Anfangs hatte ich die Filamentspule offen an eine Halterung am Drucker montiert. Der Nachteil dieser Methode liegt auf der Hand. Die Spule, oder besser gesagt das Filament, ist der Luft vollkommen ausgesetzt. Sowohl Staub als auch Luftfeuchtigkeit setzen dem Filament zu. Da ich auch nicht immer sofort die Spule nach dem Druck wieder einpacke, besteht das Problem für einige Stunden. Abhilfe musste her.
Vorab ein Wort zu den hier zum Download angebotenen ZIP-Archiven: Die Archive enthalten nur Dateien vom Typ f3d und stl. Ist etwas anderes drin, ist es nicht von mir. Vorsicht: Auch mein Server kann mal gehackt sein.
Zunächst mal habe ich eine entsprechende Kunststoffbox gesucht. Für meine 1kg-Spulen mit 20cm Durchmesser und 7cm Dicke war das gar nicht so einfach. Aber schließlich wurde ich fündig:
Als Amazon-Partner verdiene ich an qualifizierten Verkäufen. Für den Käufer ändert sich der Preis dadurch nicht. |
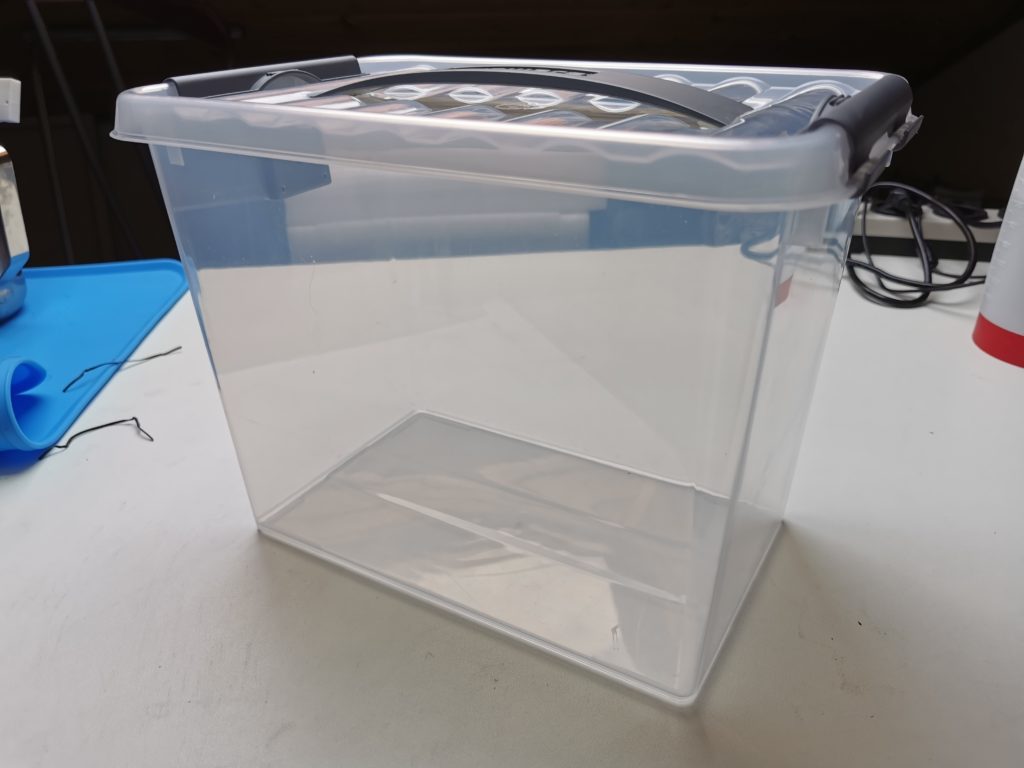
Die Box allein hilft nicht. Die Spule muss in der Box gelagert werden. Ich wollte unbedingt Beschädigungen der Box vermeiden. Außerdem sollte der Spulenwechsel leicht und schnell zu erledigen sein. Es gibt unzählige gute Ideen für Spulenhalterungen beispielsweise auf thingiverse. So richtig zufrieden war ich allerdings mit keiner. Also habe ich selbst gebastelt. Wie Ihr es von mir kennt, entsteht so etwas in der Regel erstmal aus Aluminiumprofilen. Ich würde das jetzt als Prototyp bezeichnen.
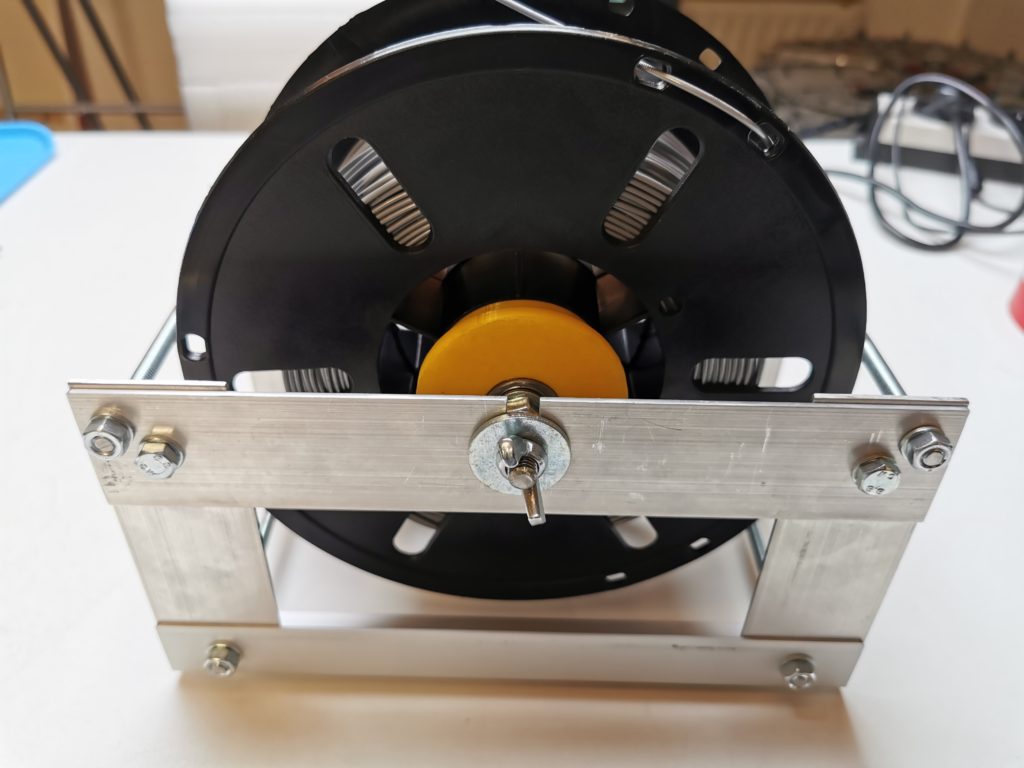
Die gelbe Achse hatte ich schon vor einiger Zeit konstruiert und gedruckt. Sie war schon im Einsatz.
