Kommen wir zum spannenden Teil. Der Druckerbausatz wird ausgepackt, die Teile werden begutachtet und dann wird gebaut.
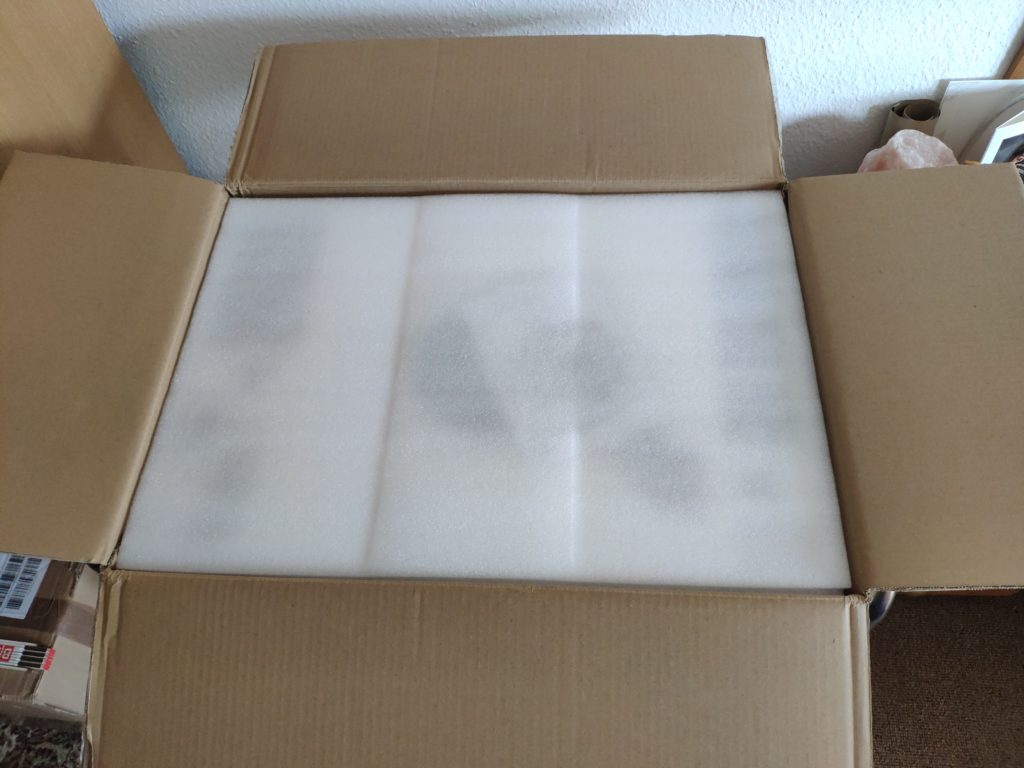
Nach dem Öffnen der Umverpackung kommt schon Schaumstoff zum Vorschein. Aber die erste Lage Teile scheint schon durch.
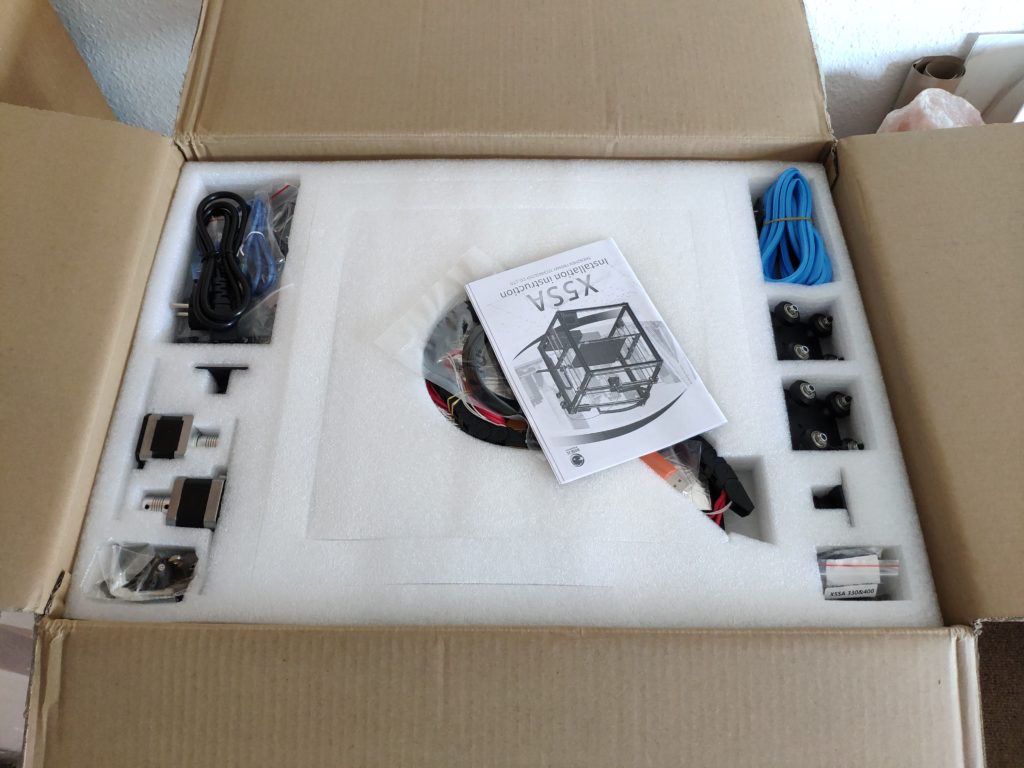
Alles ist gut gesichert verpackt. Bei der langen Reise von China nach Deutschland sicherlich keine schlechte Idee.
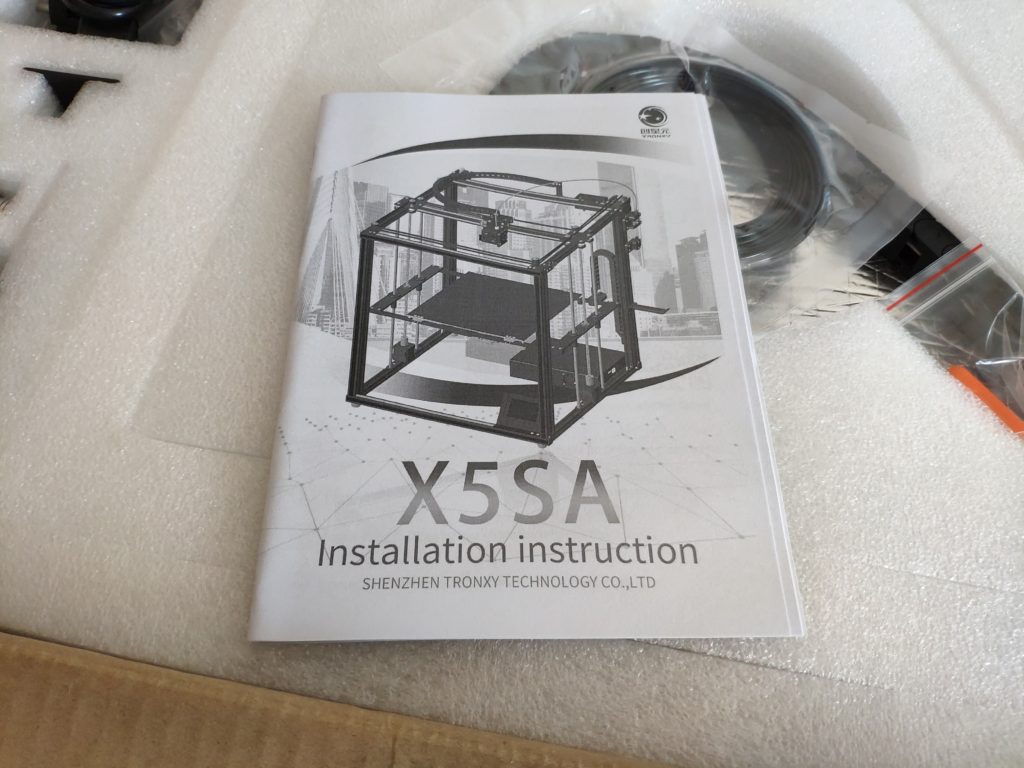
Ich hatte an anderer Stelle gelesen, dass eine Aufbauanleitung fehlen würde. Wie man sieht, war die aber bei mir vorhanden. Das rein monochrom erstellte Heftchen scheint komplett aus dem Fotokopierer zu kommen und wurde danach mit einfachen Heftklammern zusammengefügt. Da ich aber einen funktionierenden Drucker haben wollte und kein Hochglanzprospekt ist mir das egal.
Die Anleitung zeigt zunächst die üblichen Safety instructions. Dann folgen die Abschnitte …
- Machine parameter
- Machine view
Ein Bild der Maschine mit Bezeichnung fast aller Bestandteile. Gerade für den Aufbau und den Neuling eine wichtige Quelle - Package list
natürlich empfiehlt es sich mal nachzuschauen ob alles geliefert wurde - Product assmbly
in 13 Schritten wird der Aufbau beschrieben - Operation instructions
nicht gar nicht mal so schlechter Startpunkt für den Betrieb
die Dialoge auf dem Display werden erklärt - Software installation instruction
hier geht es um die mitgelieferte Slicing-Software - General problems
neuen recht typische Fehler werden analysiert
Die Anleitung lebt hauptsächlich von Bildern. Gerade beim Aufbau könnten die Bilder gern ein wenig größer und aussagekräftiger sein.
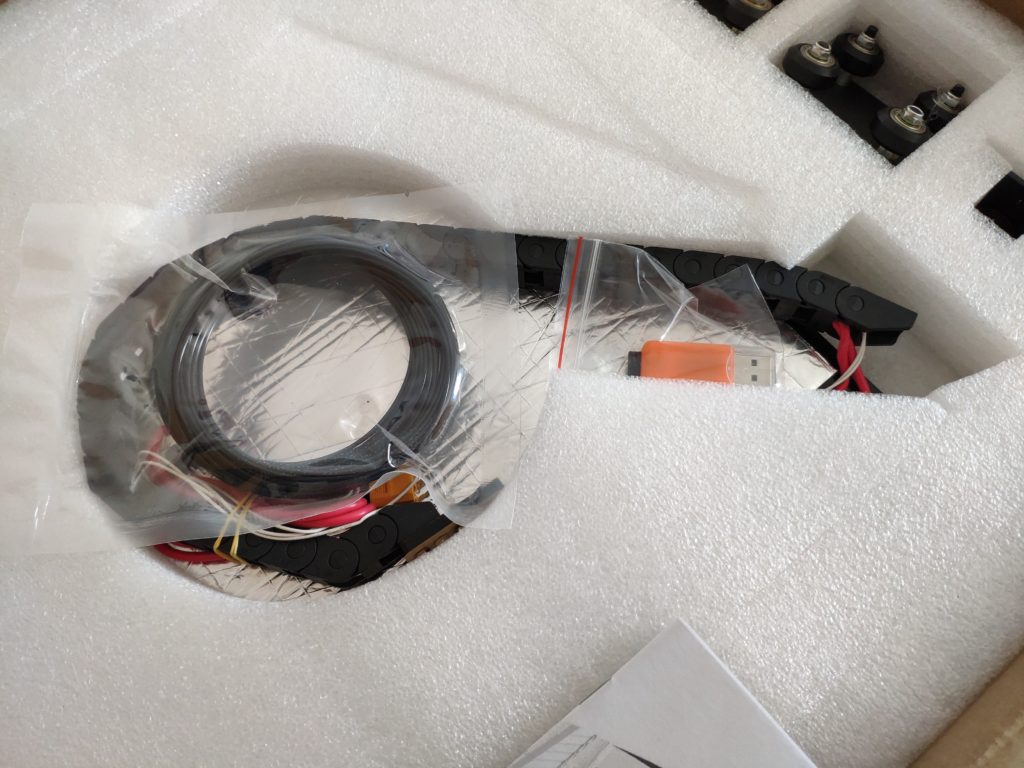
Die Energiekette für das beheizte Druckbett.
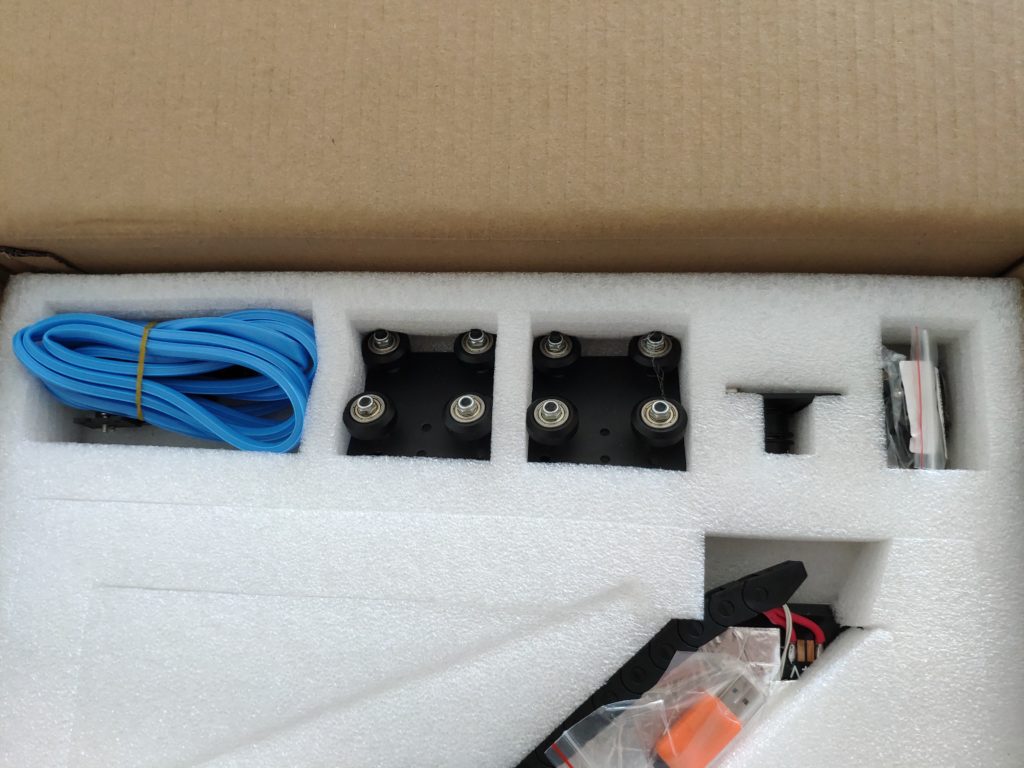
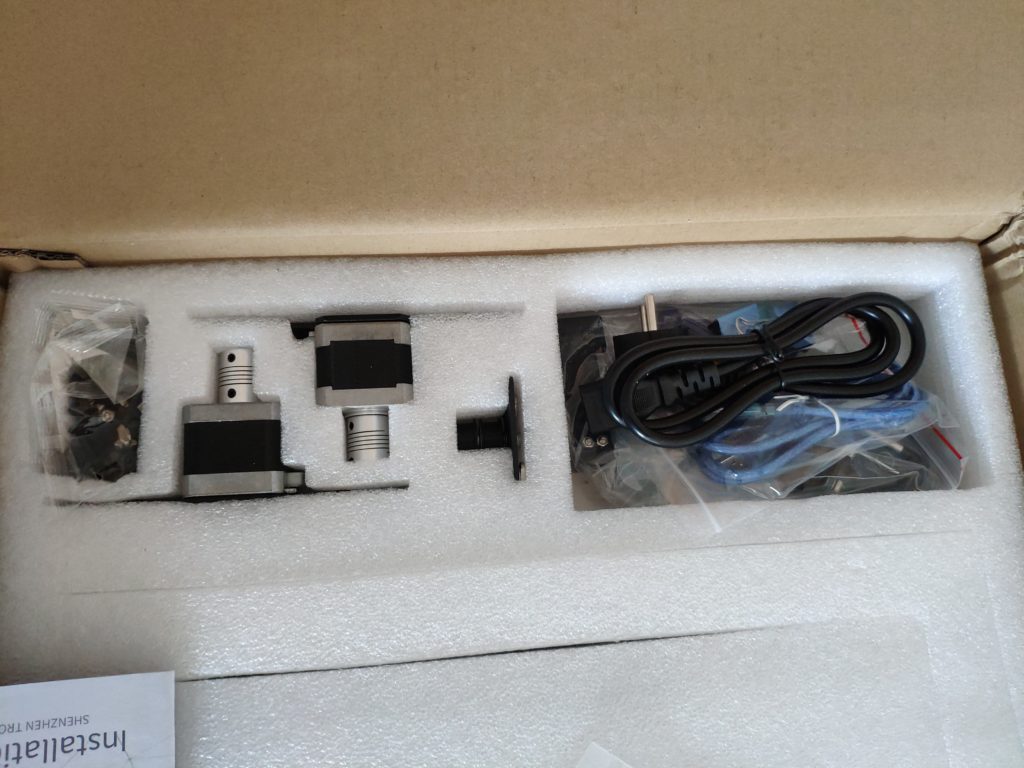
Tronxy hat sich Mühe gegeben die Teile übersichtlich anzuordnen.
