Bei all der Technik aus den vergangenen Beiträgen ist es mal wieder an der Zeit etwas Künstlerisches zu machen. Auf einer Messe in München sah ich neulich schöne Lampen, die einen interessanten Schatten geworfen haben. Die Lampenschirme bestanden aus Holzplatten, aus denen Segmente ausgeschnitten waren. Das kann ich auch …
Die Segmente waren meines Erachtens auch bei den ausgestellten Lampen ausgelasert. Die Kanten waren dunkel, wobei der typische Geruch aber fehlte. Da sich der Brandgeruch aber eh nach einiger Zeit verflüchtigt, ist das kein Indiz für eine andere Technik.
Man findet im Internet schnell entsprechende Entwürfe für interessante Designs. Eine gute Anlaufstelle ist immer wieder auch Thingiverse. Mir gefiel dort die Dodecahedron Lamp.

Ich habe mir also die Dateien heruntergeladen und die .dxf-files in Inkscape bearbeitet. Es gibt einige Probleme zu beachten, die sich fast alle auf das Thema Maßstab bzw. Größe zurückführen lassen.
Die Entwürfe waren alle für deutlich größere Sperrholzplatten und vor allem für einen größeren Lasercutter gedacht. Die Dimensionen der Platten waren 450mm * 600mm. Mein Laser schafft aber gerade mal DIN A4-Größe. Dementsprechend musste ich in Inkscape die Zeichnung verkleinern. Eigentlich ja kein Problem. Da aber kleine, ebenfalls gelaserte, Klammern die 12 fünfeckigen Seitenteile zusammenhalten muss die Holzdicke berücksichtigt werden. Die Klammern müssen so dimensioniert sein, dass ihr „Maul“ das Seitenteil umfassen kann. Die Aussparungen für die Klammern in den Seitenteilen müssen ebenfalls auf meine 3mm-Plattendicke angepasst werden. Würde man jetzt einfach die Vorlagen verkleinern, passt das alles nicht mehr. Also ist Feinarbeit angesagt.
Von den 12 Seitenteilen sind 11 vollkommen identisch. In eine Laservorlage kommt also ein Seitenteil und die dazu benötigten Klammern. 5 Seiten hat jedes Seitenteil und je Seite sind 5 Klammern zu setzen. Macht zusammen 25 Klammern. Die Hälfte pro Laservorlage reicht auch, da die Klammern ja immer auch das Nachbarteil umklammern. Bearbeitet man jetzt eine einzige Klammer in ihrer Größe um der 3mm-Dicke gerecht zu werden, kann man anschließend 12 Kopien davon anlegen um alle Klammern zu haben. Das Bearbeiten geht hier über schlichtes Vergrößern um den richtigen Maßstab.
Die Aussparungen in den Seitenteilen sind schon komplizierter. Hier muss direkt an die Knoten herangegangen werden. Ein bisschen Know-How bezüglich Inkscape ist da notwendig. Ich musste mich auch erst „schlaulesen“. Nach 20 Minuten ging es aber leicht von der Hand. Beim Bearbeiten daran denken: Auskerbungen immer symmetrisch erweitern, damit auch später die Gegenseite passt!