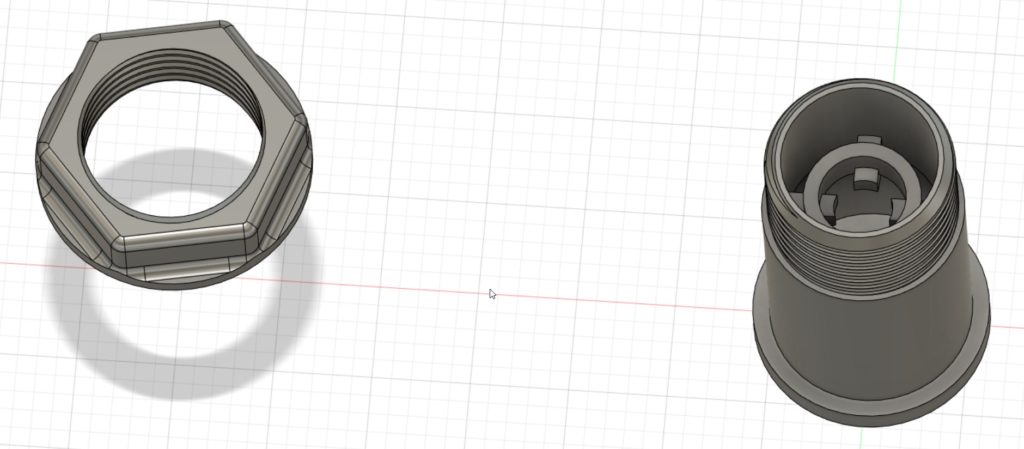
Die Spulenachse (Datei Spulenhalter) musste nochmal in der Konstruktion nachgearbeitet werden. Dazu später mehr. Das große Gewinde war zu eng konstruiert. Ich hatte erhebliche Nacharbeiten am Druck.
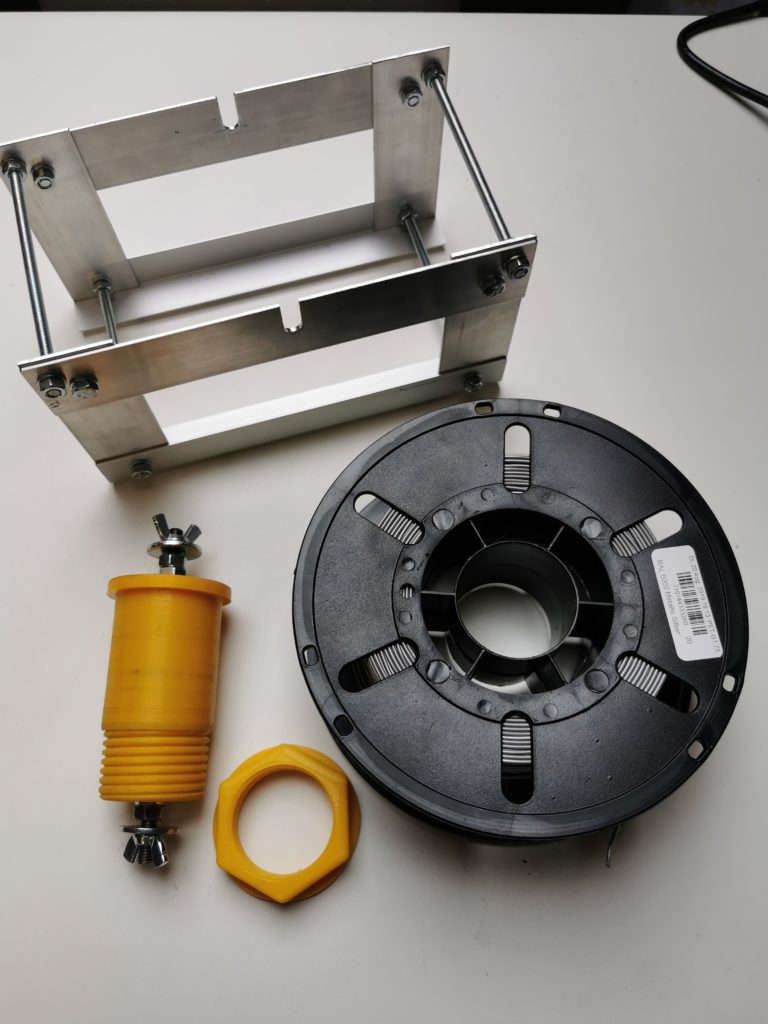
Falls sich jemand für den genauen Aufbau interessiert, kann er sich gerne bei mir melden.
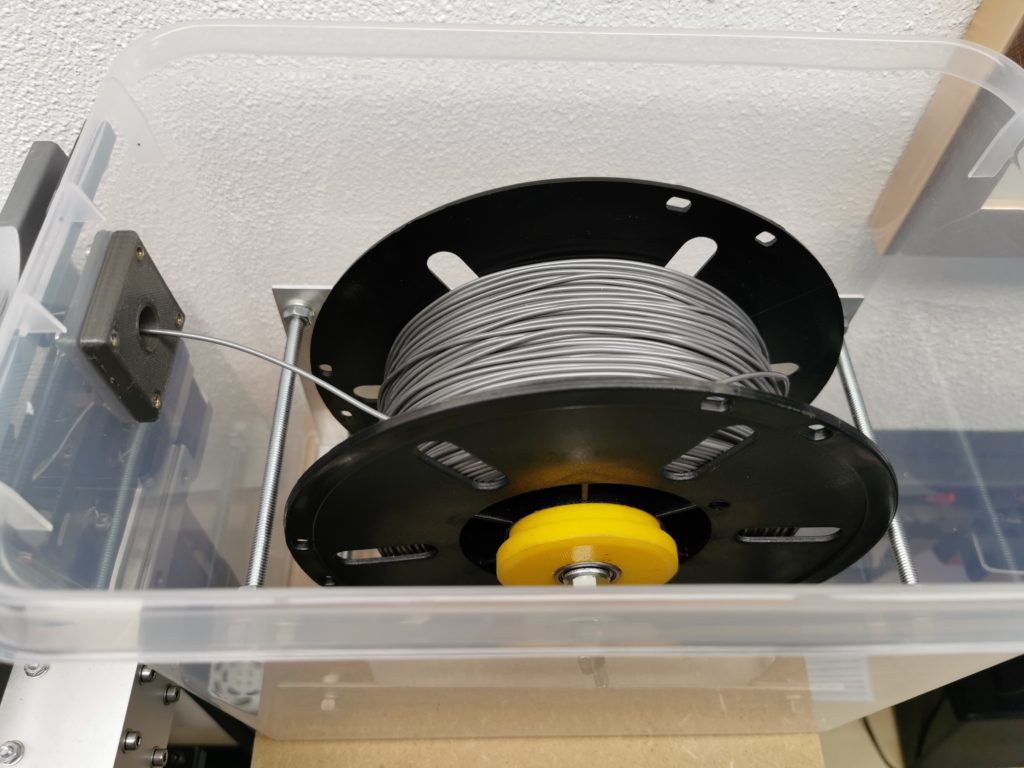
Ganz ohne Löcher in der Kunststoffbox ging es dann doch nicht. Das Filament muss ja herausgeführt werden. Dafür habe ich wieder einen Adapter konstruiert. Hauptbestandteil ist natürlich der Pneumatikverschluss mit dem Aluminiumdrehteil, die beide von einem Extruder übrig waren. Die innen liegende Platte wird noch mit Ruthex Einpressgewinden 3mm versehen und ist deshalb mit entsprechenden Löchern konstruiert.
