Mittlerweile schon der 8. Teil. Diesmal bekommen die Druckerkomponenten Kontakt mit dem OctopusPro-Board.
Ich habe die einzelnen Schritte extra so klein aufgeteilt, damit alles nachvollziehbar bleibt. Für den Einen mag das etwas ermüdend sein, Andere sind darüber vielleicht glücklich. Man kann es nicht allen Recht machen.
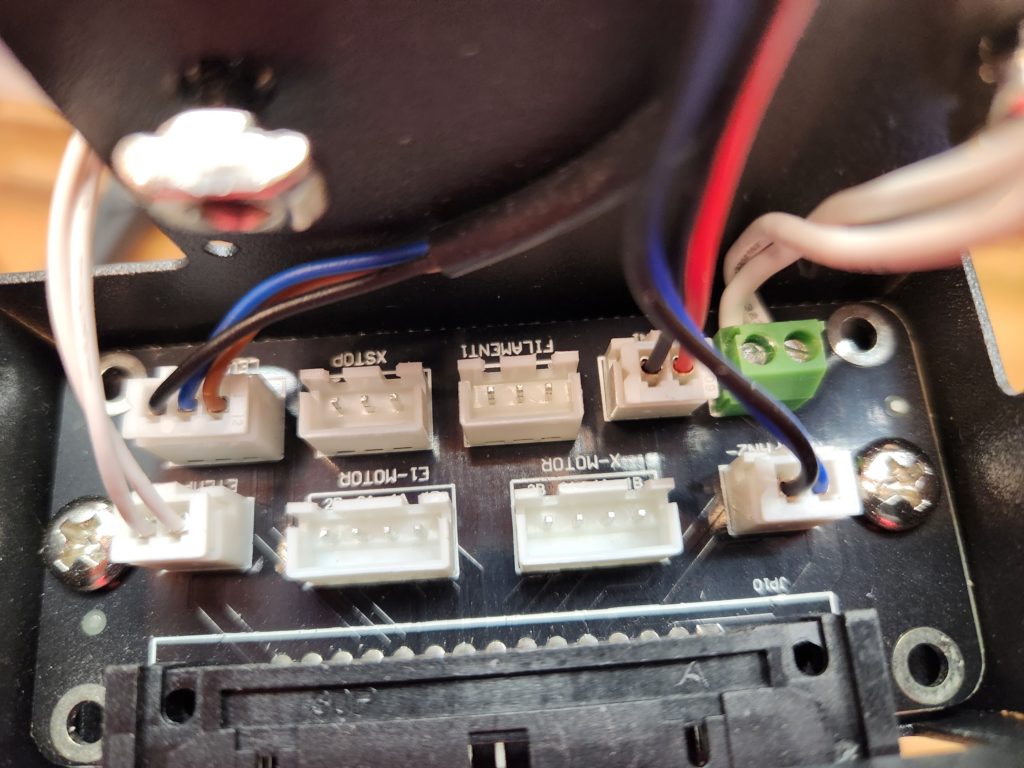
Ein paar Leitungen sind bezeichnet, aber eben nicht alle. Ich empfehle, dass man die Leitungen kennzeichnet, bevor man sie von der Adapterplatine löst, denn auf ihr sind die Bezeichnungen noch aufgedruckt.