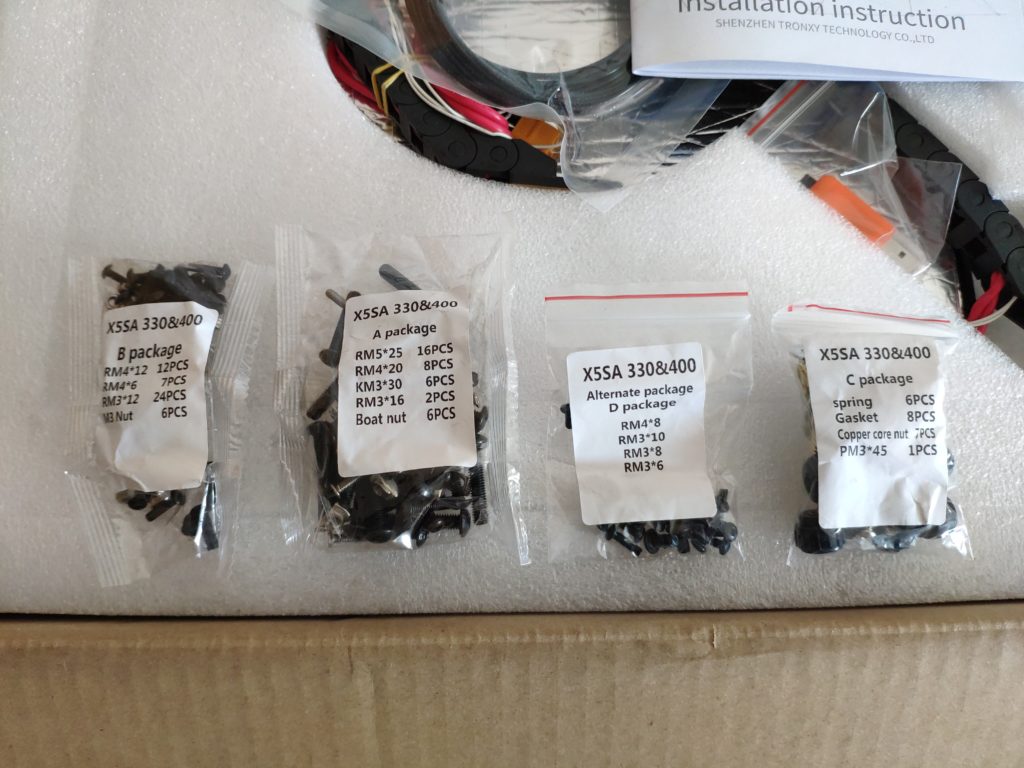
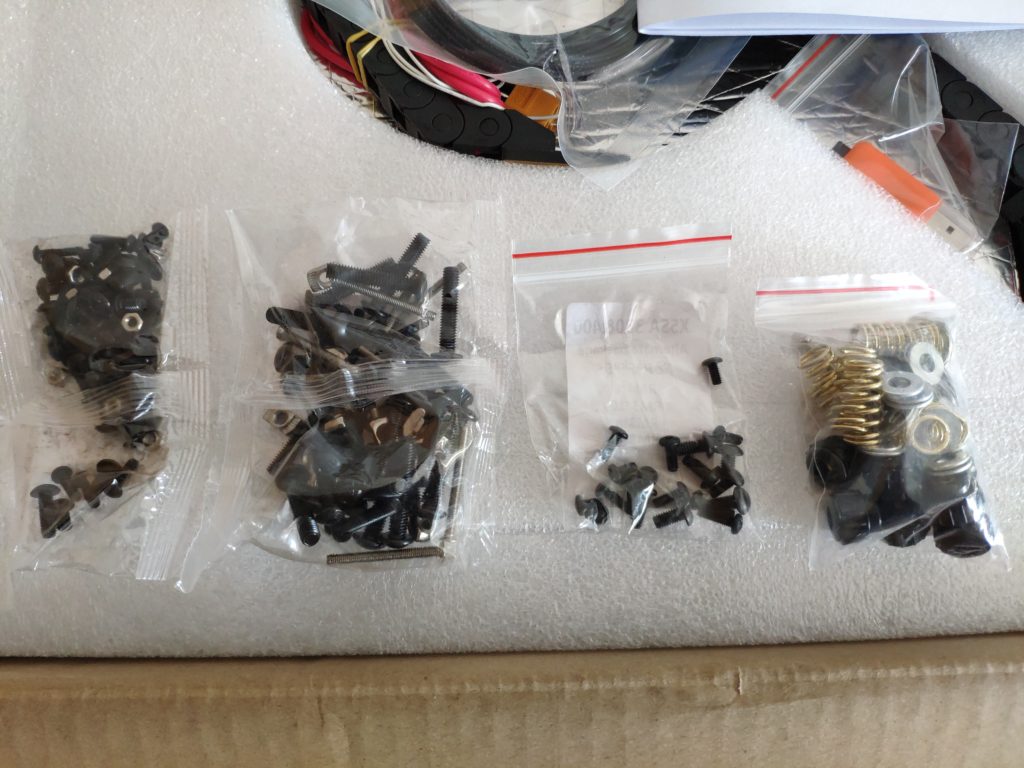
Nicht alle mitgelieferten Schrauben werden verwendet.
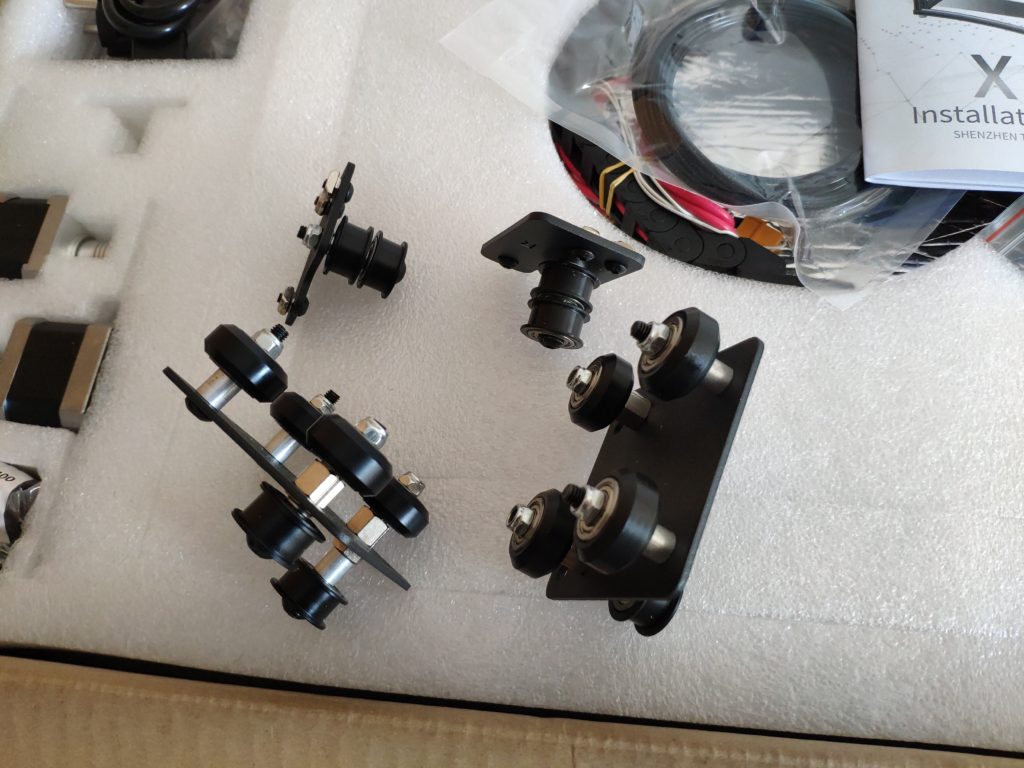
Womit wir dann auch gleich bei den meist kritisierten Teilen angekommen sind. Ich kann mich der allgemeinen Kritik nur anschließen. Zumindest die Lager für die Riemenführung sind extrem schlecht und lassen sich nur schwer drehen. Die Lager der Linearführung sind dagegen gar nicht mal so schlecht.
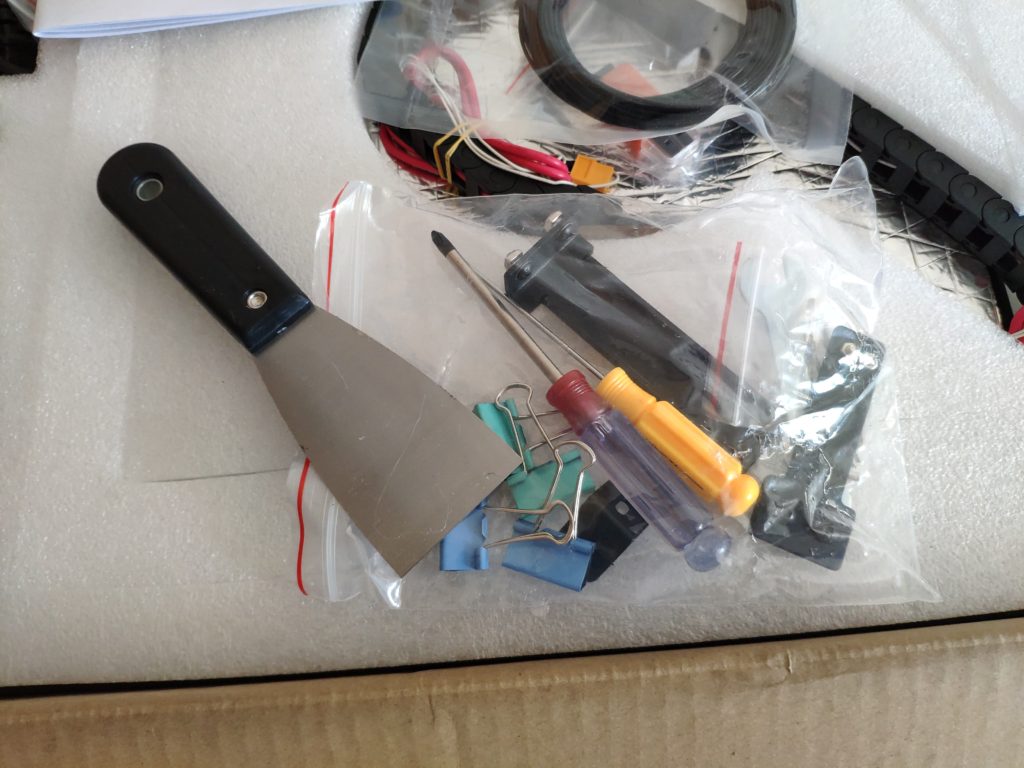
Werkzeug für den Aufbau und den Betrieb wird auch mitgeliefert. Das Werkzeug hat akzeptable Qualität. Es reicht aber nicht für den Aufbau aus. Ein Seitenschneider, ein Messer und wenigstens eine gute Zange sind auch noch notwendig.