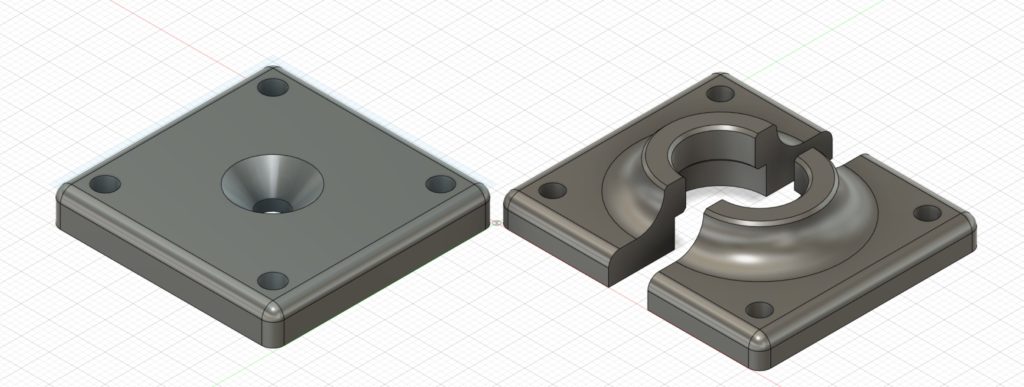
Hier die Fusion360-Archivdatei und die STLs:
Angebaut sieht es dann so aus …
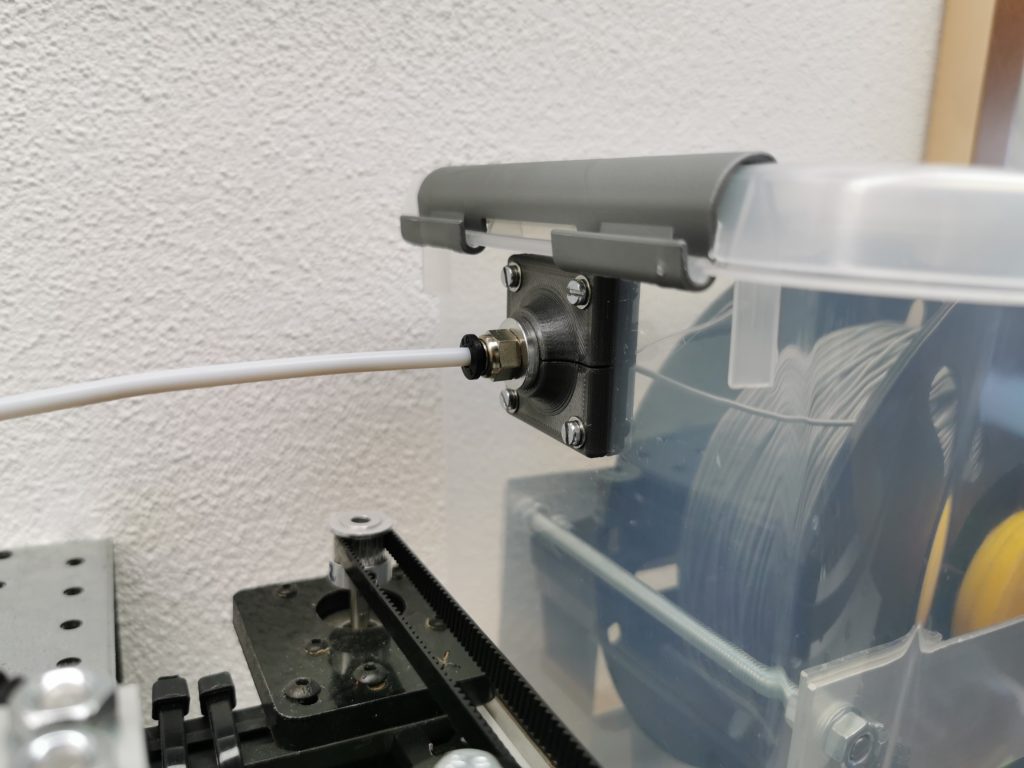
Die Kiste ist natürlich nicht vollständig luftdicht. Der Aufwand dies zu realisieren wäre zu groß. Gegen Staub und Feuchtigkeit ist das aber schon mal ein gewaltiger Schritt nach vorn.
Die ganze Kiste habe ich dann auf einem kleinen Wandhalter neben dem Drucker platziert.
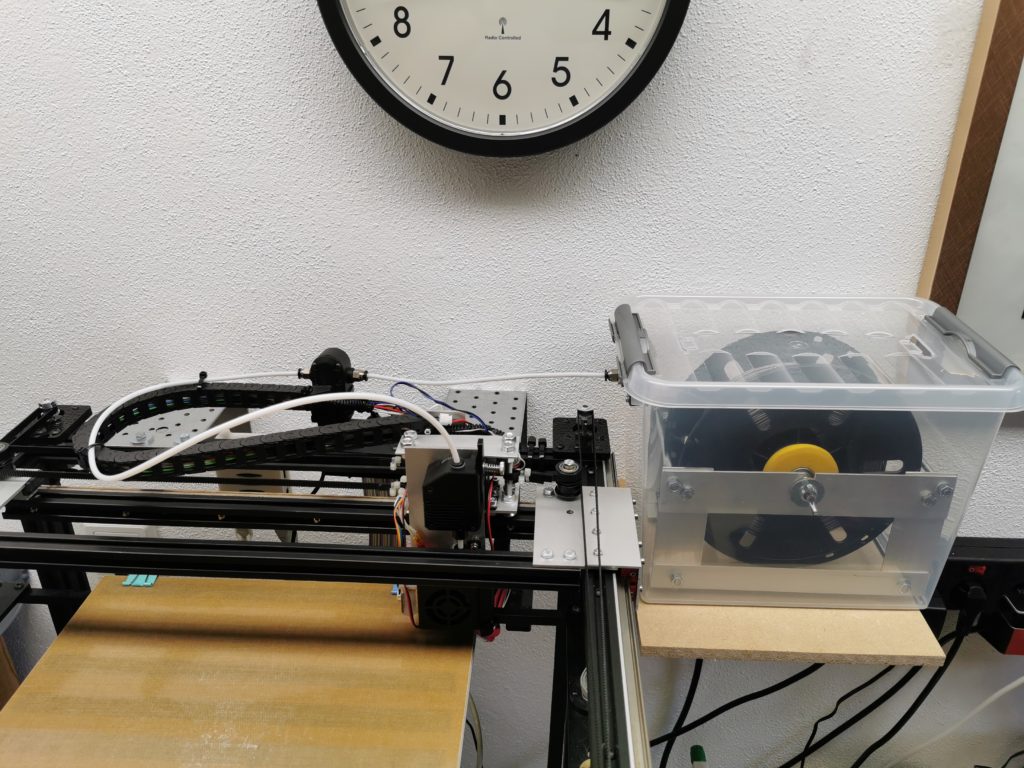
So funktionierte das auch problemlos. Aber ich habe dann doch noch ein Redesign durchgeführt.
Ich hatte oben schon erwähnt, dass das gedruckte Gewinde des Spulenkerns viel zu eng war. Damals wusste ich einfach noch nicht, wie man druckbare Gewinde konstruiert. Ein Tipp in aller Kürze: Je eine Gewindeflanke an beiden Teilen wird einfach um ein Zehntel abgetragen, denn es sind die engen Gewindeflanken, die die Probleme verursachen, – nicht etwa der Durchmesser. Mittlerweile druckt mein Tronxy auch noch wesentlich präziser. Es hatte sich außerdem herausgestellt, dass am großen Teil des Spulenkerns ein Sechkantgriff ganz gut wäre und das Gewinde um 10mm länger sein sollte.