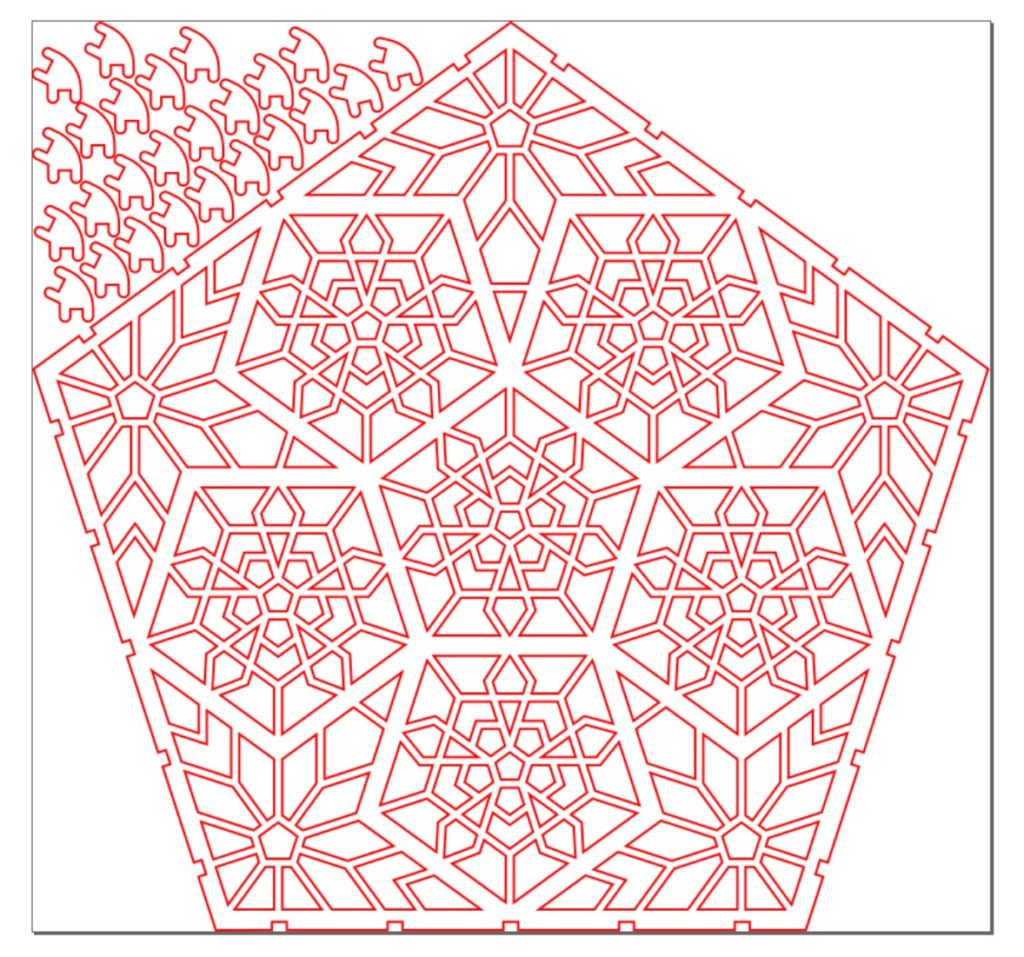
Das Ergebnis sieht dann etwa so aus. Übrigens habe ich dann noch den Fehler gemacht, dass ich zu knapp bemessen habe. So habe ich dann an der einen oder anderen Stelle nochmal mit der Feile nachgearbeitet. Mit dem Messwerkzeug in Inkscape sollte der Abstand in den Einkerbungen ermittelt werden. Die Strichdicke wird mit 0,5mm in der Farbe Rot 255 eingestellt. Gemessen werden sollte auf der Außenseite der Linien, – nicht in der Mitte. Mit anderen Worten soll in der Kerbe von der einen Liniengrenze zur gegenüberliegenden gemessen werden. Und das sollte mindestens der Holzdicke entsprechen.
Aus Inkscape wird dann eine svg-Datei erzeugt. Wie das genau geht, habe ich an anderer Stelle im Blog beschrieben. Mit dem K40-Laser habe ich anschließend die Platten ausgelasert.
Anhaltswerte: Pappelsperrholz, 30%-35% Laserleistung bei 6 mm/s, Birkensperrholz, 55% Laserleistung bei 6 mm/s.
Die elf so entstandenen Seitenteile konnte ich dann zusammenleimen. Es fehlte das Bodenteil. Das führte dann auch noch zu einer Denksportaufgabe: Der Boden musste leicht zu lösen sein, denn schließlich muss man das Leuchtmittel wechseln können. Ein Lampenfuß muss auch noch her.
Für den Lampenfuß bin ich in einen Möbelmitnahmemarkt gegangen. Die haben in der Regel in der Elektroabteilung immer irgendwelche Restbestände von Tischlampen. So habe ich recht schnell einen schönen Lampenfuß gefunden. Klar, der hässliche Lampenschirm war auch dabei. Aber den kann man ja entsorgen.