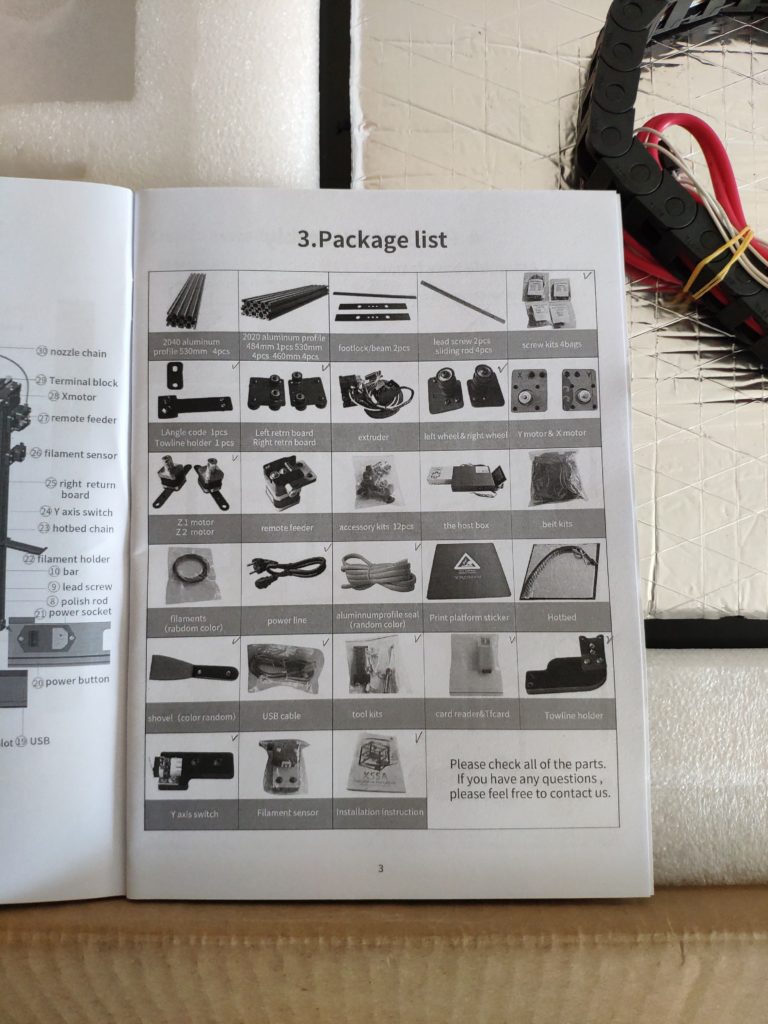
Gefundene Teile habe ich in der Liste abgehakt.
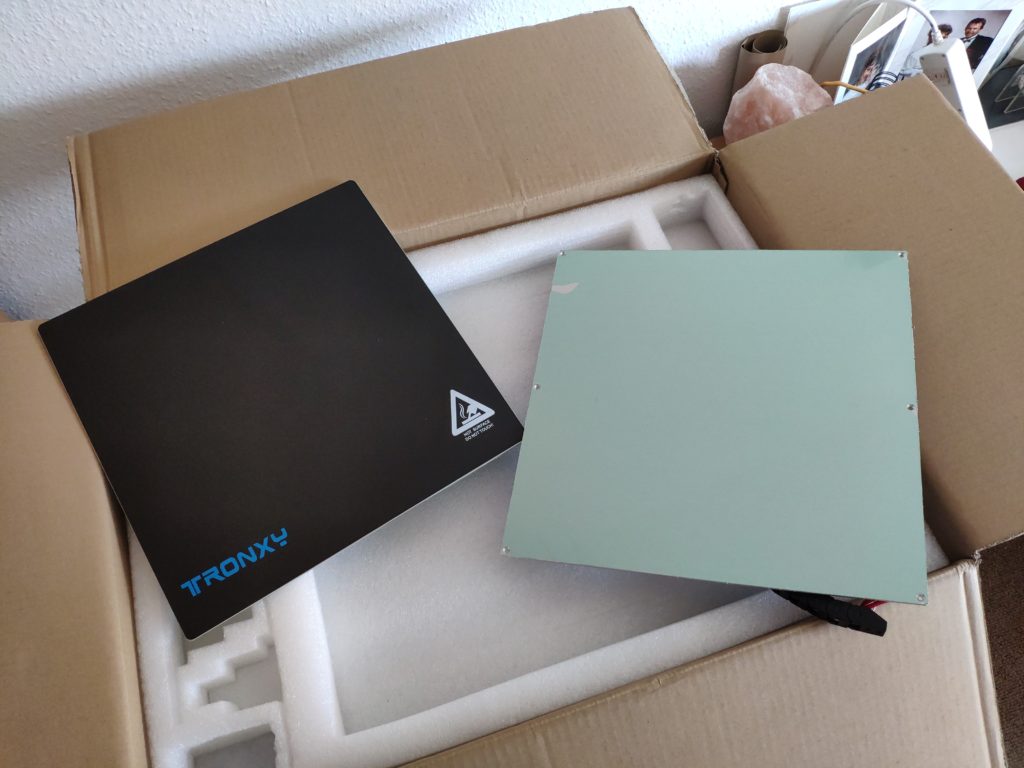
Das beheizte Druckbett (rechts) und eine abnehmbare Druckplatte mit spezieller aufgeklebter Beschichtung.
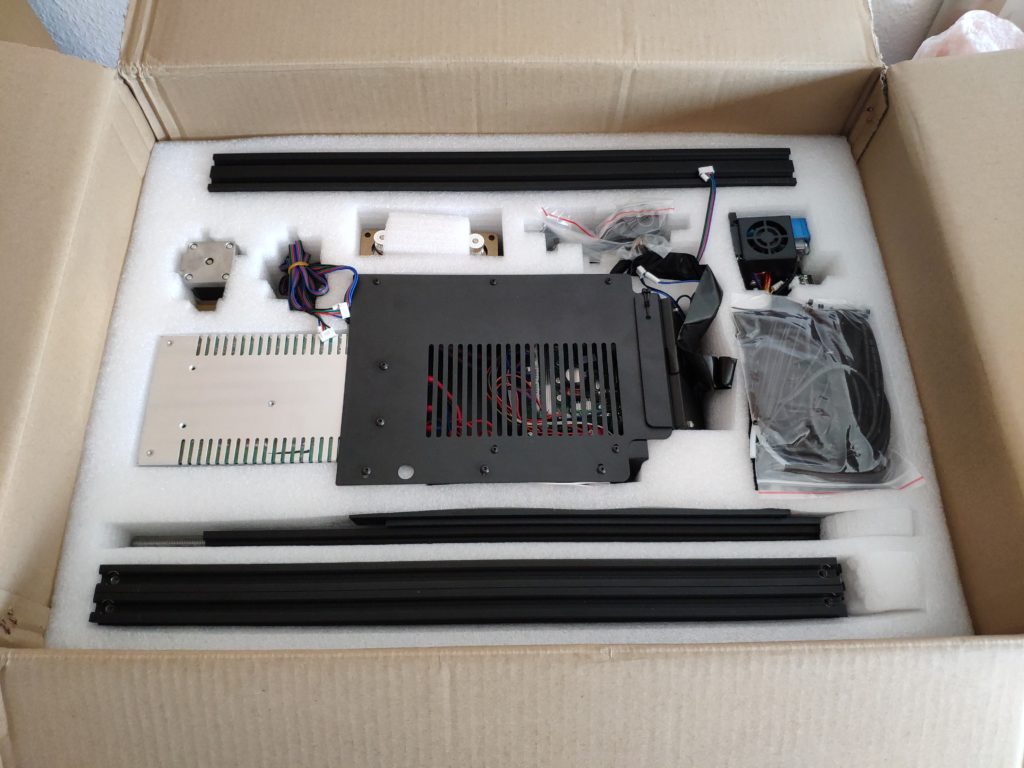
Zweite Etage
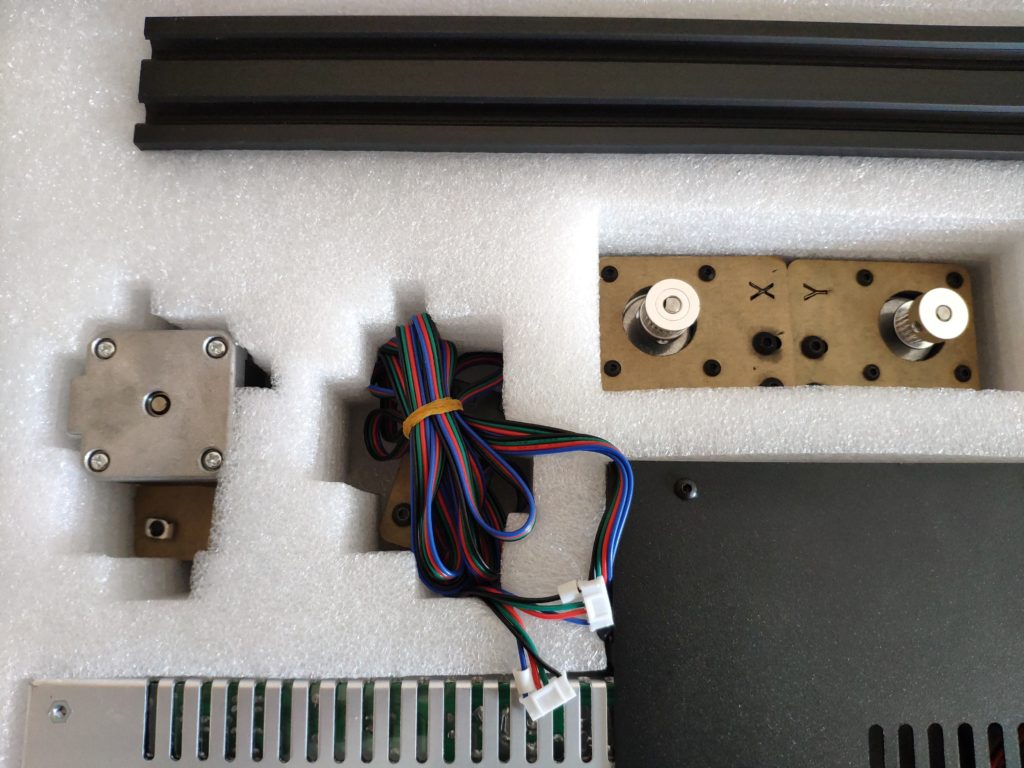
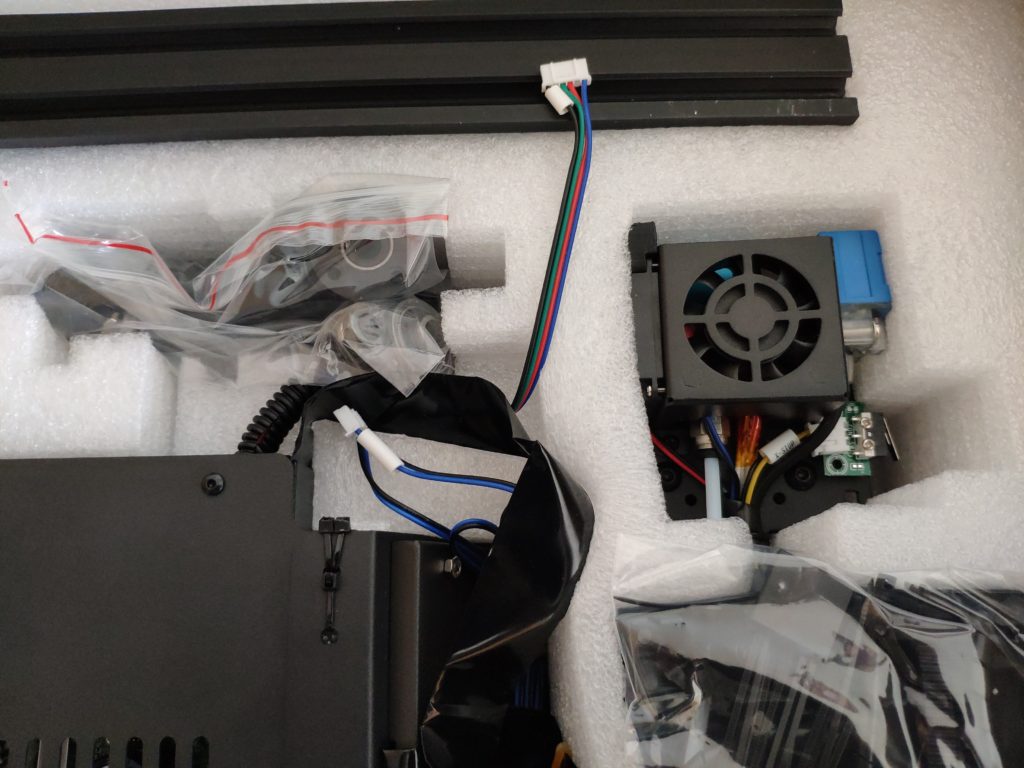
Sicherlich am spannendsten auf der rechten Seite ist das Hotend, das als komplett montiertes Modul kommt.
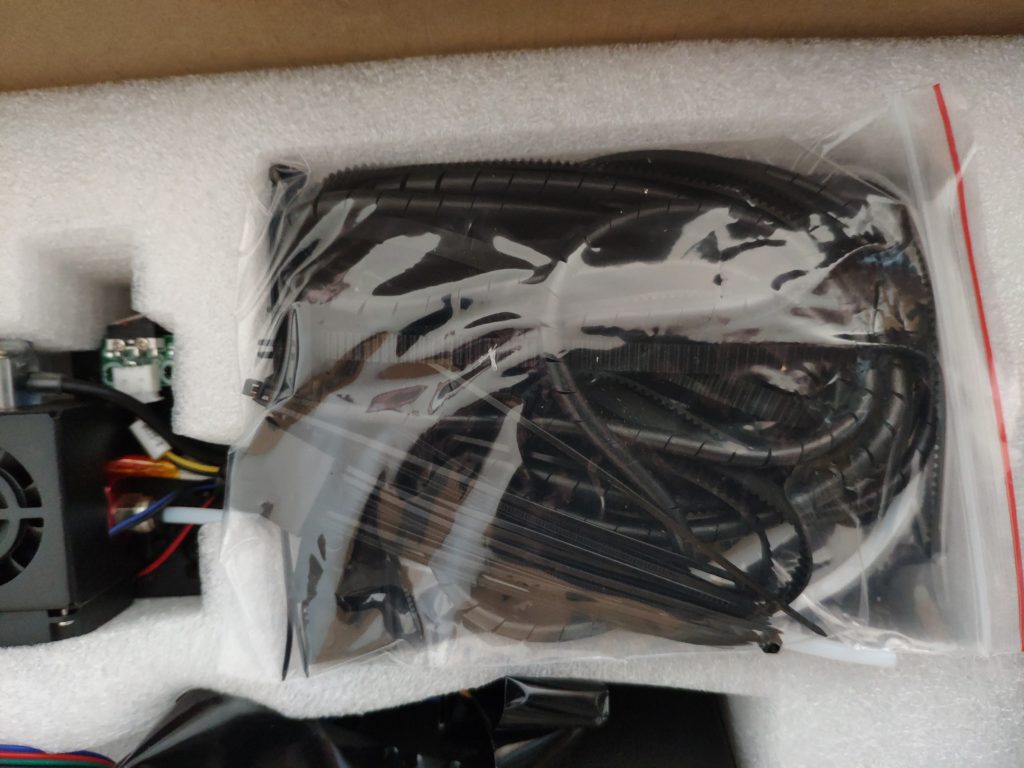
Eine Tüte mit diversen Kunststoffkabelbindern und -schläuchen. Außerdem ein schlicht lächerlicher Vorrat an PLA-Filament.