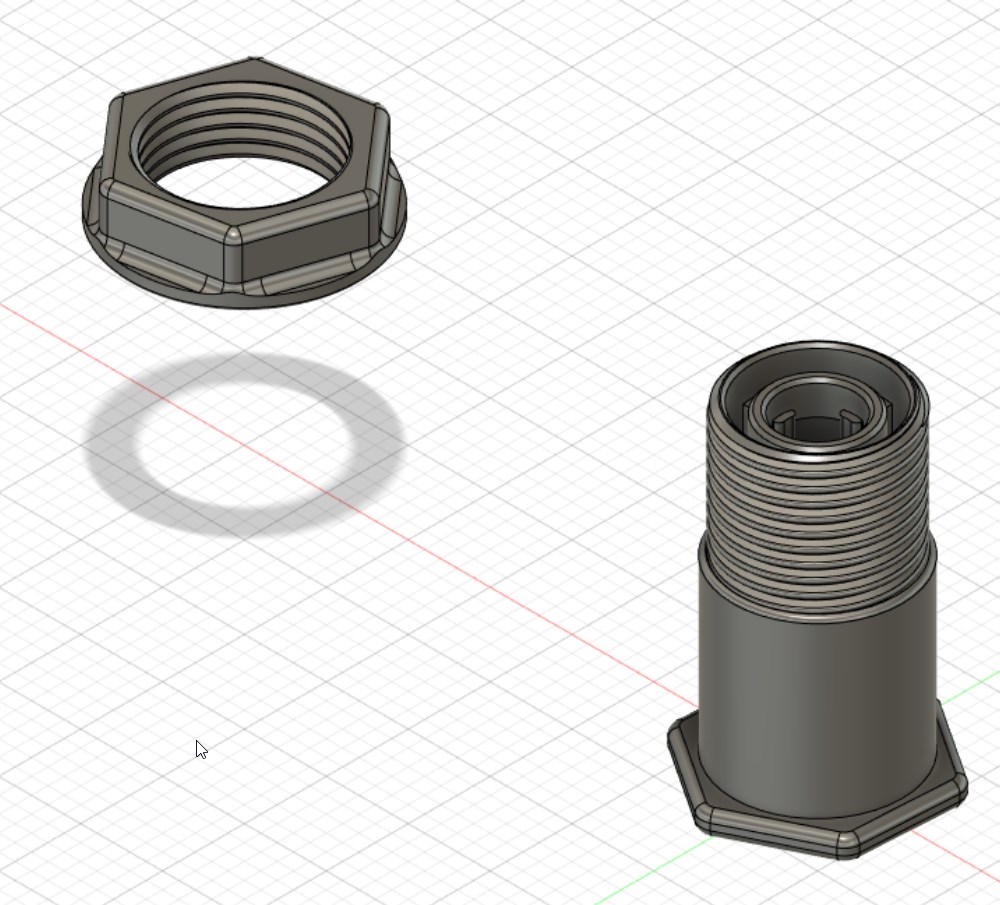
Anbei die Fusion360-Archivdatei und die STLs des zweiteiligen Spulenkerns.
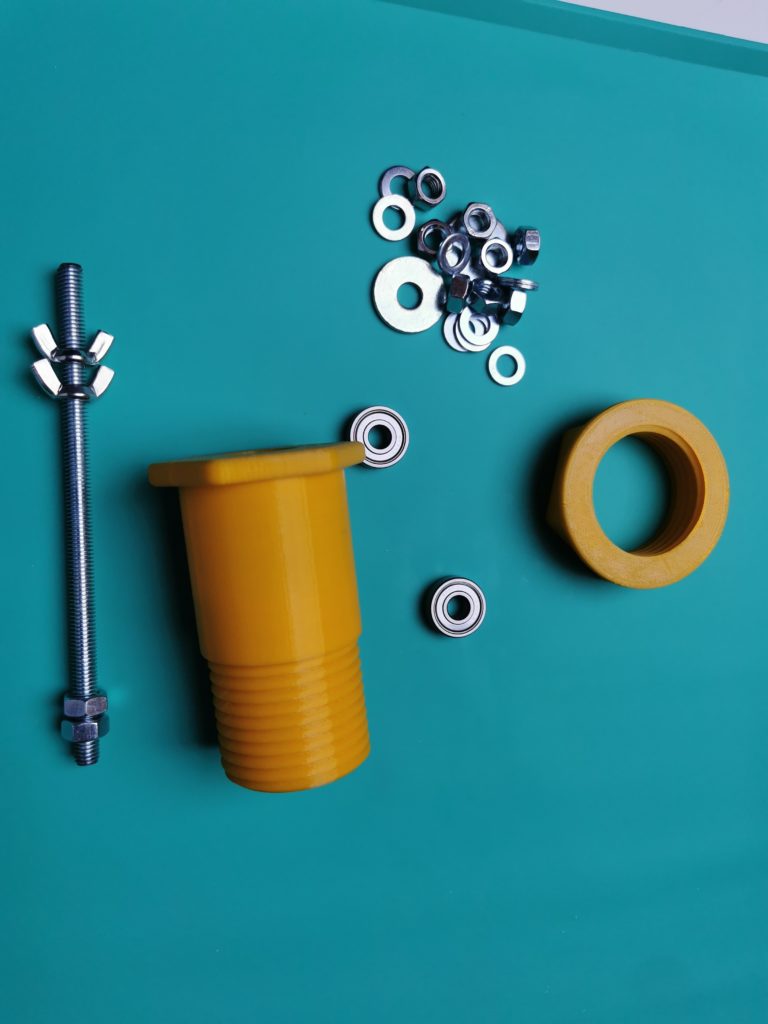
Für den Zusammenbau benötigt man:
- eine 160mm lange M8 Gewindestange
- zwei 608zz-Wälzlager
- zwei Flügelschrauben M8
- vier Muttern M8
- 3 kleine Unterlegscheiben
- 2 große Unterlegscheiben
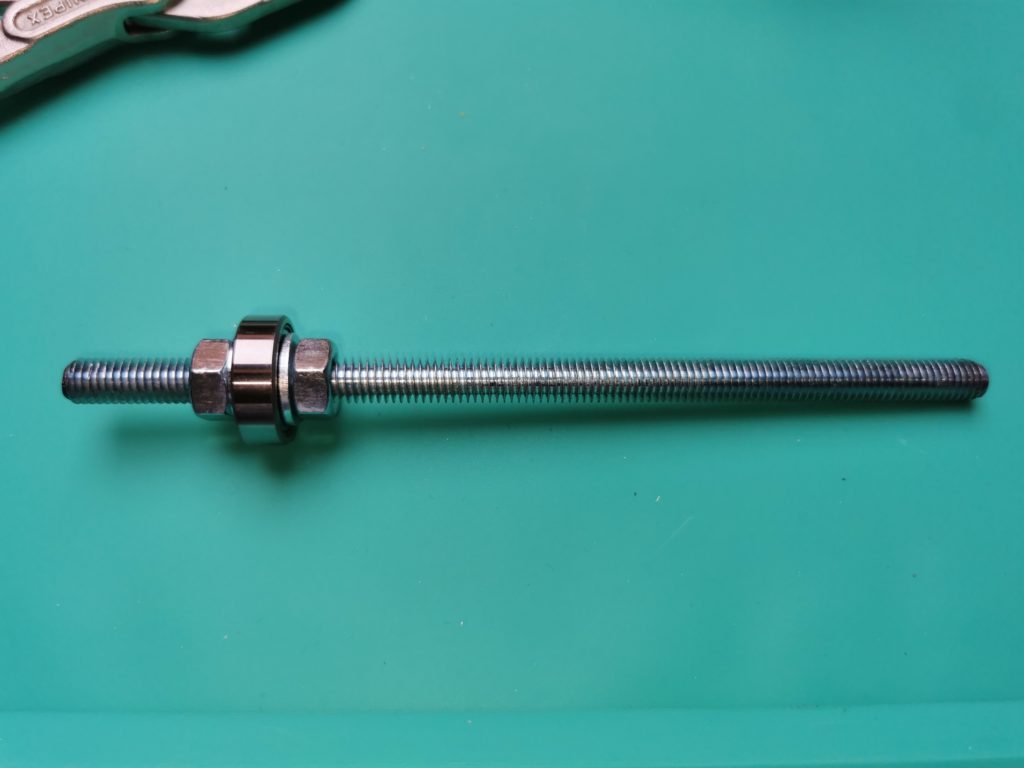
Es geht mit der obigen Konstruktion los, die gut fixiert wird. Wichtig ist, dass die Unterlegscheiben die Funktion des Wälzlagers in keiner Weise behindern dürfen. Prinzipiell dürften die Unterlegscheiben also nicht größer als der innere Ring des Lagers sein. Das freie Gewinde links hat eine Länge von 20mm.