Für das Bodenteil des Lampenschirms habe ich eine neue Konstruktion gewählt. In dem Vorschlag aus Thingiverse war so etwas nicht vorhanden.
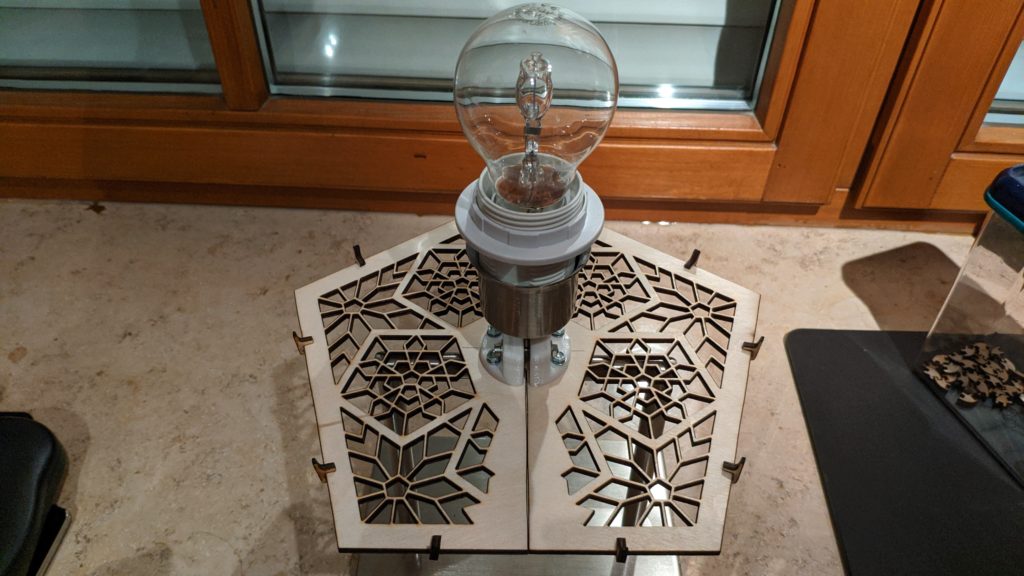
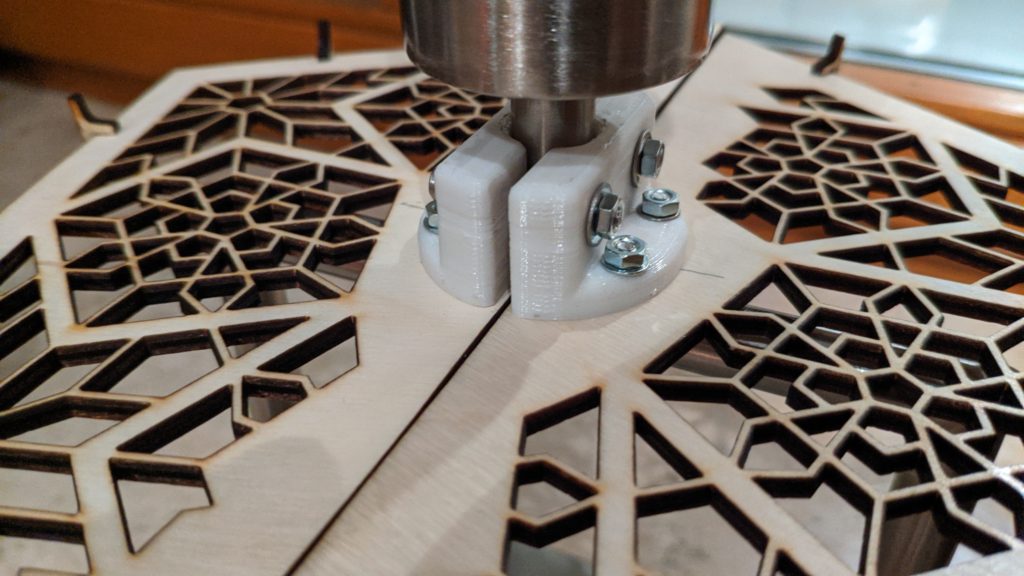