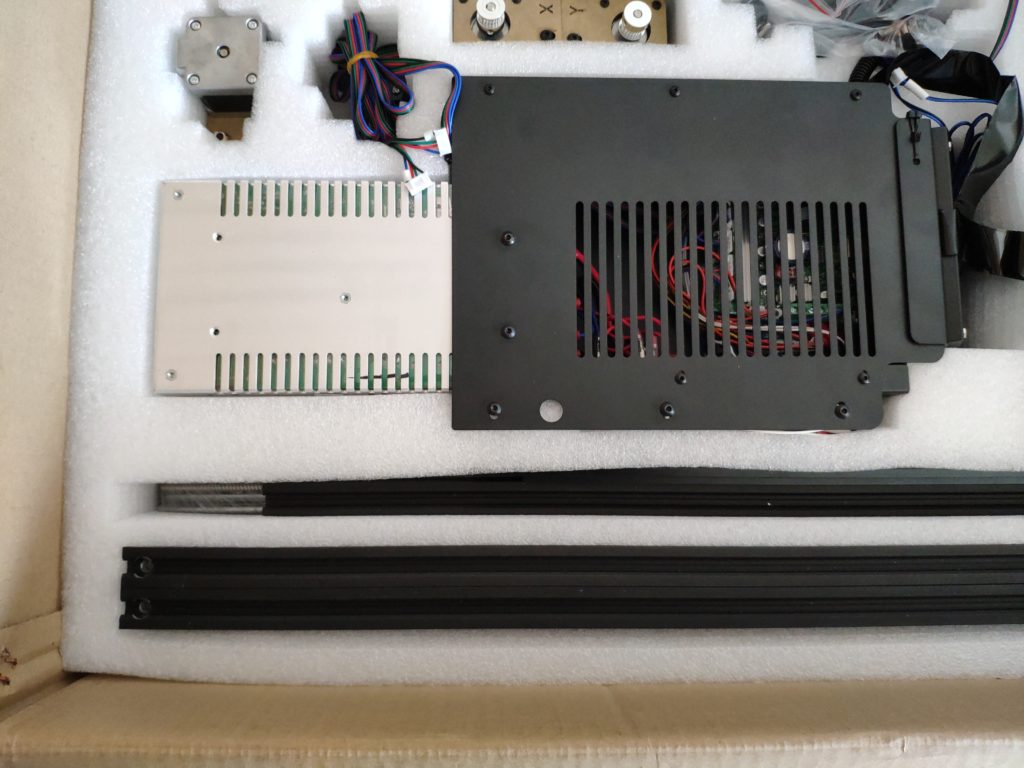
Das Netzteil ist komplett mit der Steuerelektronik als Modul vereint.
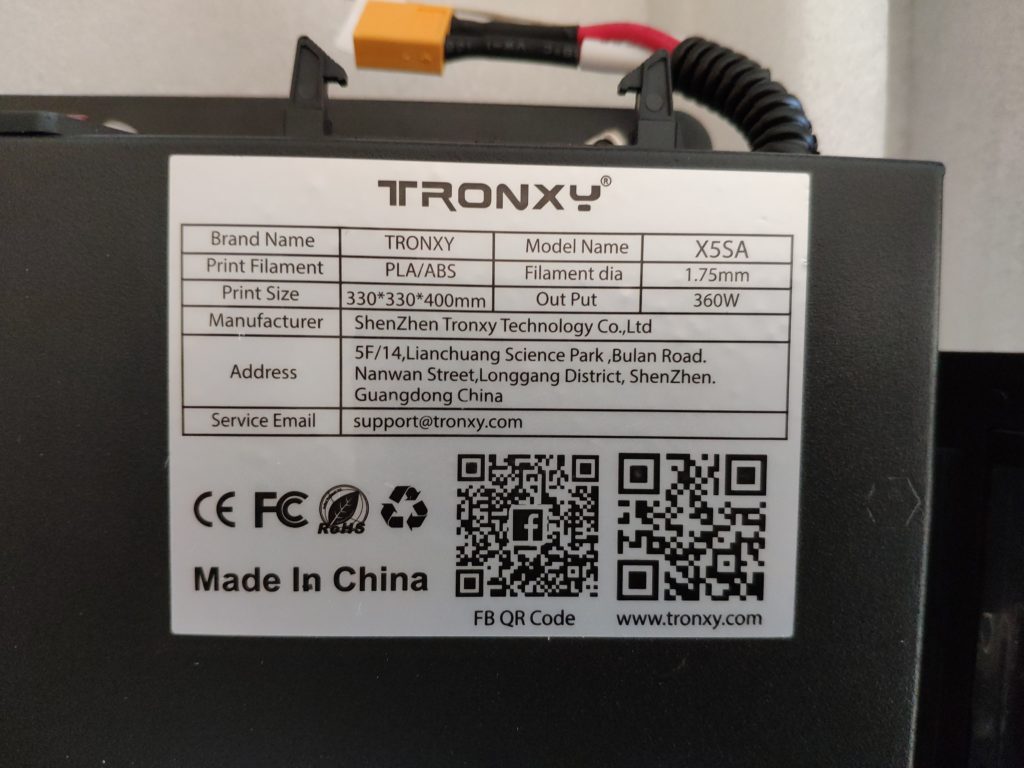
Das Typenschild des Druckers.

Auf dem Karton war nichts von 24 Volt zu lesen, – obwohl bestellt. Glücklicherweise ist das Netzteil aber so ausgewiesen.
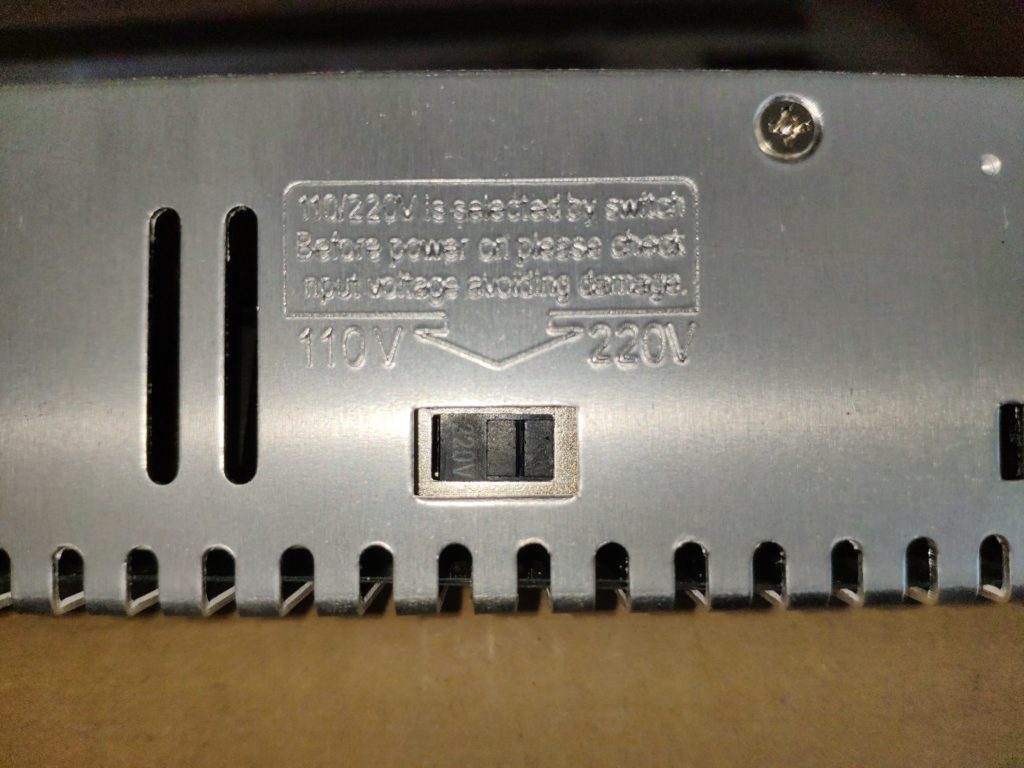
Na ja, – eigentlich haben wir ja etwas mehr als 220V in Deutschland. Aber Hauptsache der Schalter für die Primärspannung ist richtig eingestellt. Das sollte man unbedingt prüfen, sonst kann der Spaß schnell zu Ende sein.
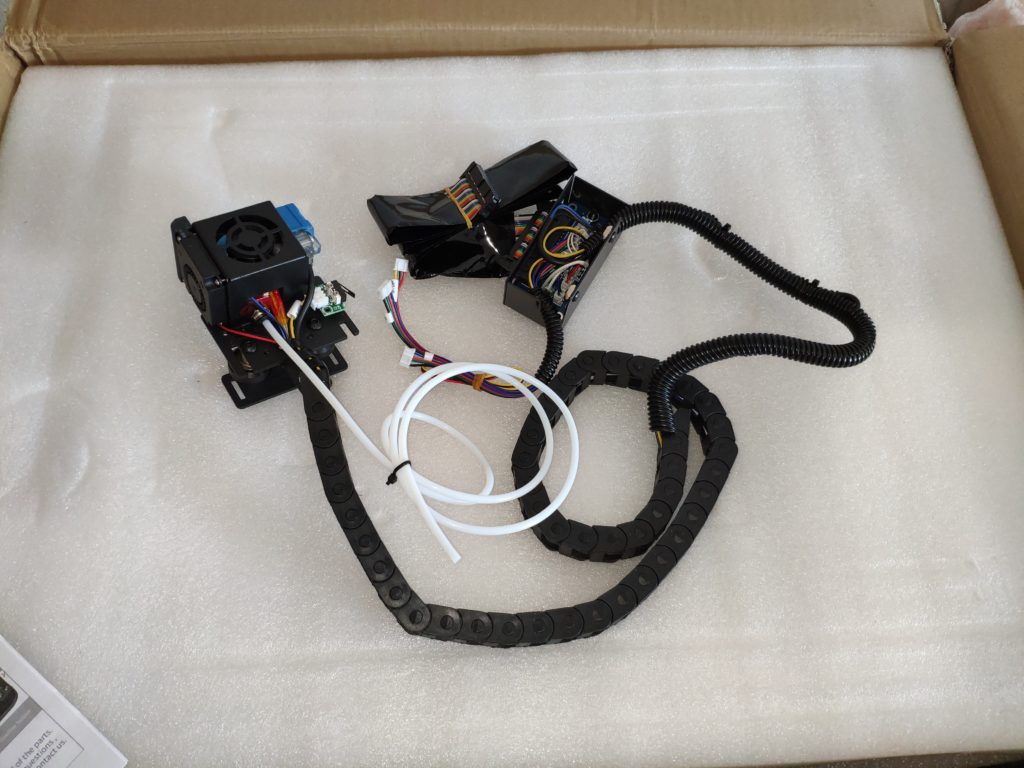
Das Hotend ist wie schon oben bemerkt als komplettes Modul mit angeschlossener Elektronikbox beigelegt.
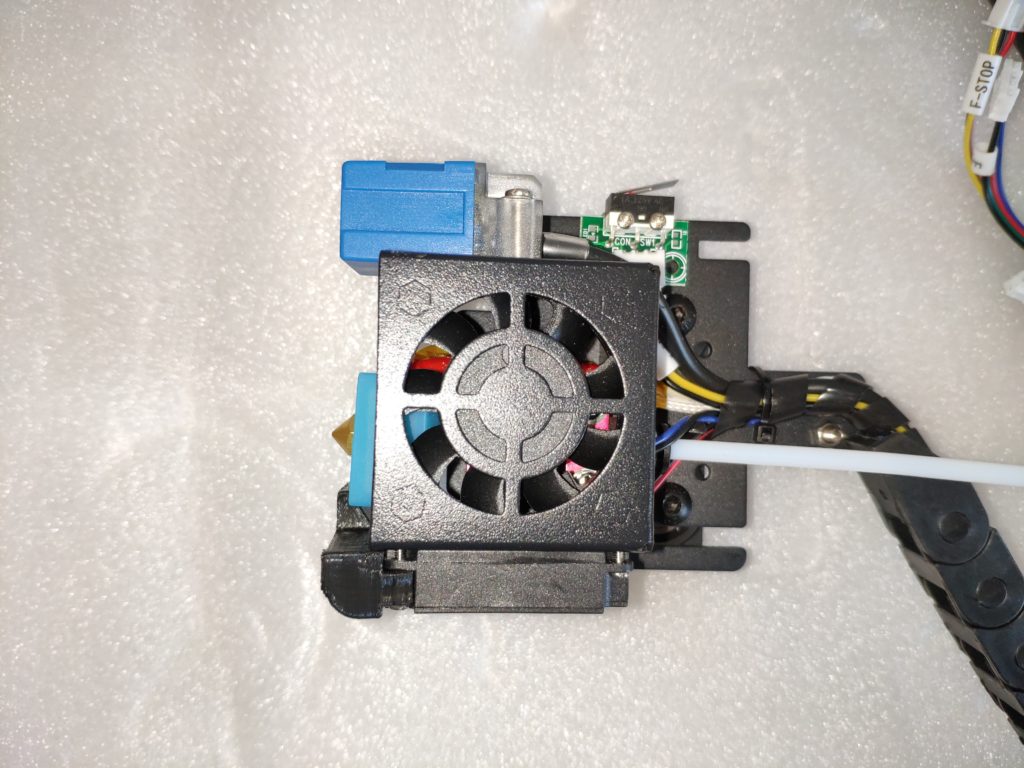
Ventilator zur Hotendkühlung und links oben ist der Abstandssensor zu sehen.