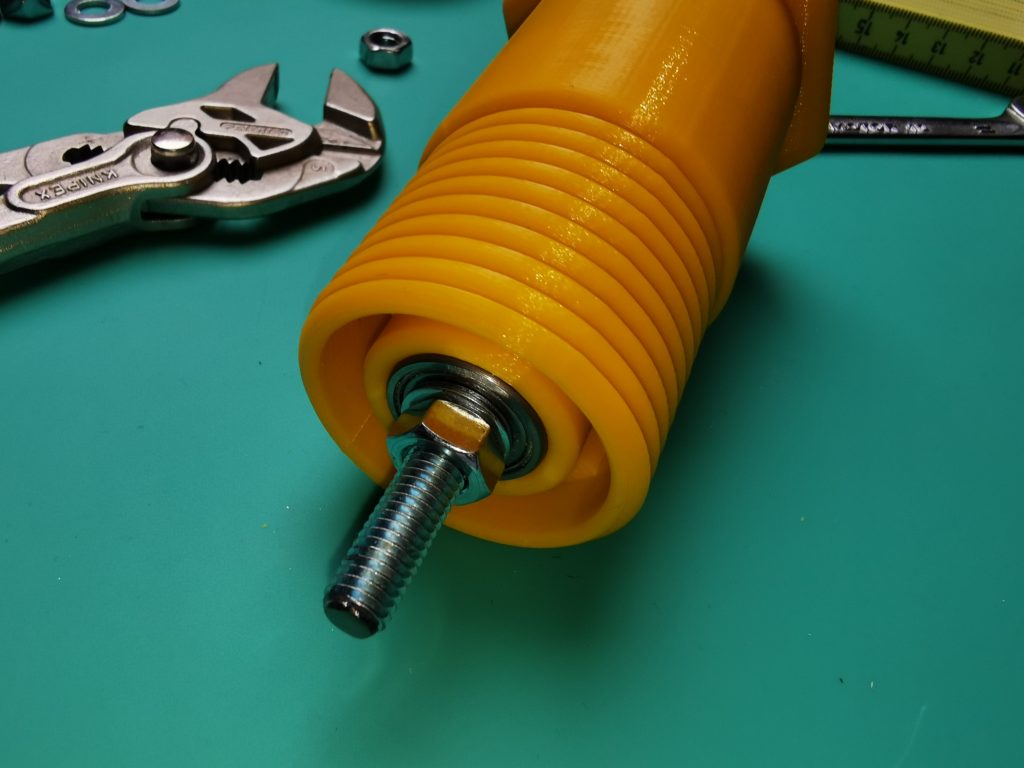
Die Stange wird wie im Bild oben eingesteckt. Auf der anderen Seite wird dann ein Wälzlager über die Gewindestange und in die Passung gelegt. Eine Mutter mit Unterlegscheibe fixiert das Lager in dieser Position (nur auf einer Seite!!). Diese Mutter wird nur mit den Fingern angeschraubt, denn wir wollen den Kunststoff nicht unter Spannung setzen. Damit die Mutter aber in Position bleibt, wird sie mit einer zweiten Mutter gekontert.
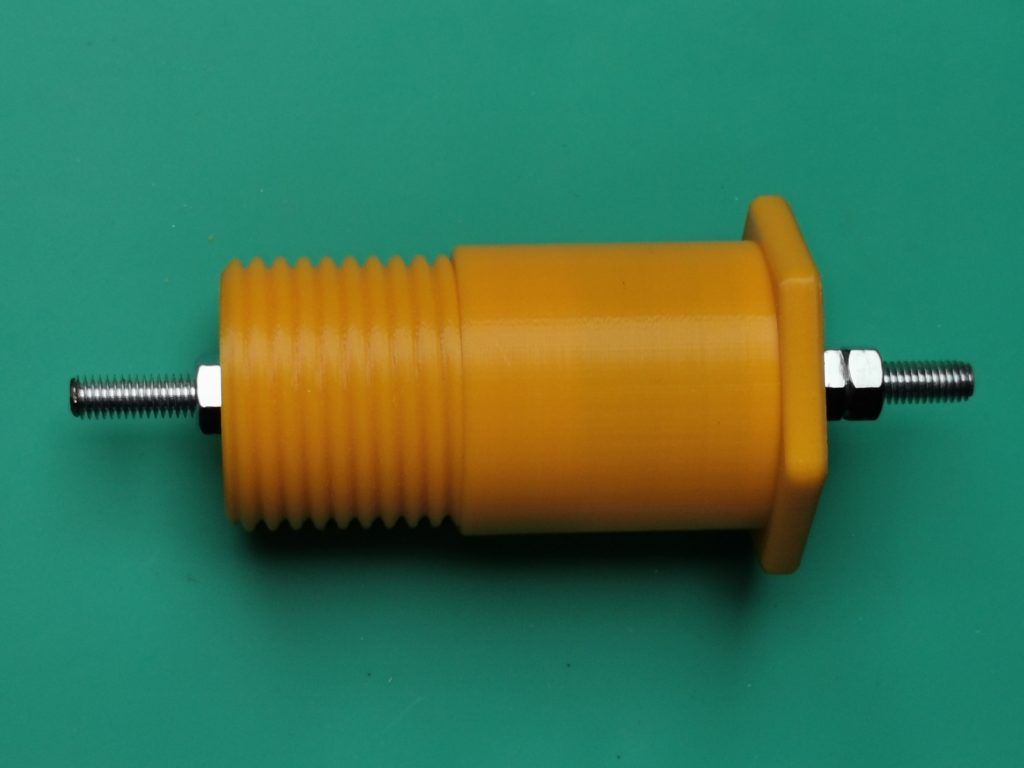
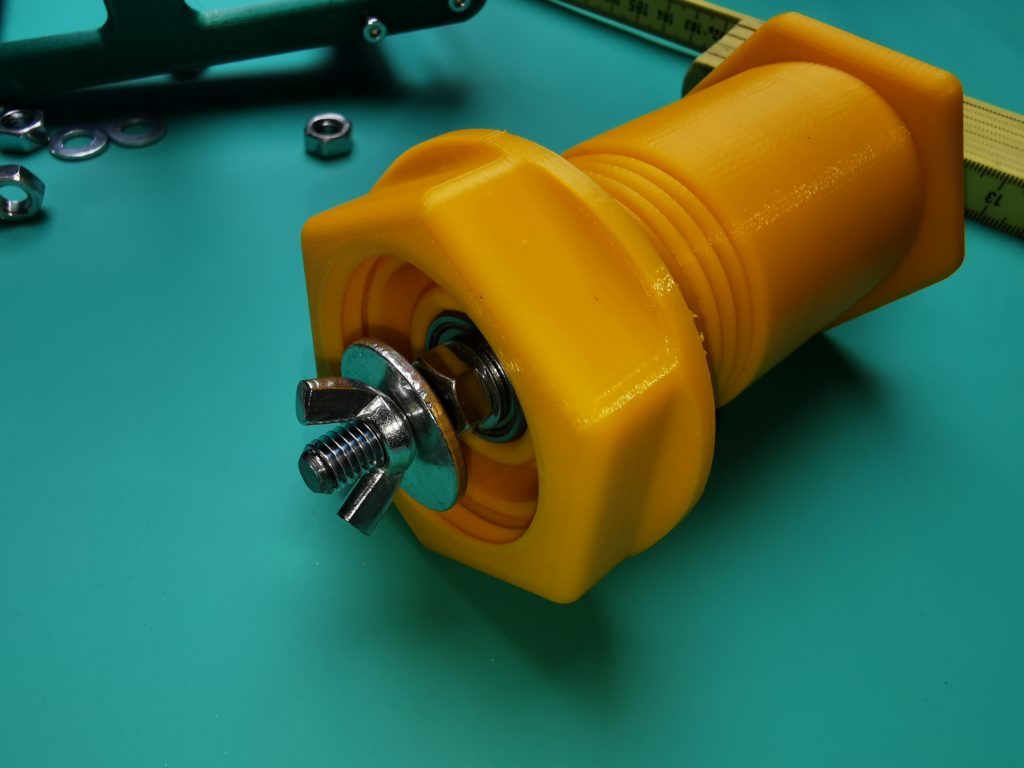
Den Abschluss bilden die locker aufgedrehten Flügelmuttern mit den großen Scheiben.