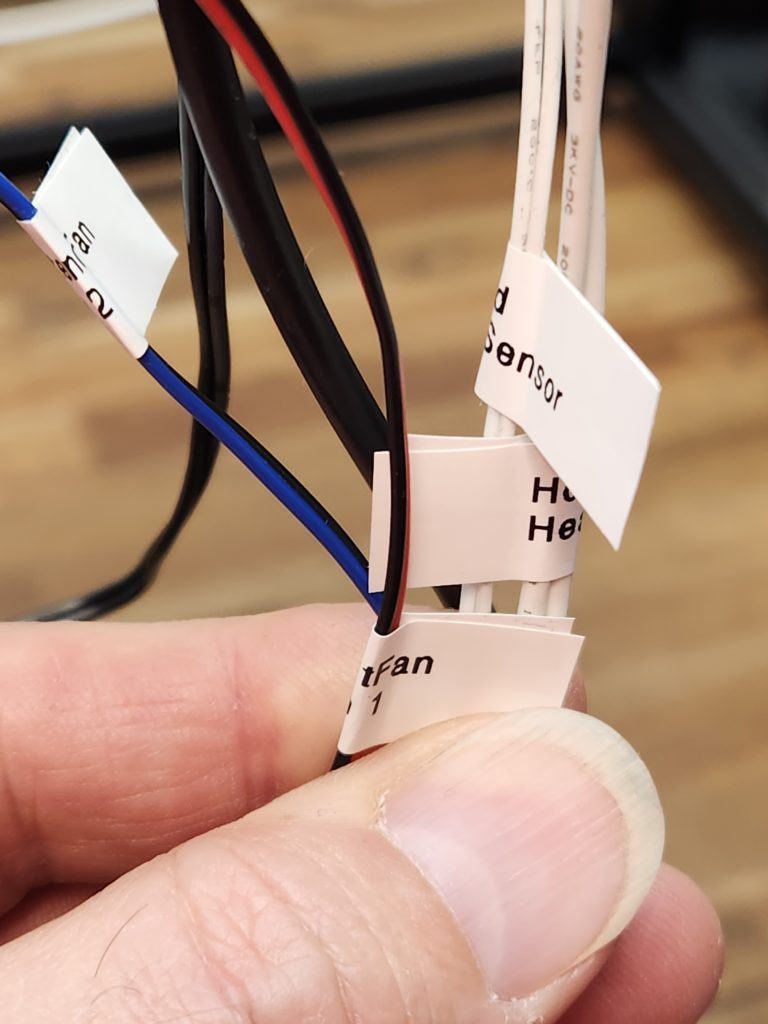
Kleiner Einschub: Ich habe ja schon auf einigen Bildern meine Kabelfahnen gezeigt. Wer öfters Kabel bezeichnen will, oder auch andere Dinge belabeln möchte, ist ganz gut mit einem mobilen Beschriftungsgerät beraten. Ich nutze seit Jahren zwei Brother Geräte. Eines ist stationär für eher komplizierte Dinge, die ich am Computer entwerfe. Wesentlich wichtiger ist aber ein voll mobiles Gerät mit Batterie- oder Akkubetrieb. Ein Beispiel wäre dies:
Dieses Gerät hat sogar noch den Vorteil, dass es speziell für Kabelbeschriftung ausgelegt ist und zudem zusätzliche Symbole ermöglicht. Als Amazon-Partner verdiene ich an qualifizierten Verkäufen. Für den Käufer ändert sich der Preis dadurch nicht. |
Zurück zum eigentlichen Thema. Ich habe versucht, so viele Kabel wie möglich vom ursprünglichen Zustand zu übernehmen. Das bedeutete auch, dass Kennzeichnungen getauscht werden mussten.