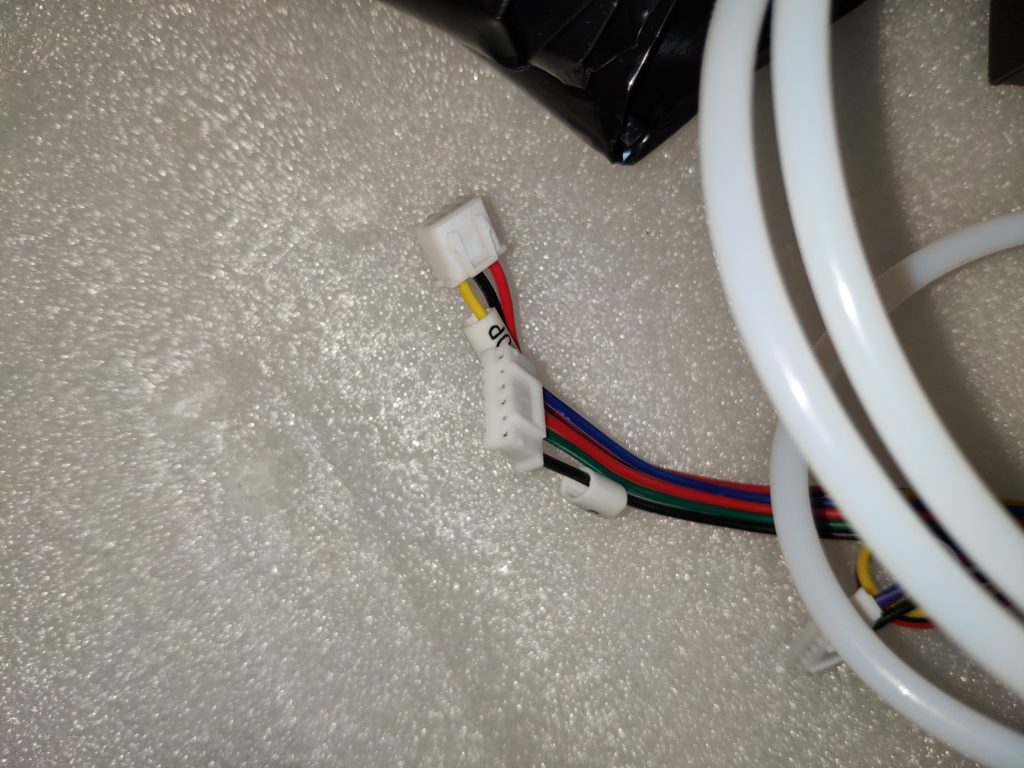
Alle elektrischen Anschlüsse sind fertig mit Steckern ausgelegt. Jeder Steckanschluss ist eindeutig gekennzeichnet. Sehr gut !
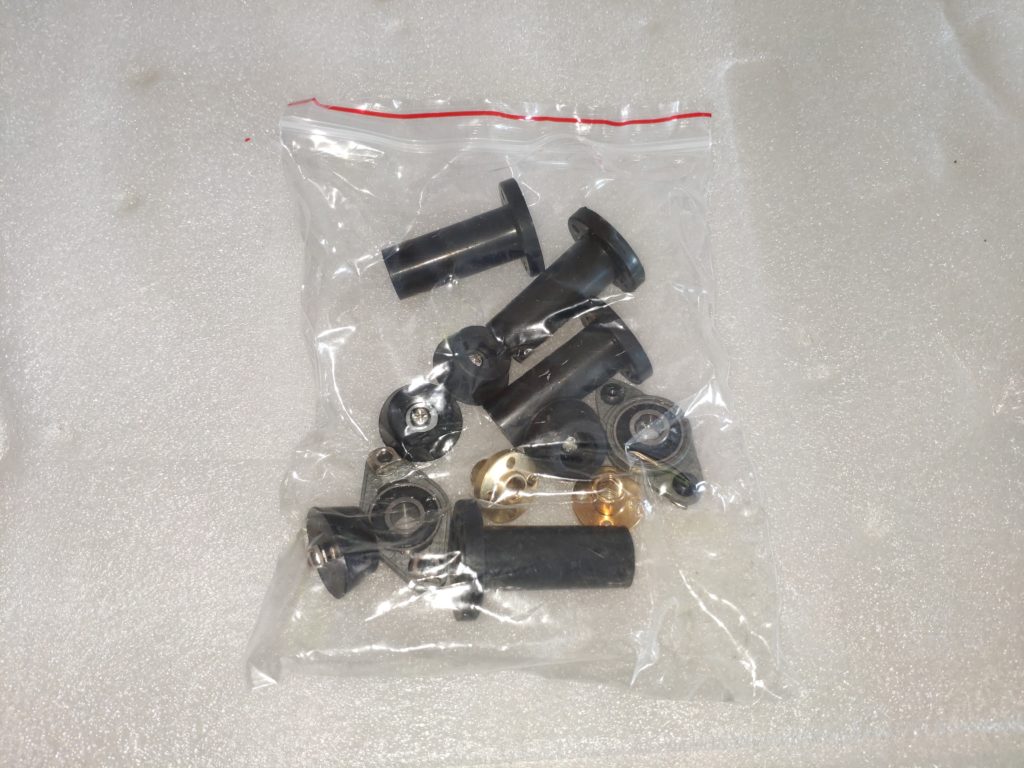
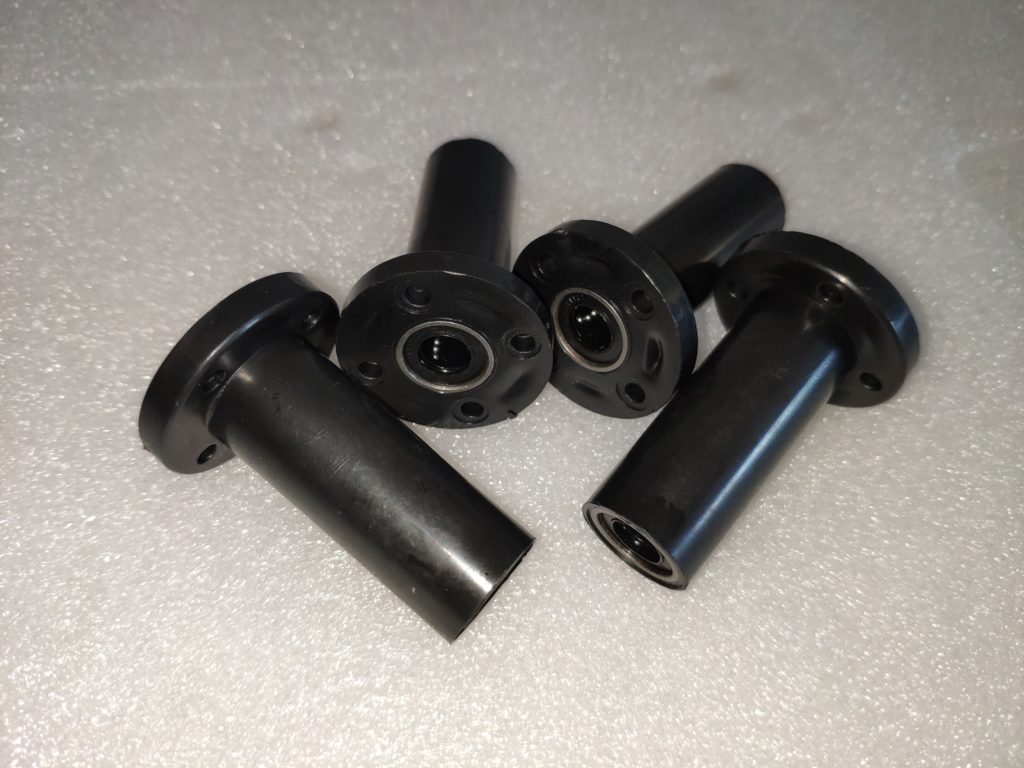
Die Linearlager für die Z-Achse sind tatsächlich aus Kunststoff. Ich konnte aber keinerlei Beschädigung ausmachen und ehrlich gesagt sehen die Teile vollkommen in Ordnung aus. Die Zeit wird es zeigen. Die Spindelmuttern haben keinen Spielausgleich. Das ist aber eigentlich auch nicht nötig, da sie ohnehin nur von oben belastet sind.
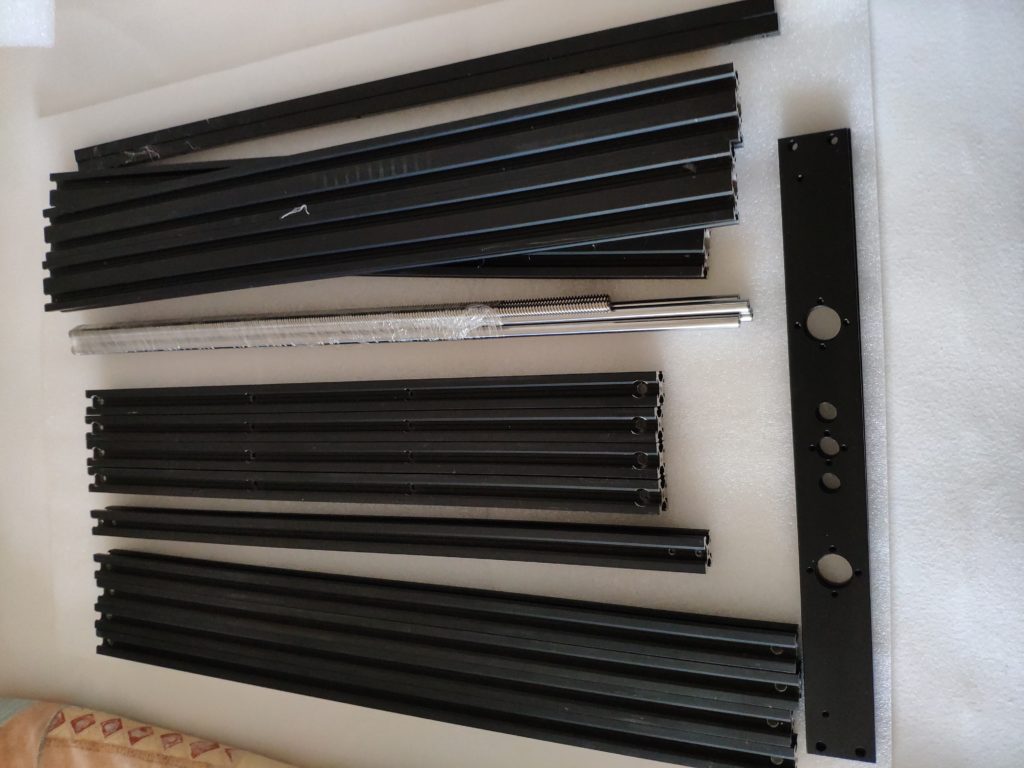
Die Basis des ganzen Druckers bilden natürlich die Aluminiumprofile vom Typ 2020 und 2040. Die Profile sind ordentlich gefertigt und auch akzeptabel an den Schnittkanten. Der Aufbau hat gezeigt, dass die Schnitte auch sauber im Winkel sind.
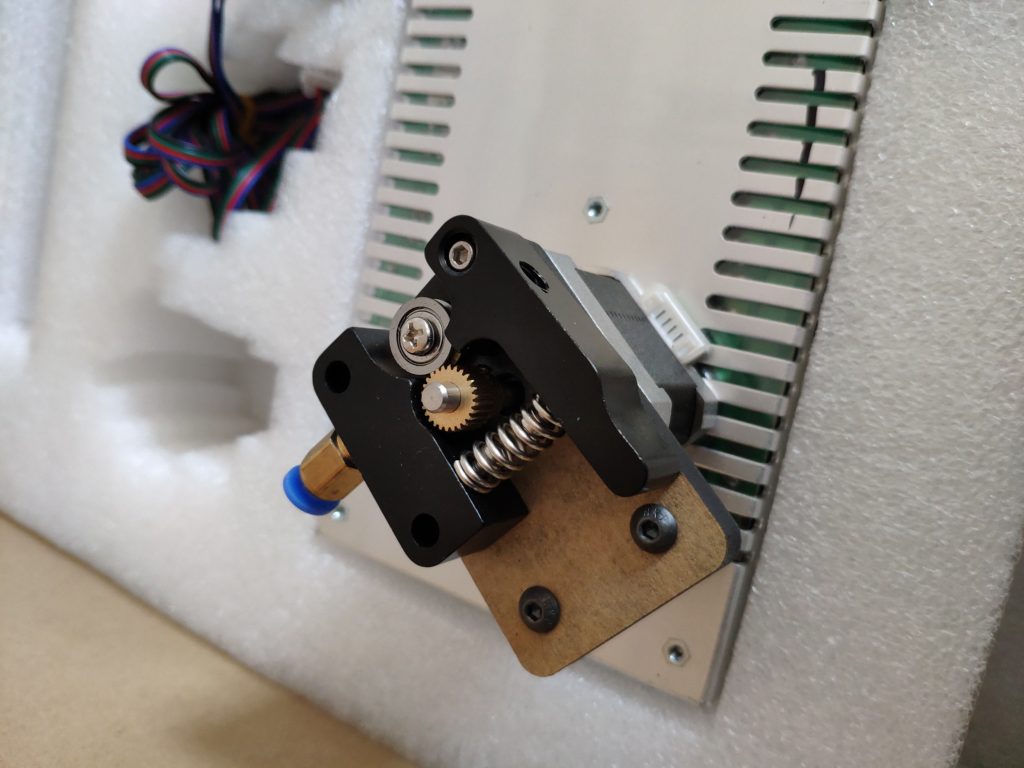
Der Extruderantrieb. Da es sich um ein Bowdensystem handelt ist der Antrieb vom Druckkopf entfernt montiert.
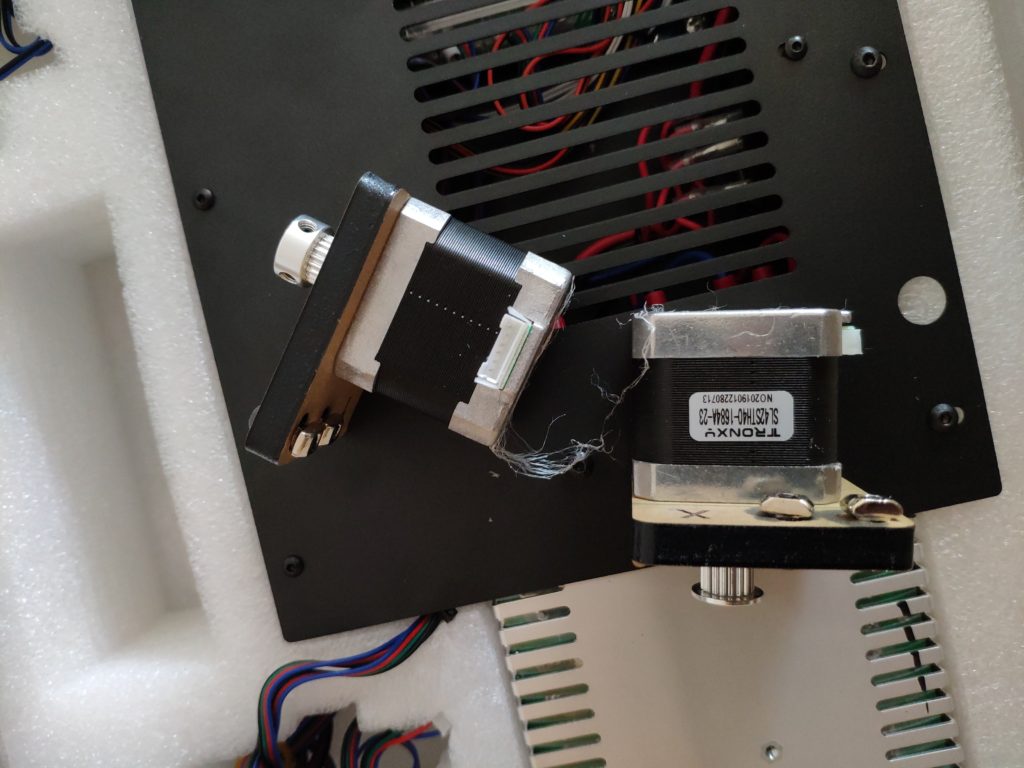
Die beiden Schrittmotoren für die Riemen. Es wird oft bemängelt, dass hier zur Montage Kunststoffplatten verwendet werden. So wie die Platten ausgelegt sind erwarte ich an dieser Stelle aber selbst auf Dauer keine Probleme. Alle Riemenumlenkrollen sind mittlerweile auf Metallplatten montiert. Da hat Tronxy gegenüber den Vorgängermodellen deutlich verbessert.