Auch mit dem Gestell war ich bezüglich Designerwägungen nicht zufrieden. Da die Abmessungen bekannt und erprobt waren, war eine Nachkontruktion in Fusion360 kein Problem.
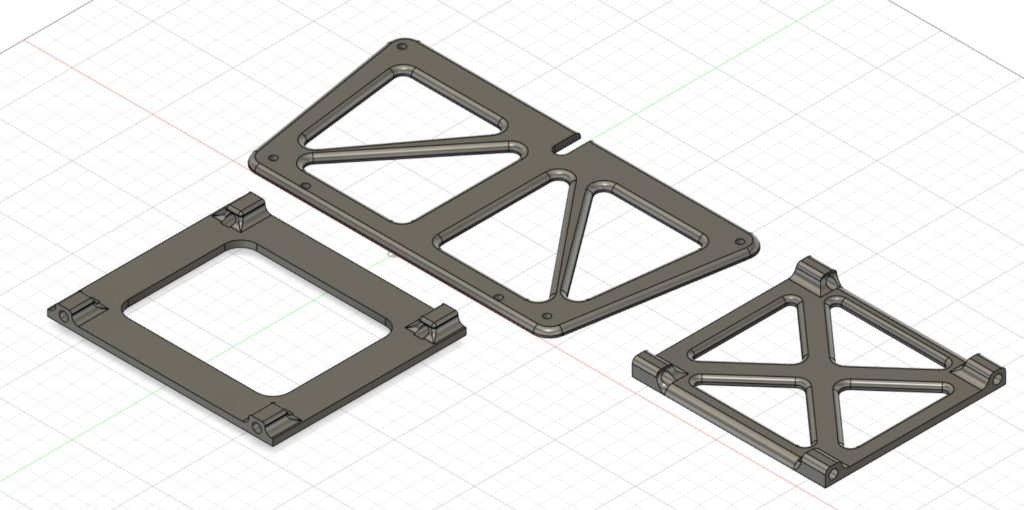
Oben mittig liegt ein Vorder-/Rück-Teil. Links liegt das Bodenteil und rechts ein Seitenteil. Auch hier wieder die Archivdatei zusammen mit den STLs in einem ZIP-Archiv.
In das Bodenteil und in die Seitenteile müssen erst noch 4mm Ruthexgewinde eingeschmolzen werden. Die passenden Löcher wurden konstruktionsseitig bereits vorgesehen (5,6mm). Ich kann nur wärmstens empfehlen beim 3D-Druck diese Art von Verschraubungen zu benutzen. Auch ich kenne noch die Möglichkeit 6-kant-Passungen für Muttern zu drucken. Ein viel zu großer Aufwand im Vergleich zu dieser Methode mit den einzuschmelzenden Gewindehülsen. Auch die Festigkeit ist wesentlich höher.
Als Amazon-Partner verdiene ich an qualifizierten Verkäufen. Für den Käufer ändert sich der Preis dadurch nicht. |
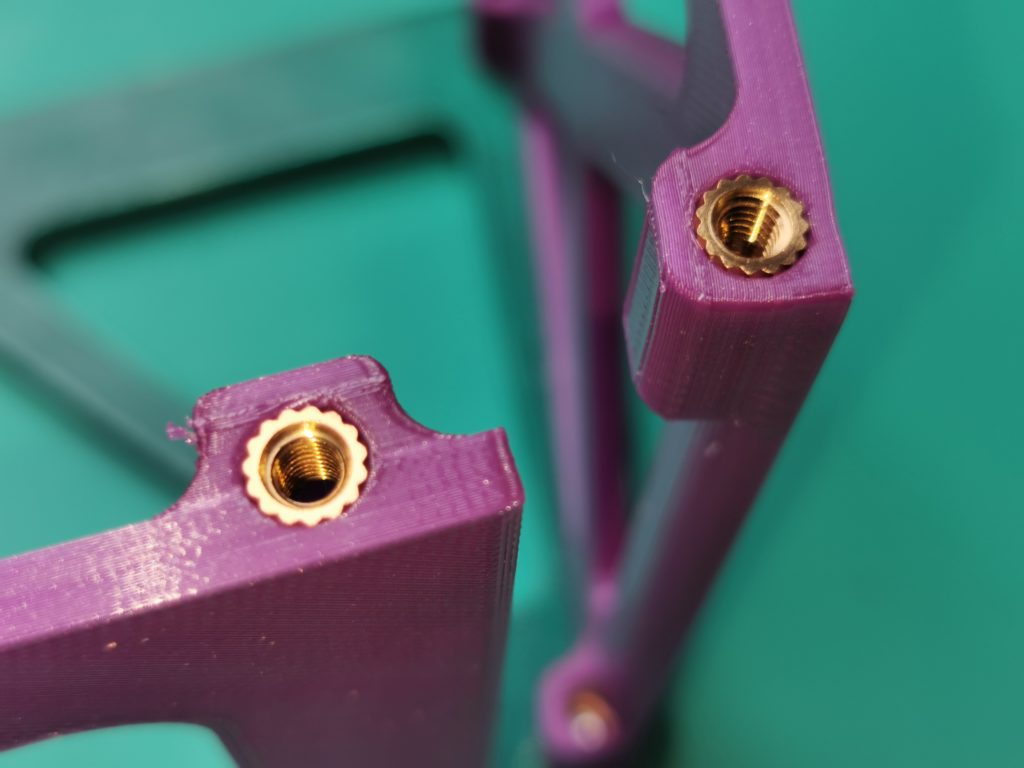
Den „Käfig“ aufzubauen ist wirklich ein Kinderspiel.
