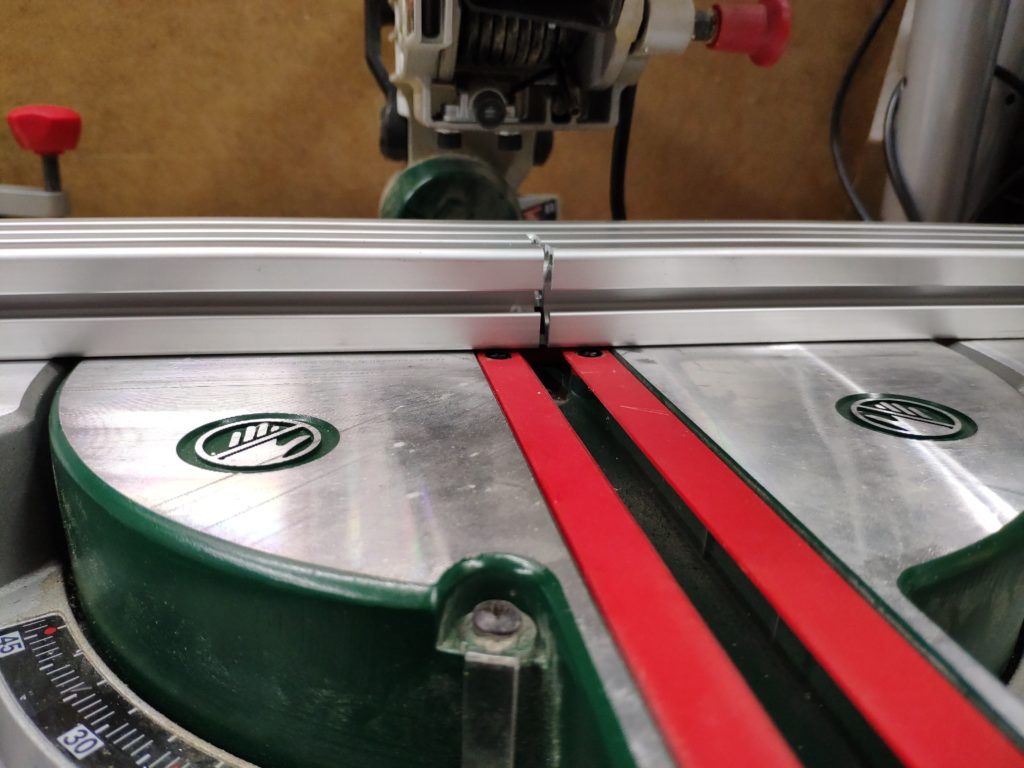
Mit einem letzten Detailbild ist dieser Beitrag vollständig. Wer sich jetzt fragt, warum ich denn den dreieckigen Ausschnitt aus dem Profil nicht sofort ausgesägt habe, den muss ich auf einen späteren Zeitpunkt mit einem neuen Artikel vertrösten. Ich habe da nämlich noch eine Idee. Ich bin noch nicht fertig . . .