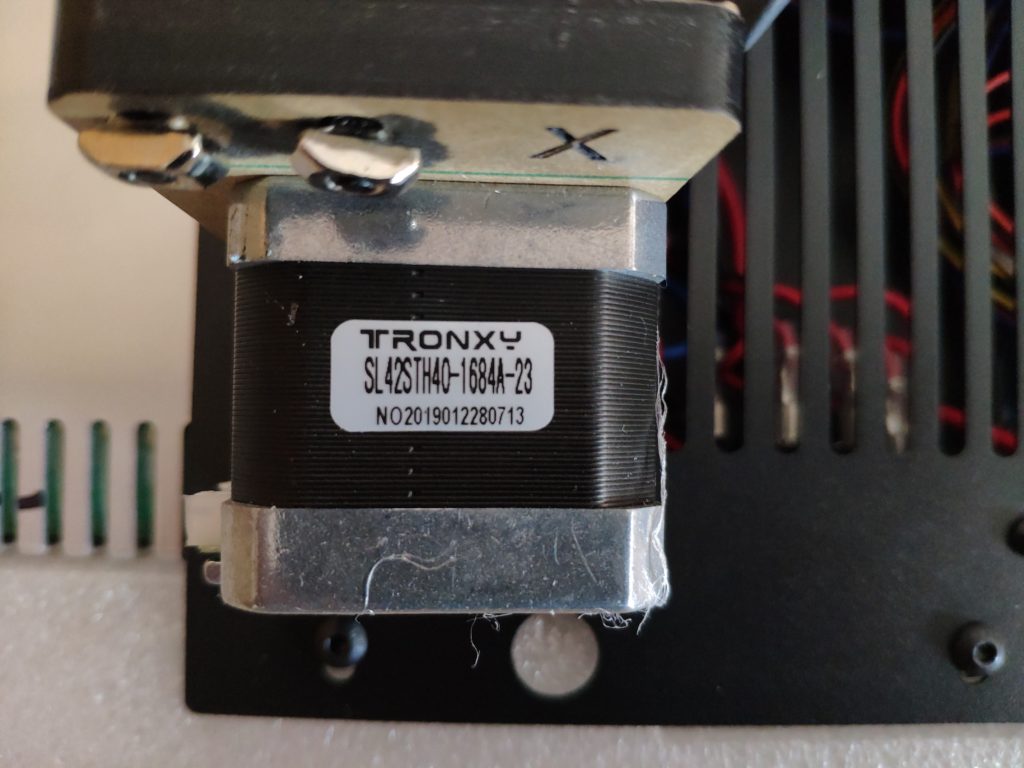
Alle Schrittmotoren sind vom gleichen Typ.
Nun geht es an den Aufbau. Ich habe mal für alle Schritte die Zeit gemessen. Ich habe mich absolut nicht beeilt und gelegentlich auch mal was zu Trinken geholt. Es geht also auch noch deutlich schneller.
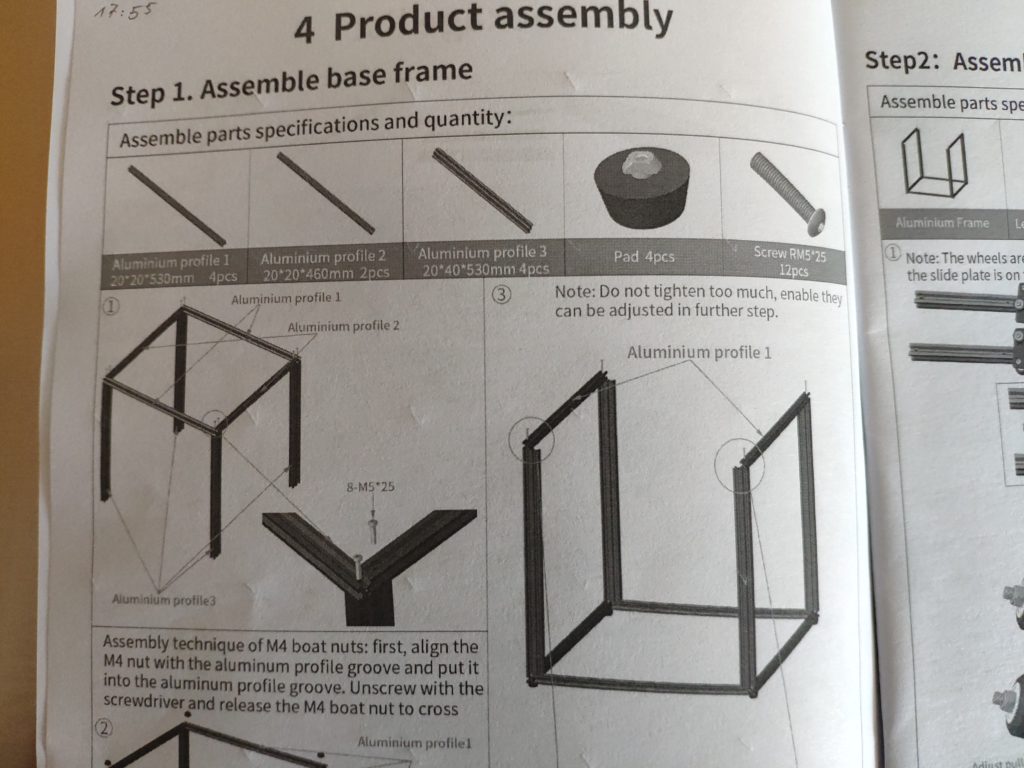
Hier geht es auch schon los. Prinzipiell ist das alles kein Problem. Alle Bohrungen und Gewinde passen hervorragend. Die Aufbauanweisung leidet etwas unter der Reproduktionsmethode. Der wichtigste Teil, – nämlich der Knotenpunkt der drei Rahmenteile, ist auf dem Foto kaum erkennbar. Ein Unbedarfter könnte da ins Rätseln kommen. Aber eigentlich ist es gar nicht falsch aufbaubar.
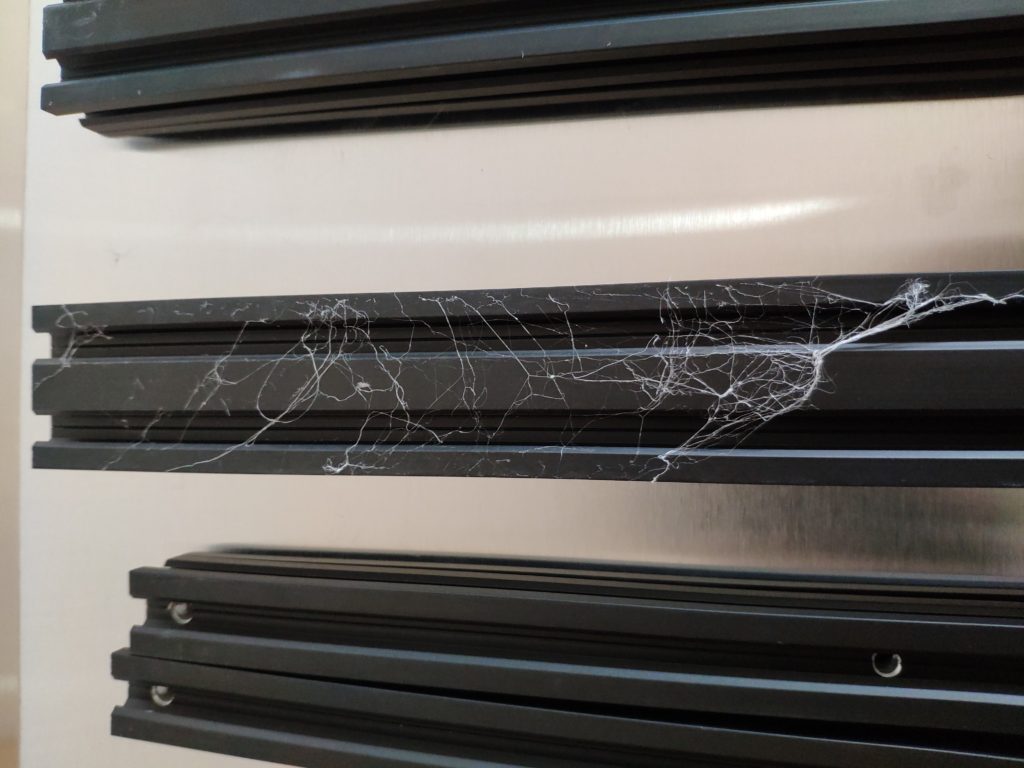
Die Teile waren übrigens sehr stark mit „Engelshaar“ belegt. Das Zeug war auch noch ziemlich klebrig. Es ließ sich aber mit einem leicht feuchten Tuch problemlos abwischen.
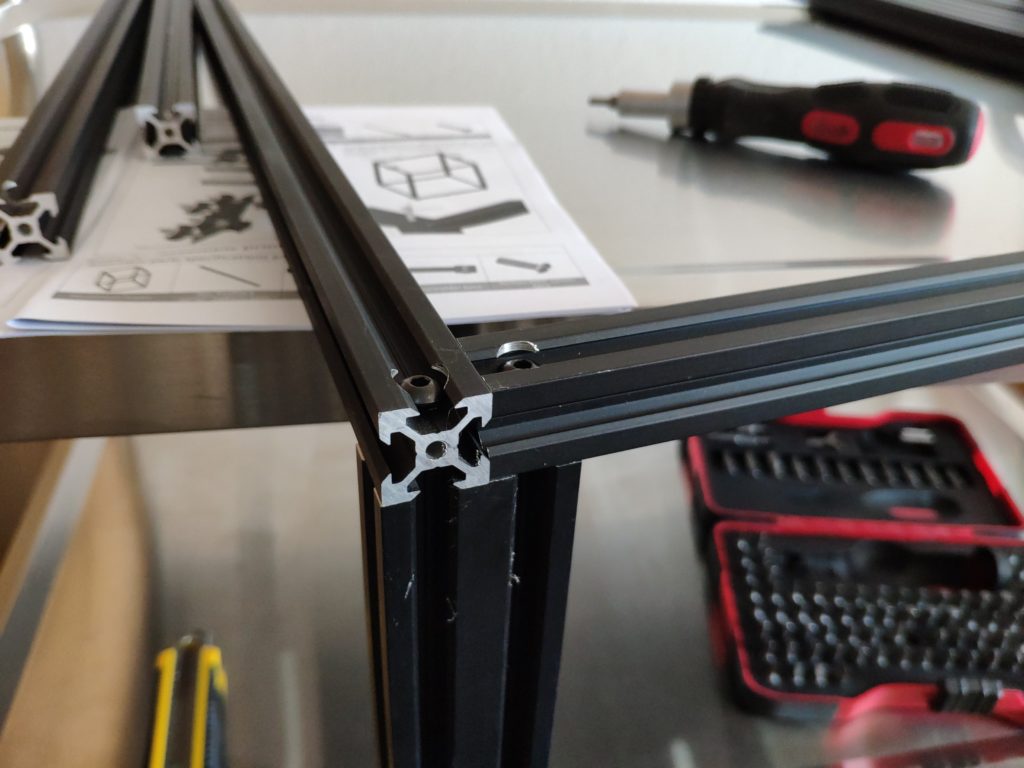
Man sollte beim Aufbau genügend Platz haben und die Oberfläche, auf der gebaut wird, darf nicht empfindlich sein. Kratzer können sehr schnell entstehen. Die Profilkanten sind zwar nicht gefährlich scharfkantig, aber möbelfreundlich abgerundet sind sie natürlich auch nicht.

Es ist für einen Hersteller auch kaum zu schaffen, Profile zu sägen, ohne dass der Kunde ein paar Späne findet. So ist es auch hier. Aufpassen ist angesagt, sobald die Elektronik oder die Lager ins Spiel kommen. Da kann so ein Span schon erhebliche Probleme auslösen. Ich hatte einen kleinen Handstaubsauger neben mir stehen und habe solche Sachen immer sofort weggesaugt.
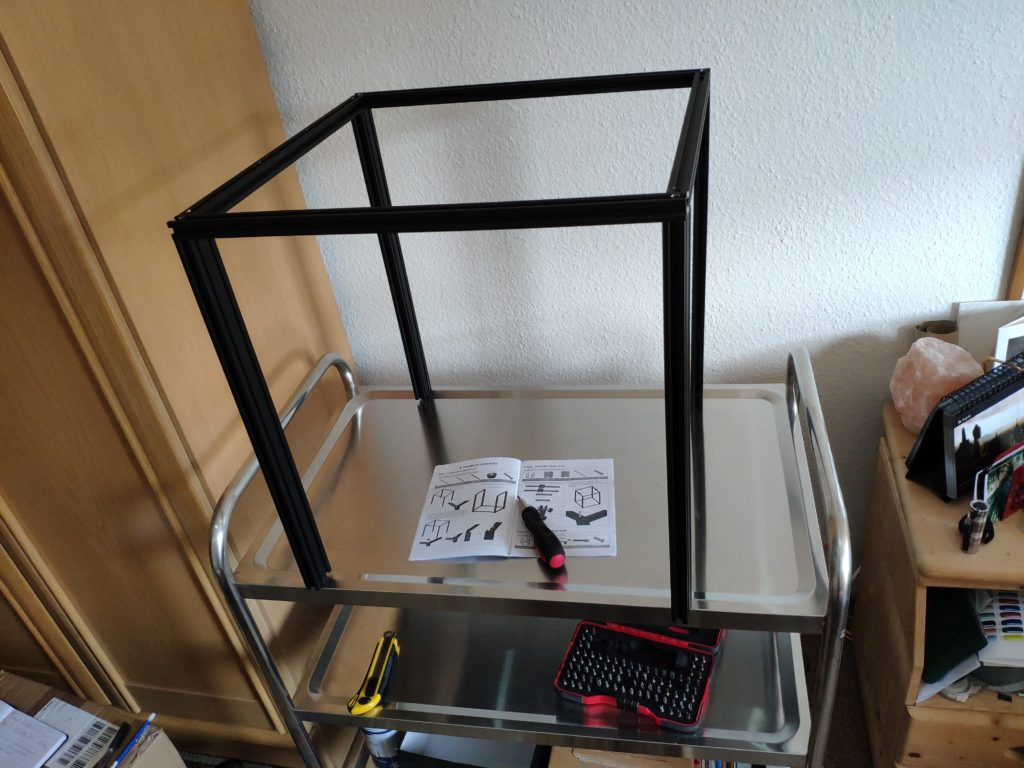
Der Aufbau fand auf dem Großküchenservierwagen statt, auf dem vorher mein Mendelmax stand.