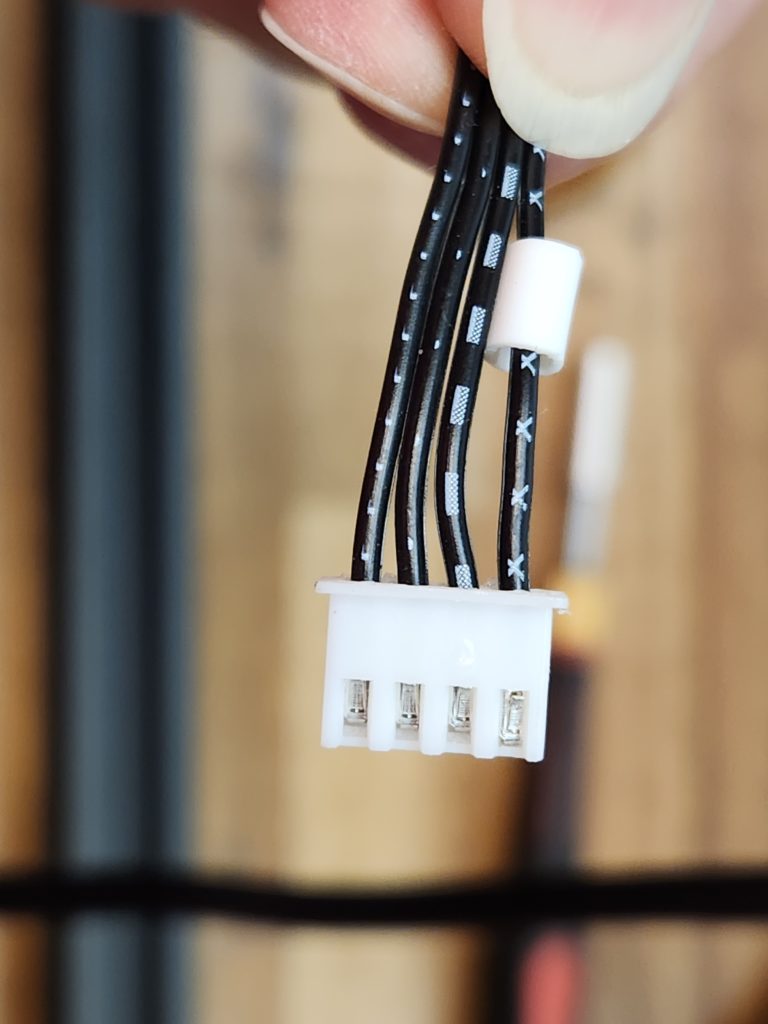
Der kleine weiße Ring kennzeichnet die Achse an dessen Stepper dieses Kabel hing. Man kann mit einem spitzen Gegenstand die kleinen Metallzungen im Stecker eindrücken und dann die einzelne Leitung herausziehen. Vor dem Zurückstecken muss eventuell die Metallnase wieder etwas aufgerichtet werden. Bei beiden Vorgängen sollte man vorsichtig zu Werke gehen. Die Zungen brechen bei übermäßiger Belastung ab und dann ist dieser Metallkontakt nicht mehr verwendbar und muss ausgetauscht werden.
Auch beim Durchziehen der Leitungen durch die Energiekette zwischen hinterem oberen Rahmen und dem Extruder muss gegebenenfalls ein Stecker wie oben beschrieben zerlegt werden. Foto vom