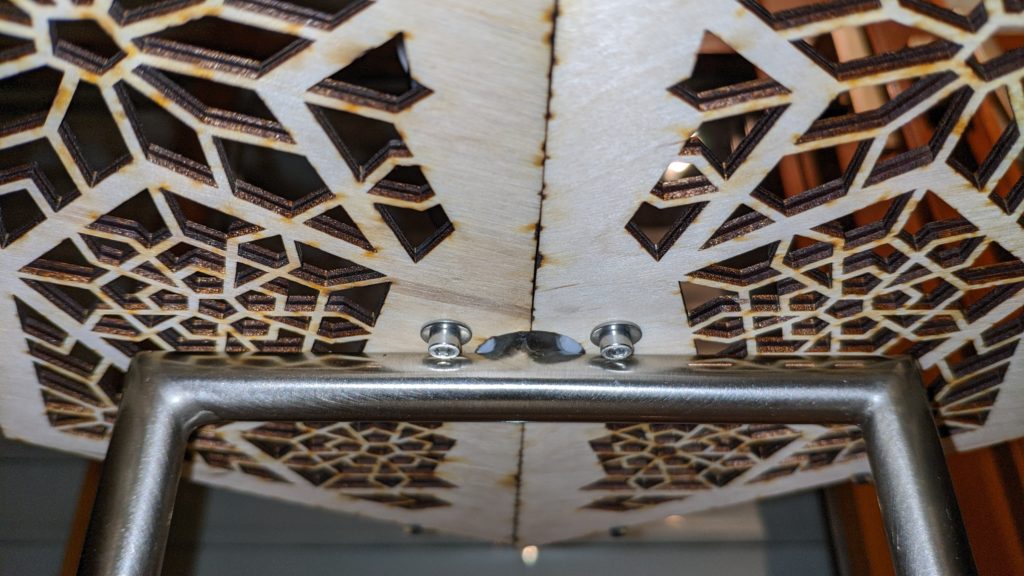
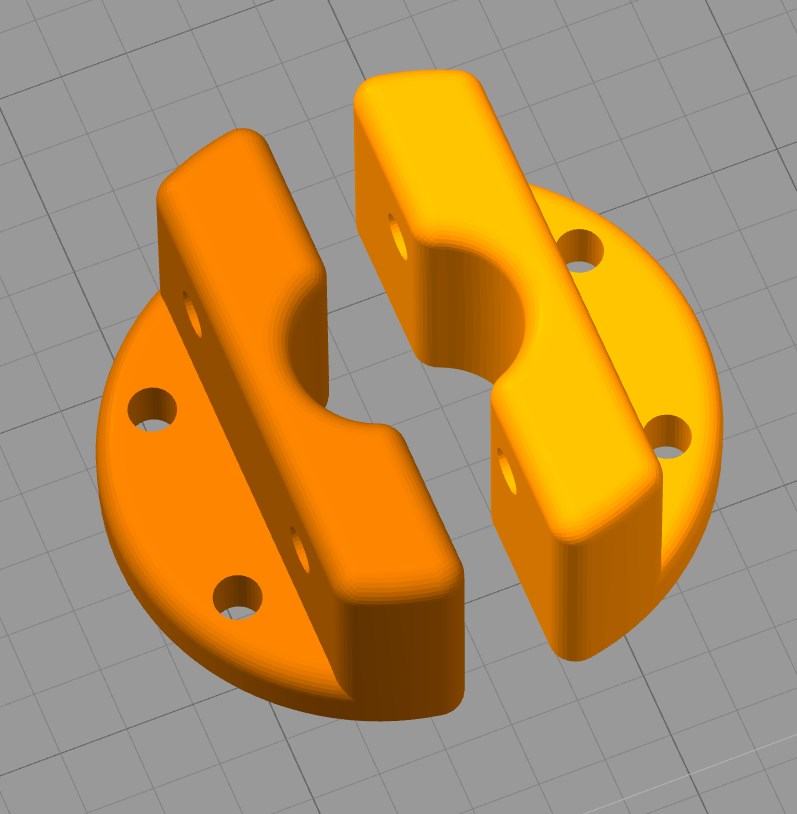
Die Halterung habe ich in Fusion360 entworfen und dann mit dem 3D-Drucker aus weißem PET-G gedruckt.