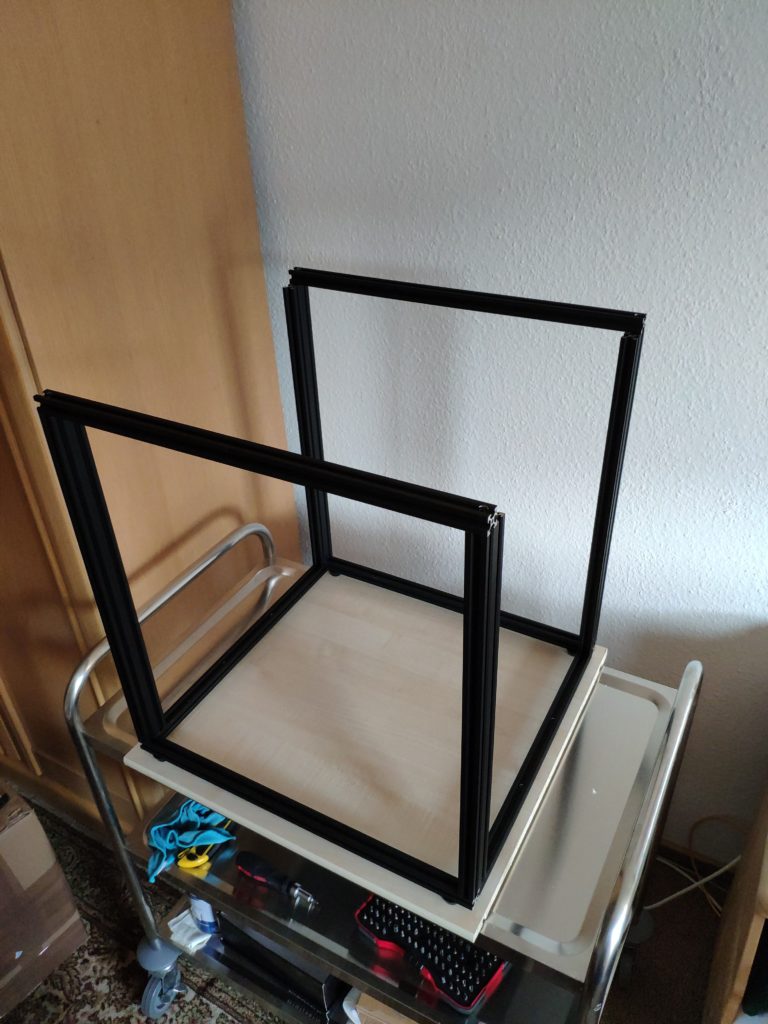
Es ist natürlich sehr wichtig, hier auf die Winkeligkeit zu achten. Ist der Rahmen krumm, kann der Druck nicht gerade werden. Ein großer Anlegewinkel sollte genutzt werden. Ich musste aber kaum etwas korrigieren. Die Schnittflächen scheinen wirklich sehr gut im Winkel zu liegen.
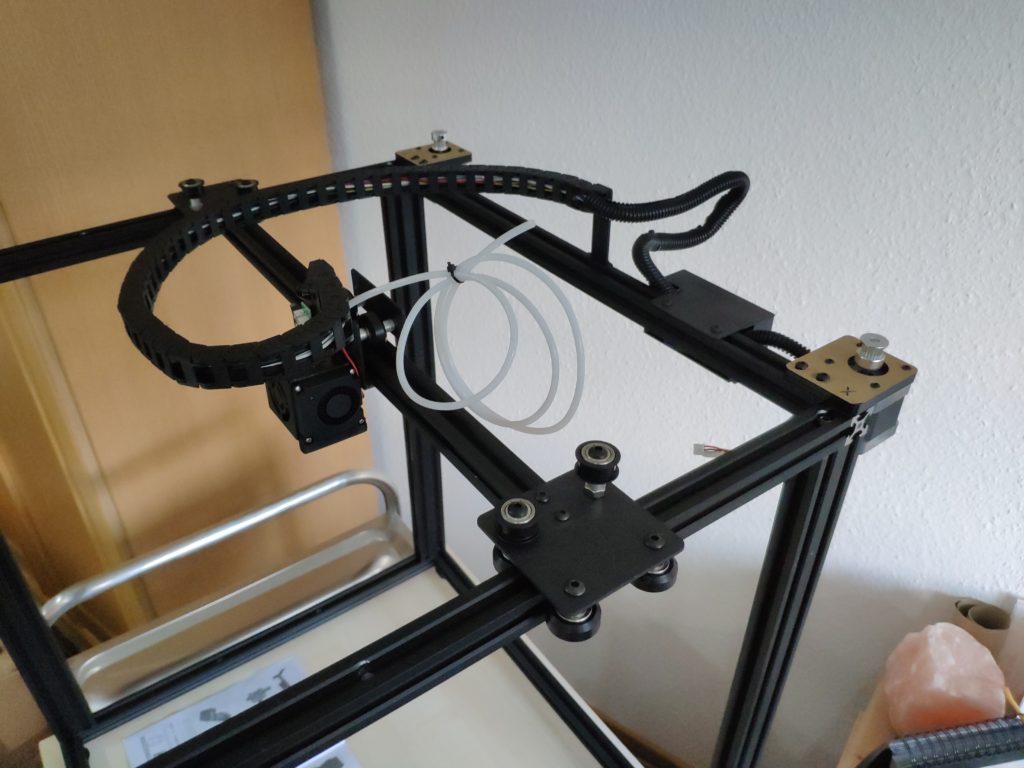
Langsam lässt sich ein 3D-Drucker erkennen.
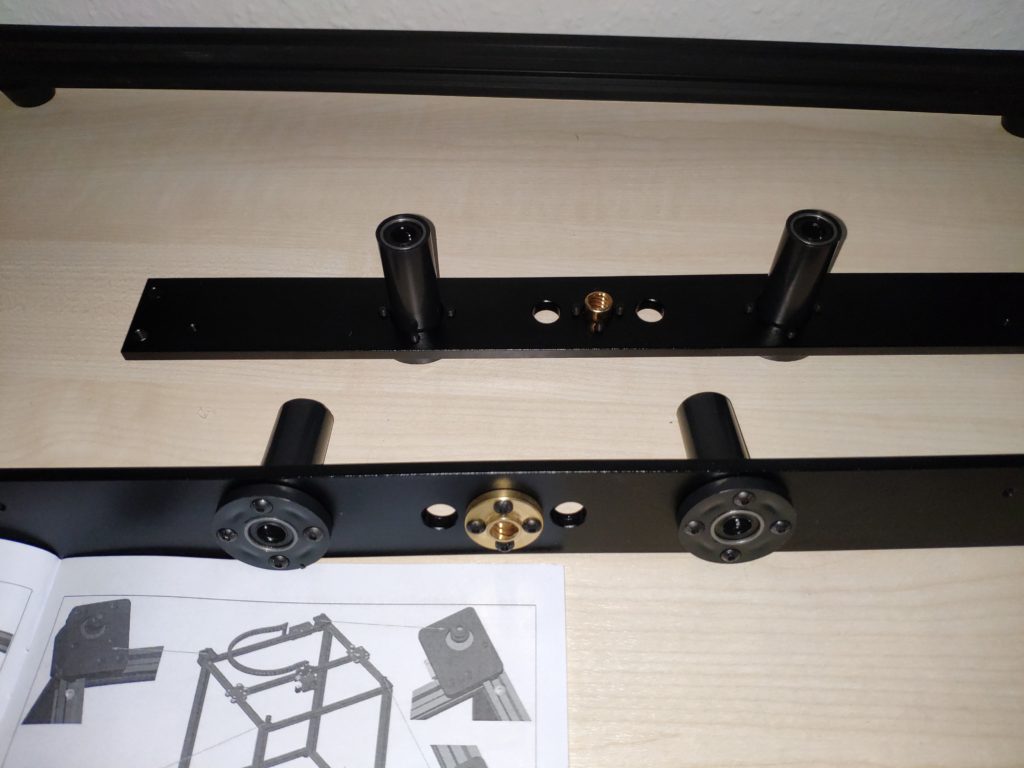
Der Aufbau des Z-Lifts ist etwas „frickelig“. Zuerst müssen die Traversen mit Spindelmutter und Linearlagern aufgebaut werden. Viel Spaß beim Schrauben. Insgesamt warten 24 3mm-Schrauben mit relativ langem Gewinde darauf eingeschraubt zu werden. Kleiner Tipp: Erst alle Schrauben so weit eindrehen, dass die Teile noch beweglich sind. Dann Teile in den Löchern zentriert ausrichten und dann jeweils über Kreuz anziehen. Vorsicht bei den Kunststoffteilen. Wenn der Kunststoff das Fließen anfängt, ist es schon zu viel. Bei roher Gewalt reißt das Material natürlich.
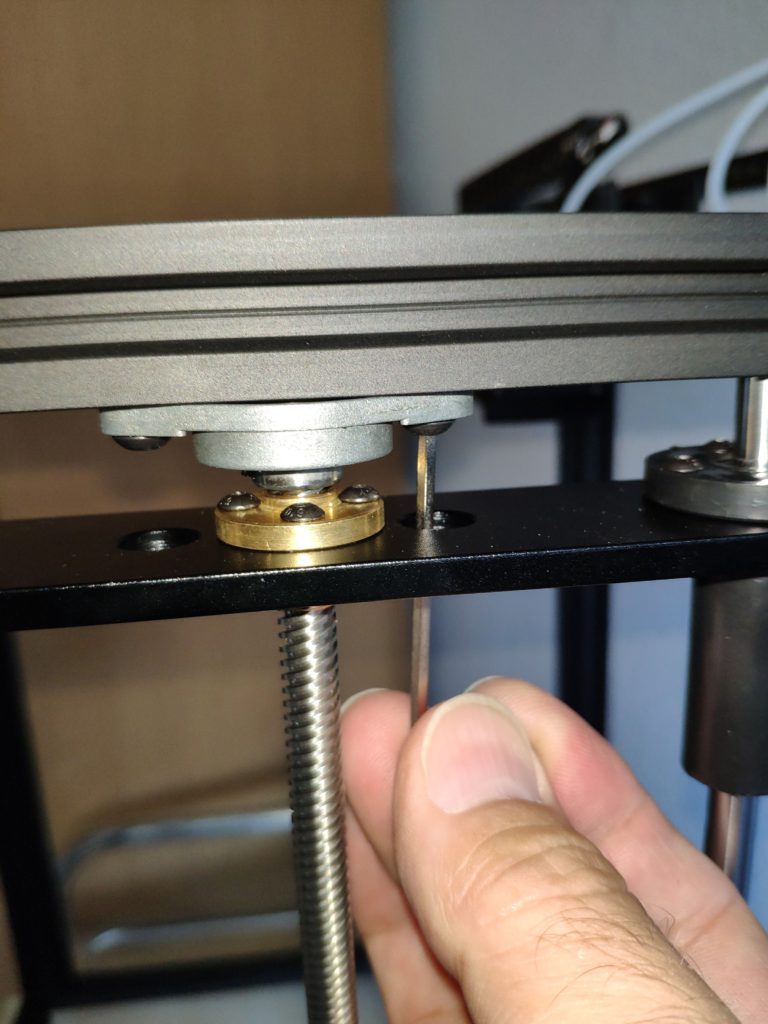
Es empfiehlt sich, wie auch abgebildet in der Anleitung, die Stangen mit der Lifttraverse und dem oberen Lager (nur aufgeschoben) komplett in den Rahmen zu hängen, nachdem das Schrittmotormodul locker fixiert wurde. Da die blanken Stangen und die Gewindestange ohne Abstandsfixierung zueinander eingesetzt werden, muss man natürlich die Abstände abstimmen. Die Madenschrauben werden im Aufbau oben im Lager noch nicht angezogen. Unten wird zunächst der Flansch mit den Madenschrauben am Motor fixiert. Die Motorachse dazu nur so weit einführen, wie der dünne Teil des Lagers lang ist. Jetzt wird die Gewindestange im Flansch so fixiert, dass sie zur oberen Strebe etwa 3-4 mm Abstand hat. Die blanken Stangen und auch das obere Lager sind noch nicht fest angezogen. Die Traverse wird ganz nach oben geschraubt. Jetzt stimmt der Abstand der Stangen zueinander oben. Mit dem oberen Lager (nur die Position, nicht die Madenschrauben für die Gewindestange) beginnend wird jetzt fixiert. Dann werden die beiden Stangen festgeschraubt. Jetzt das Gleiche unten. Die unteren Schrauben der glatten Stangen habe ich nicht angezogen sondern nur locker eingeschraubt. Ich bin der Meinung, dass sich ansonsten die Konstruktion verspannt.
Im letzten Schritt muss noch die Gewindestange im oberen Lager fixiert werden. Dazu folgendes Vorgehen. Die Gewindestange wird jetzt ganz leicht nach oben gezogen, so dass der Flansch etwas auseinander gezogen wird. Jetzt werden in dieser Position die Madenschrauben angezogen. Das hat den Vorteil, dass die Last nicht auf der Achse des Schrittmotors liegt. Dafür ist sein Lager nämlich nicht ausgelegt. Sowohl Gewindestange als auch der ganze Drucktisch hängen jetzt an den oberen Lagern.