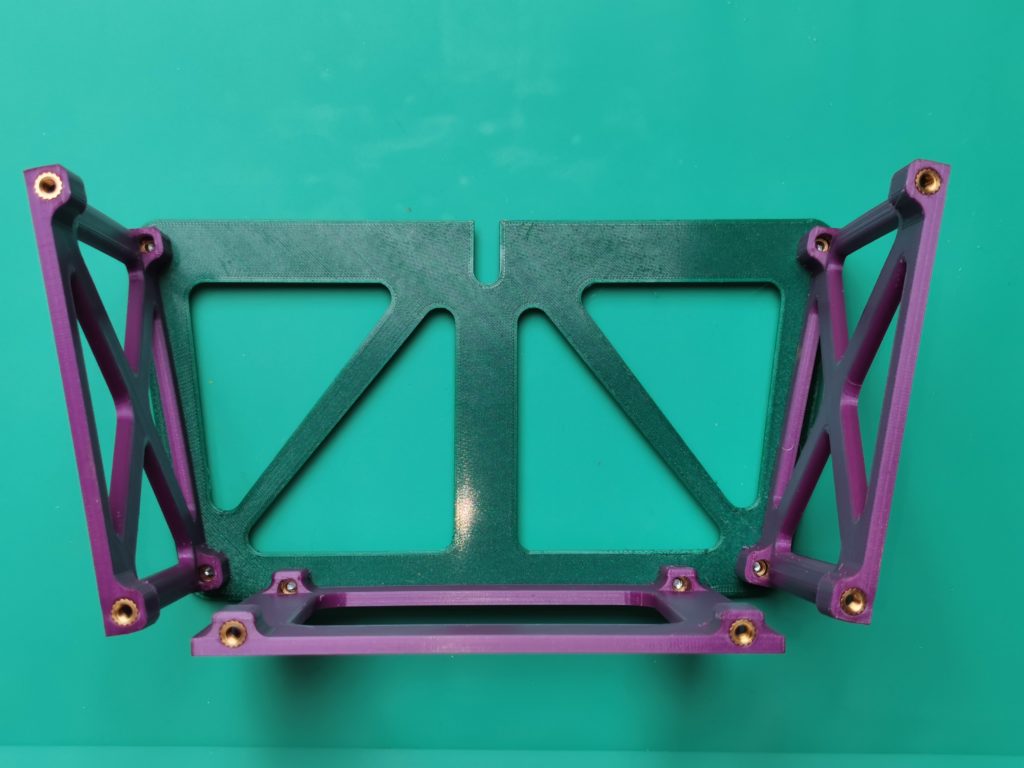
Der fertige Spulenhalter sieht dann so aus:
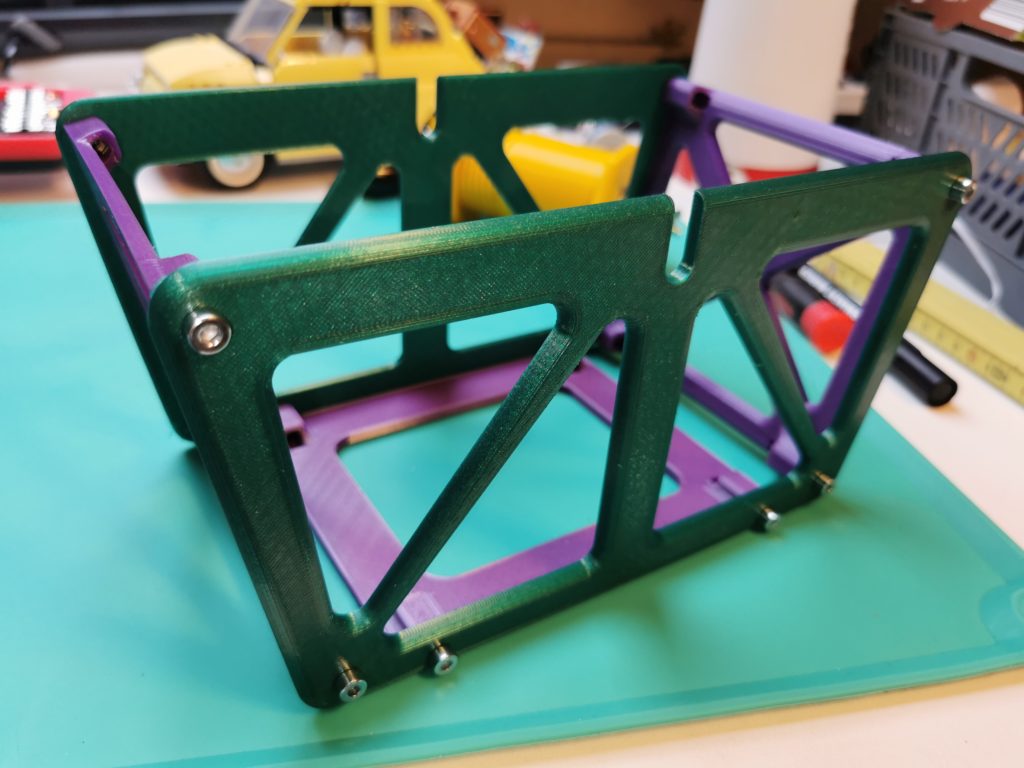
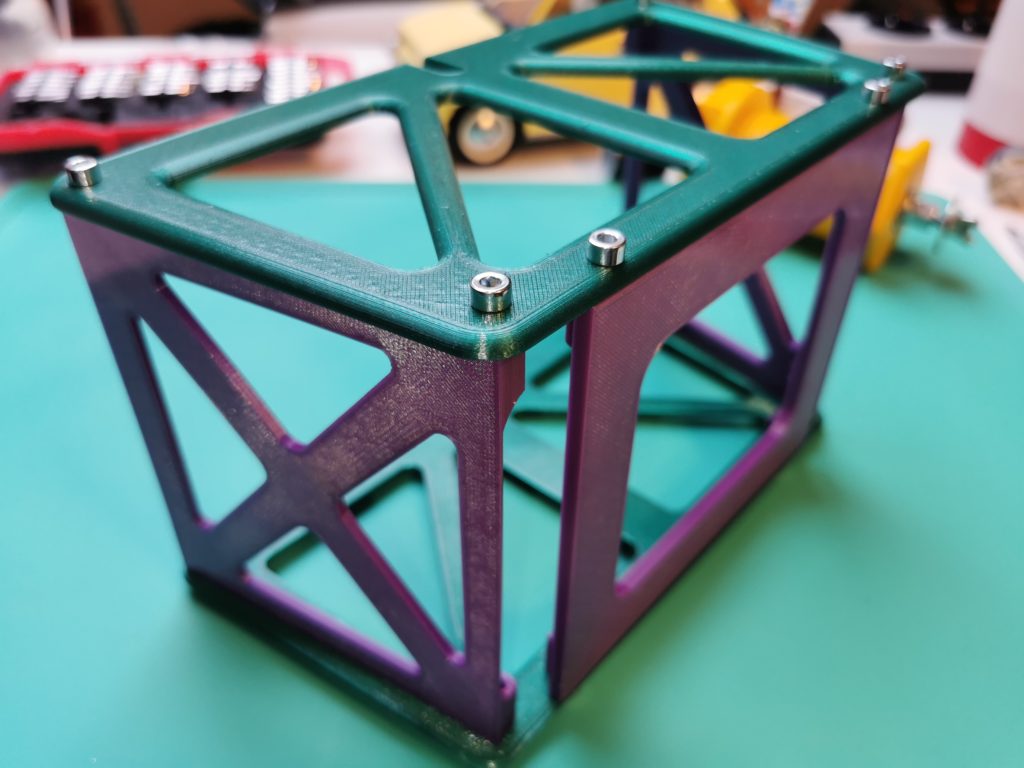
Natürlich soll ein Gesamtbild mit eingelegter Filamentspule nicht fehlen.