Um einer sich aufdrängenden Frage gleich vorwegzukommen: Natürlich wäre es naheliegend, die am Lampenfuß direkt unter der Fassung vorhandene Aufnahme zu nutzen. Bringt aber aus zwei Gründen nichts. Erstens muss das Leuchtmittel bei dieser Art von Lampen immer punktförmig aus der Mitte strahlen, was auch bei der Auswahl der Leuchtmittel wichtig ist. Der Schattenwurf funktioniert sonst nicht! Nutzt man die vorhandene Verschraubung liegt die Lampe zu weit unten im Schirm.
Zweitens ist das Leuchtmittel nicht wechselbar, da es üblicherweise dicker als die E27-Fassung ist.
Das Bodenteil bedurfte auch noch einer entsprechenden Zeichnung in Inkscape. Die notwendigen Schritte waren:
- breiten Mittelsteg einziehen, damit man ….
- den Boden in der Mitte teilen kann.
- Mittelaussparung einbringen.
- Das Bodenteil muss deutlich größer werden, damit man den Schirm darauf ablegen kann
- Andere Klammern müssen entworfen werden. Sie sollen nur ein seitliches Wegrutschen des Schirms verhindern.
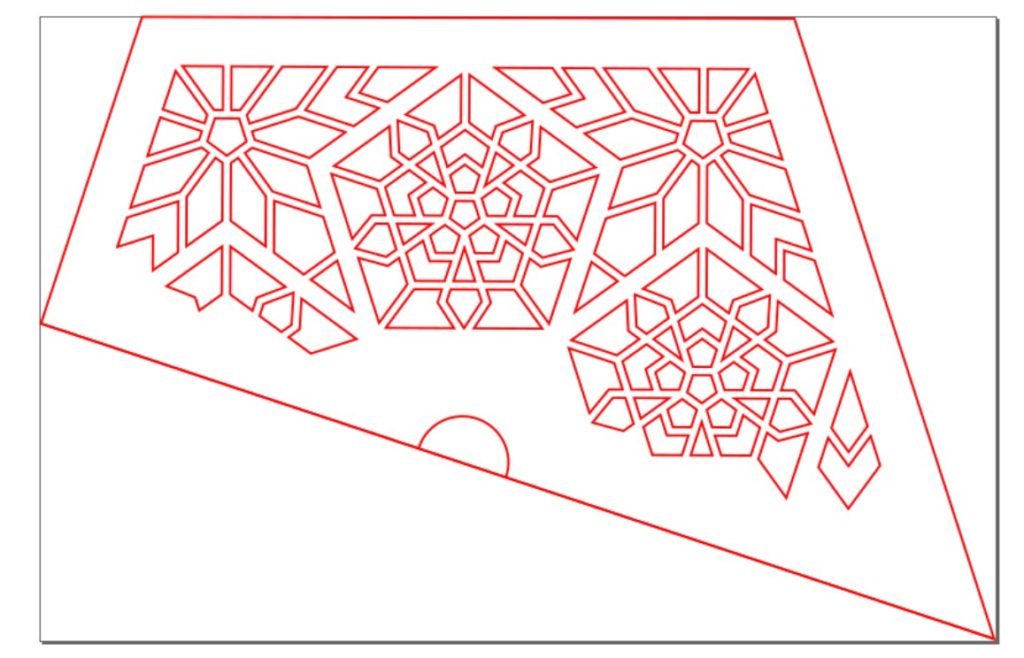
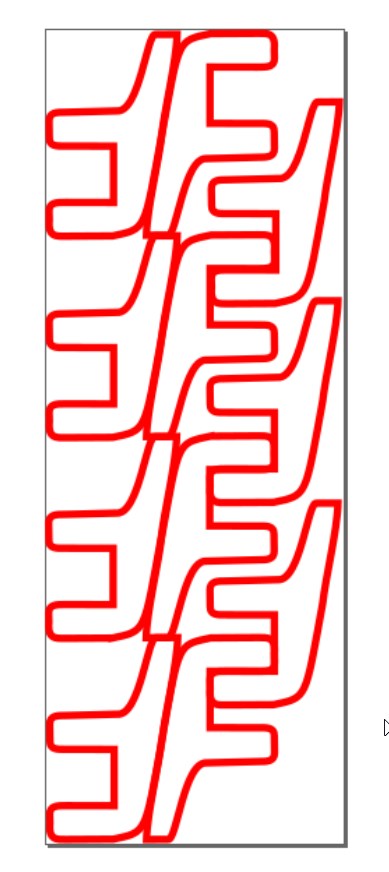
Im Ergebnis sieht die Lampe dann so aus, wie in den abschließenden Bildern. Noch ein paar Hinweise:
- Das Leuchtmittel muss punktförmig sein und möglichst im Mittelpunkt stehen, sonst ist der Schattenwurf unscharf
- Elektrische Arbeiten gehören in die Hand derer, die das gelernt haben. Unterschätzen Sie niemals die Gefahr von Strom! Ich rate deshalb dringend vom Nachbau ab, wenn Sie nicht über die notwendige Expertise verfügen.
- Das Leuchtmittel sollte nicht zu stark aufheizen, sonst brennt der Schirm ab. LED-Licht wäre geeignet.