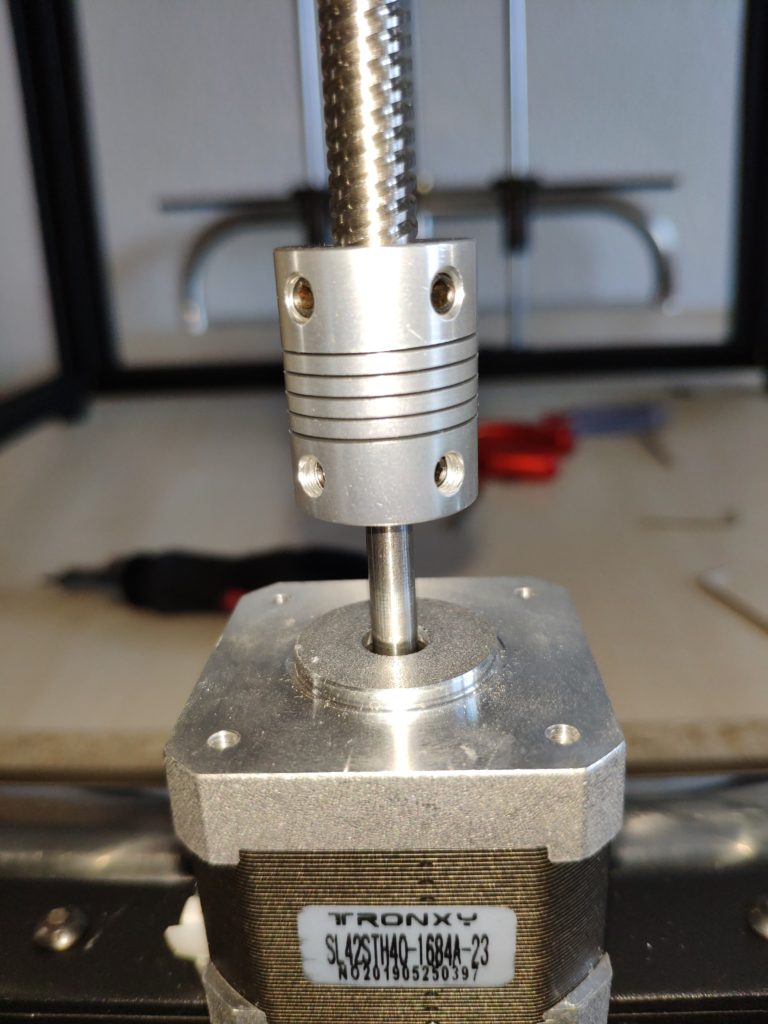
Der weitere Aufbau gestaltet sich eigentlich recht problemlos. An mancher Stelle merkt man aber, dass nicht alles bis zum Ende durchdacht ist.
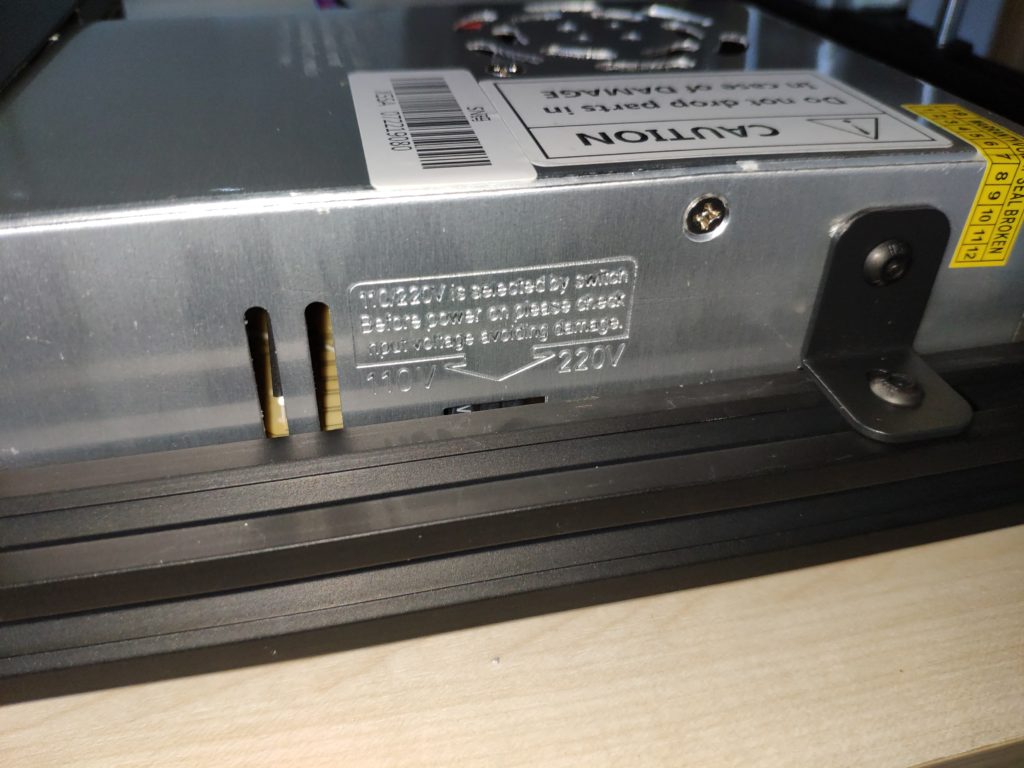
Nach Installation des Netzteils ist es beispielsweise nicht mehr möglich die Primärspannung zu verstellen oder auch nur sicher abzulesen.
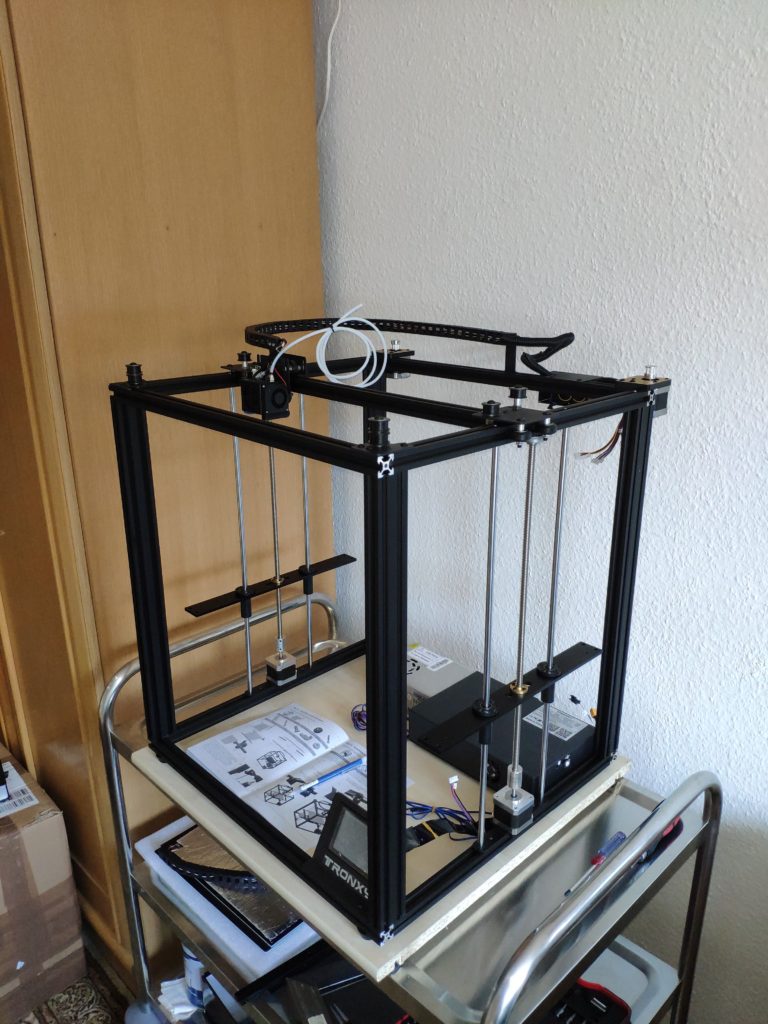
Noch fehlt das Druckbett.
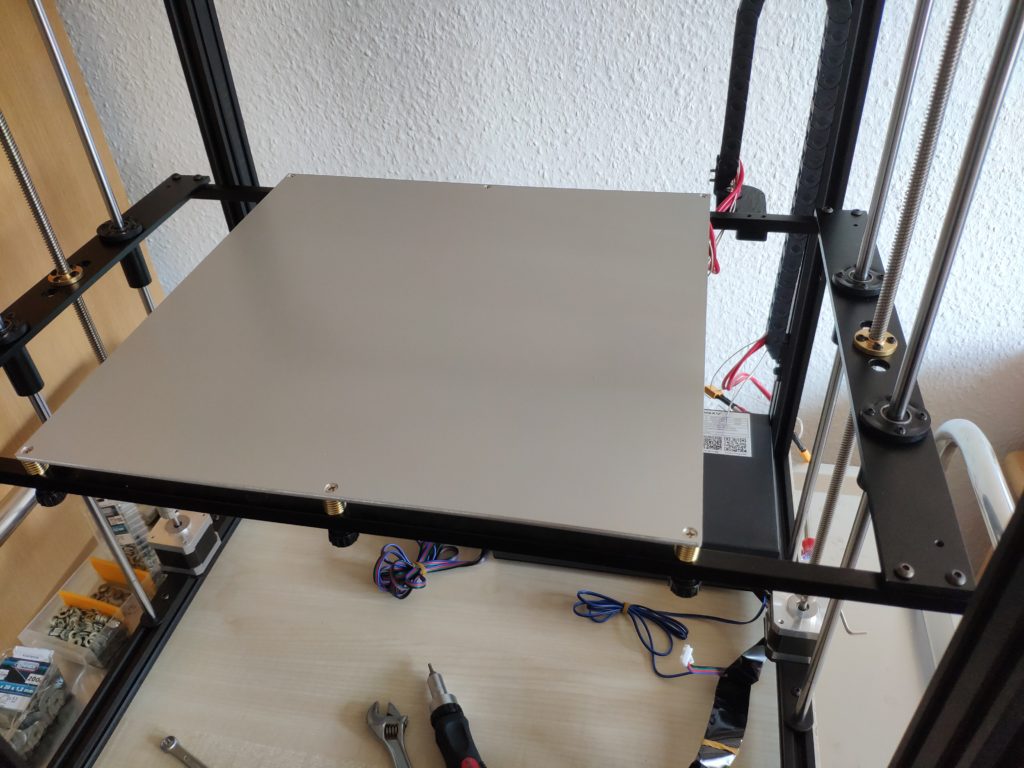
Aber das ist auch sehr einfach im Aufbau. An einer Stelle sollte man aufpassen. Das Druckbett ist mit 6 Schrauben befestigt. Man sollte auf gleichmäßiges Anziehen achten, um nicht gleich die Platte zu verziehen. Wenn man später den Oberflächentest laufen lässt, merkt man deutlich, wie weit man die Platte mit den Schrauben verziehen kann.
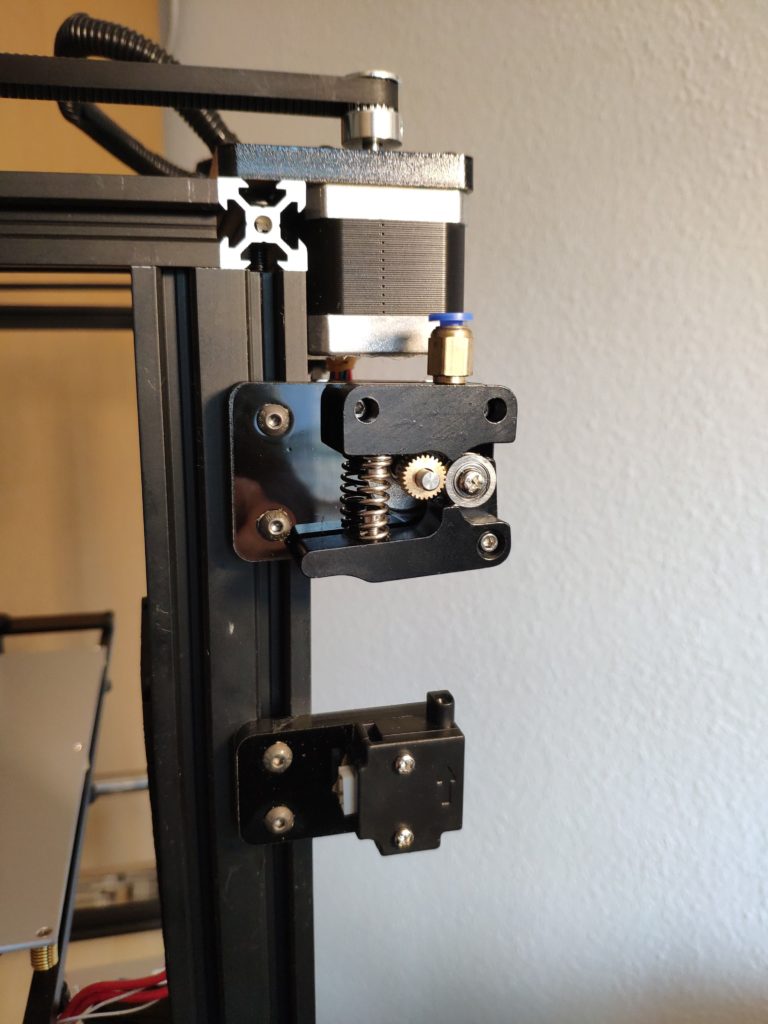
Hier ist noch der Extruderantrieb und der Filamentsensor zu sehen.
Wieviel Zeit habe ich denn nun gebraucht? Der reine Rahmen mit den Schritten 1 und 2 hat eine Stunde in Anspruch genommen. Die Y-Schlitten sind dann schon montiert, aber noch nicht eingestellt. Die Druckkopfmontage hat gute 20 Minuten gedauert. Schritt 4 behandelt die Umlenkrollen und Motoren für die X- und Y-Achse. Hier gingen gerade mal 10 Minuten drauf. Für die gesamte Z-Lift-Montage mit den Schritten 5 und 6 habe ich knapp über eine Stunde gebraucht. Netzteil und Steuerelektronik (Schritt 7) waren in einer Viertelstunde installiert. Die Druckbettmontage dauerte 45 Minuten und das Anbringen der Riemen für die X/Y-Steuerung war nach 15 Minuten erledigt. Der gesamte Rest mit den Schritten 10 bis 13 war in einer guten Stunde fertig. Dazu kommt jetzt noch das ordentliche Befestigen der Leitungen. Hier sollte eine Stunde reichen. Übrigens reichen die mitgelieferten Kabelbinder nicht aus, weil sie nicht lang genug sind um ein 2040-Profil zu umschließen.
Insgesamt sind also etwa 6 Stunden anzusetzen, bis der Drucker ohne Justierarbeiten steht. Das deckt sich mit den Erfahrungen anderer Nutzer aus dem Netz.