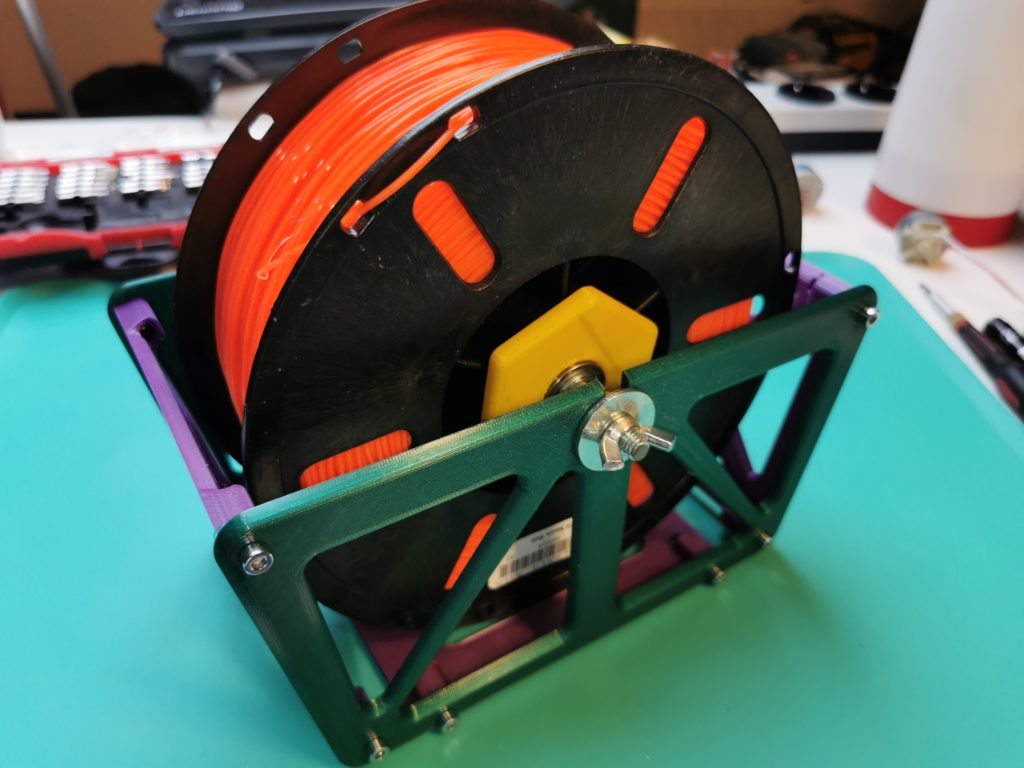
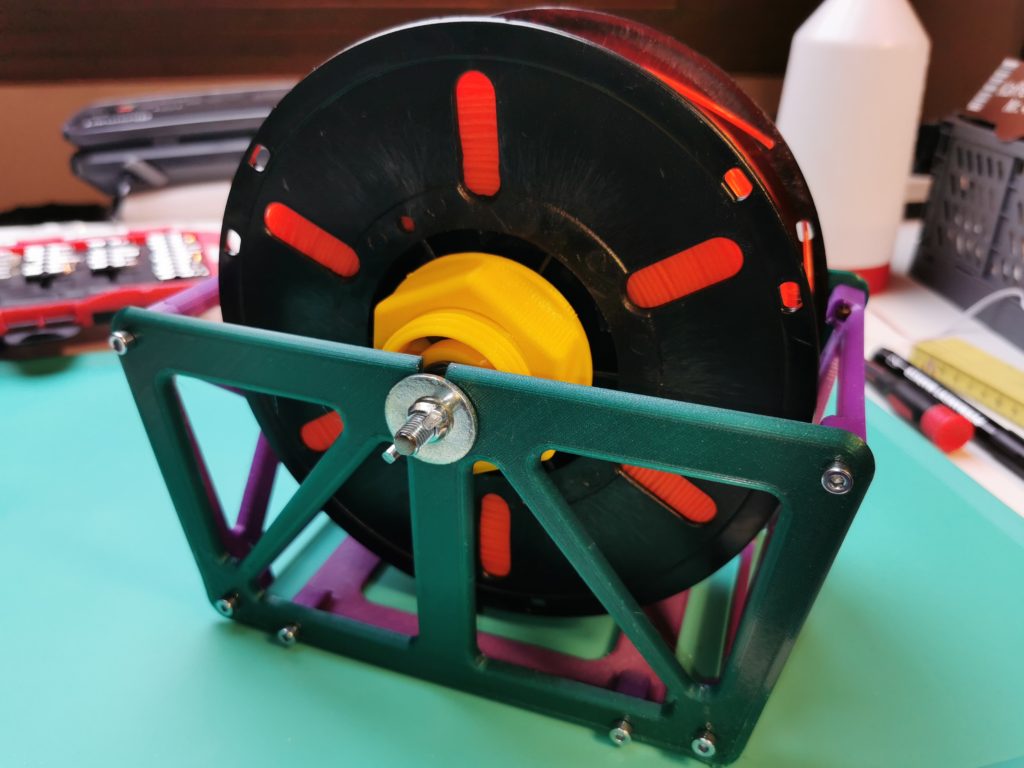
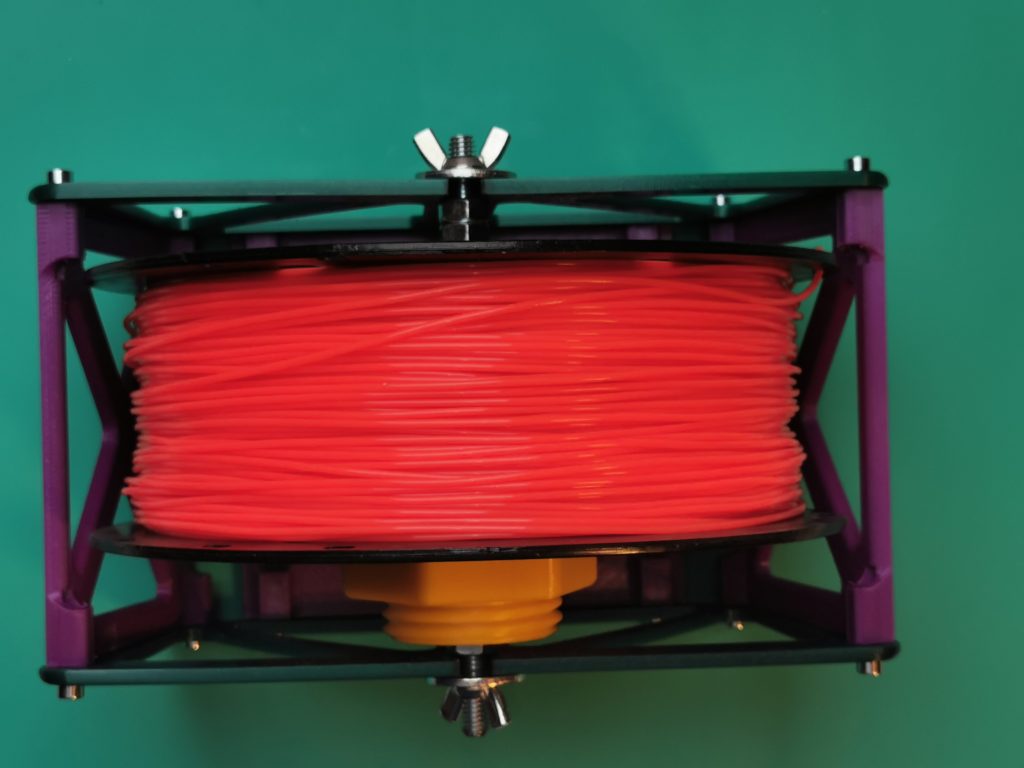
Viel Spaß beim Nachbau und beim Drucken.