- Lampe nur beaufsichtigt eingeschaltet lassen.
- Entweder man schafft es, dass der Laser keine Schmauchspuren auf dem Holz hinterlässt, oder man achtet beim Zusammenkleben darauf, dass die schönen Seiten außen liegen.
- Beim Verleimen sollte Holzleim genommen werden. Andere Kleber könnten aufgrund ihrer Zusammensetzung unerwünscht auf Wärmeeinwirkung reagieren.
- Man wird es kaum schaffen, dass alle Klammern komplett sauber in den Kerben sitzen. Beim Versuch ist mir eine Seite durchgebrochen. Man sieht es eh nicht!
- Auf Anfrage stelle ich gern alle Skizzen und Konstruktionen zur Verfügung. Aufgrund der unterschiedlichen Anforderungen können sie aber immer nur als Grundlage dienen.
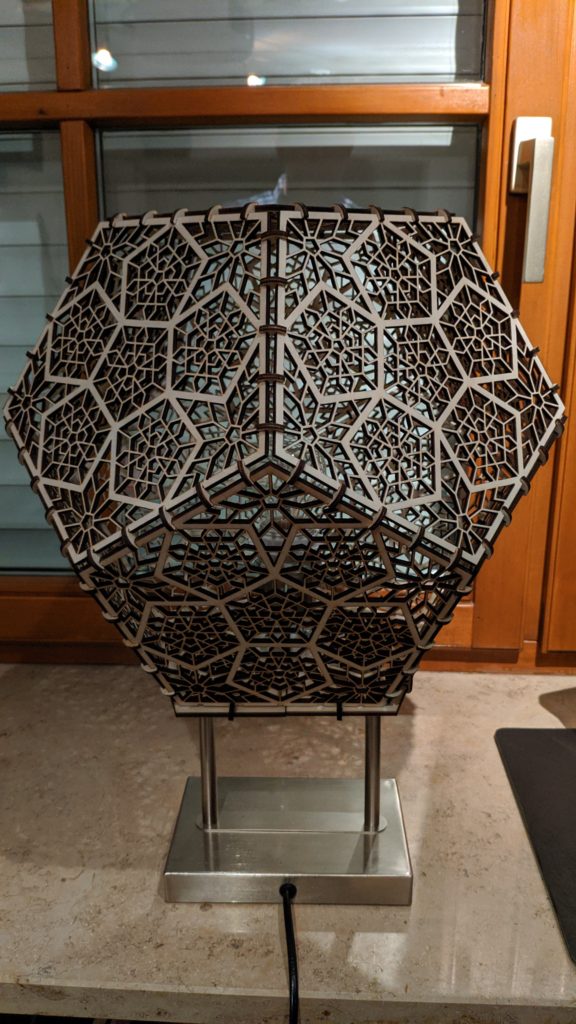
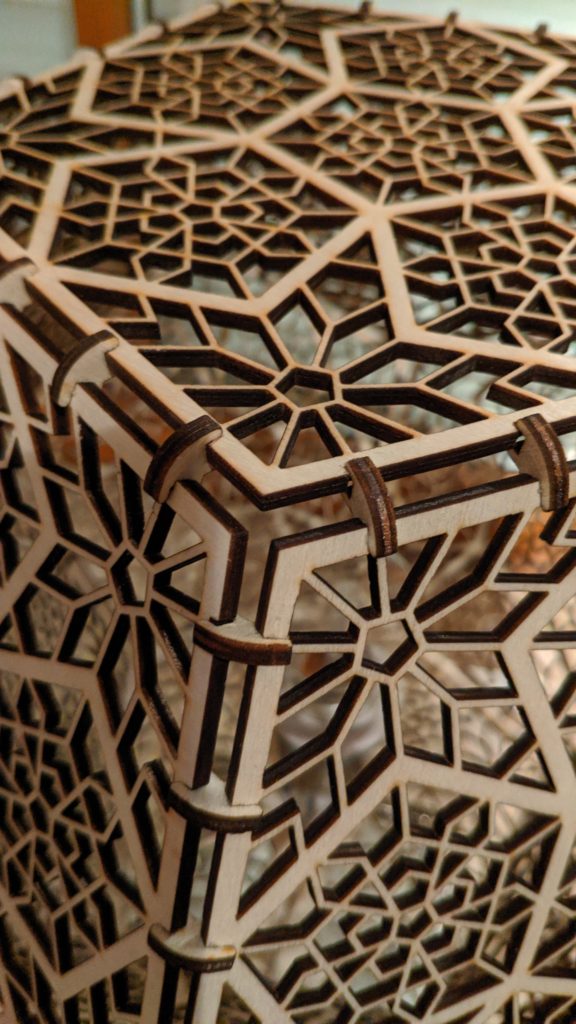
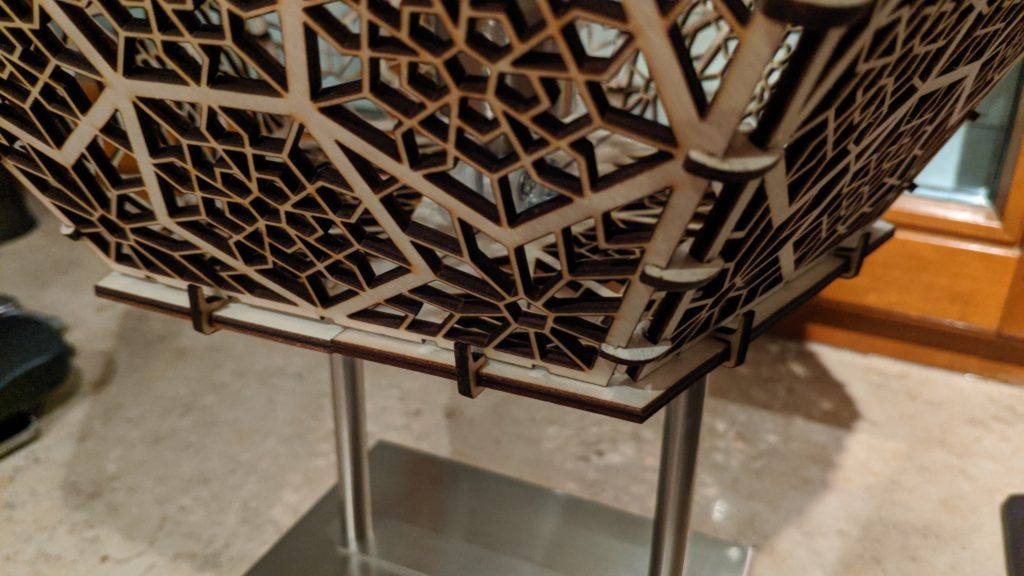