Ursprungszustand machen ! Das oben gezeigte Kabel kann beispielsweise nicht durch die Energiekette gezogen werden, da der Stecker zu breit ist. Beim Querlegen würden die Kontakte und Leitungen leiden. Ich habe also ein Foto gemacht, alle Leitungen aus dem Plastikteil gezogen, einen Schrumpfschlauch über die Kontakte gezogen und konnte dann ganz leicht das Kabel durch die Energiekette ziehen.
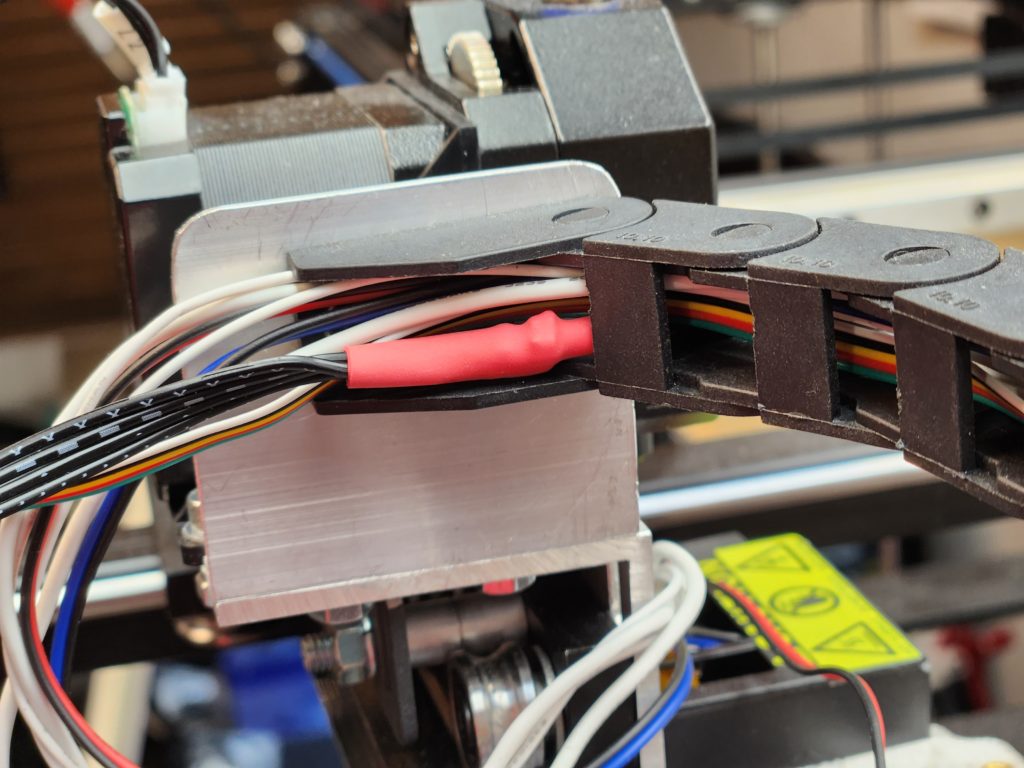
Die neue Box mitsamt OctopusPro-Board habe ich am hinteren Rahmen oben montiert. Vermutlich werde ich aber noch eine zusätzliche Strebe einbauen. Das sieht mir doch etwas zu instabil aus.
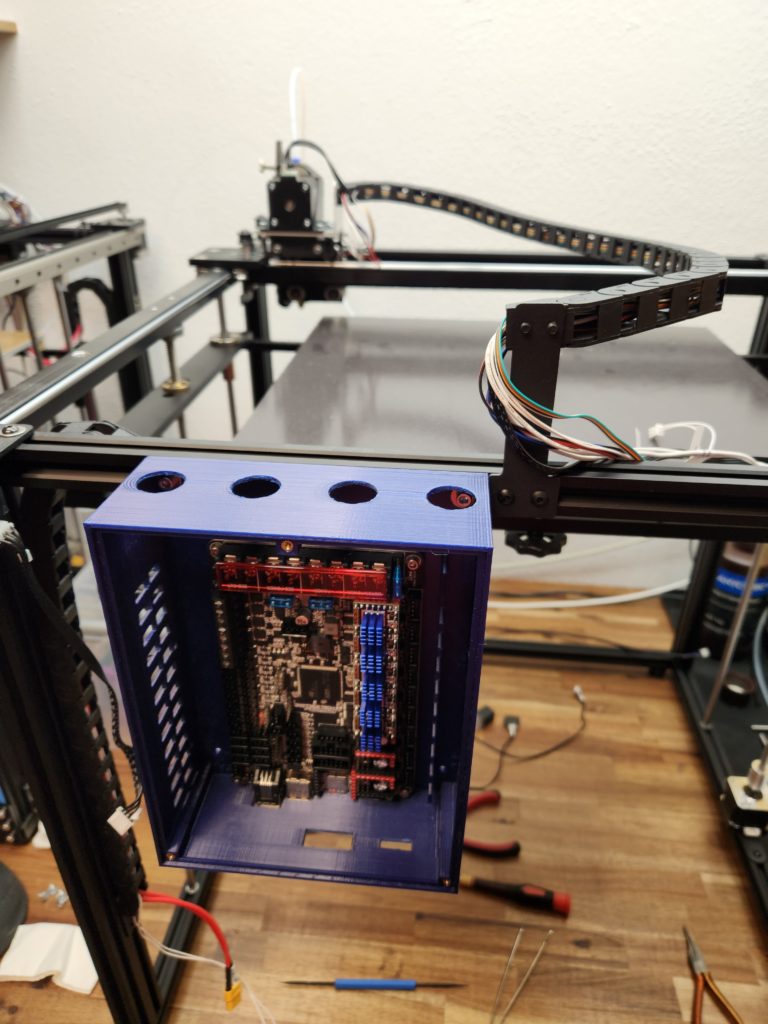
Das vom Extruder kommende Kabelbündel wird in die Box geführt.
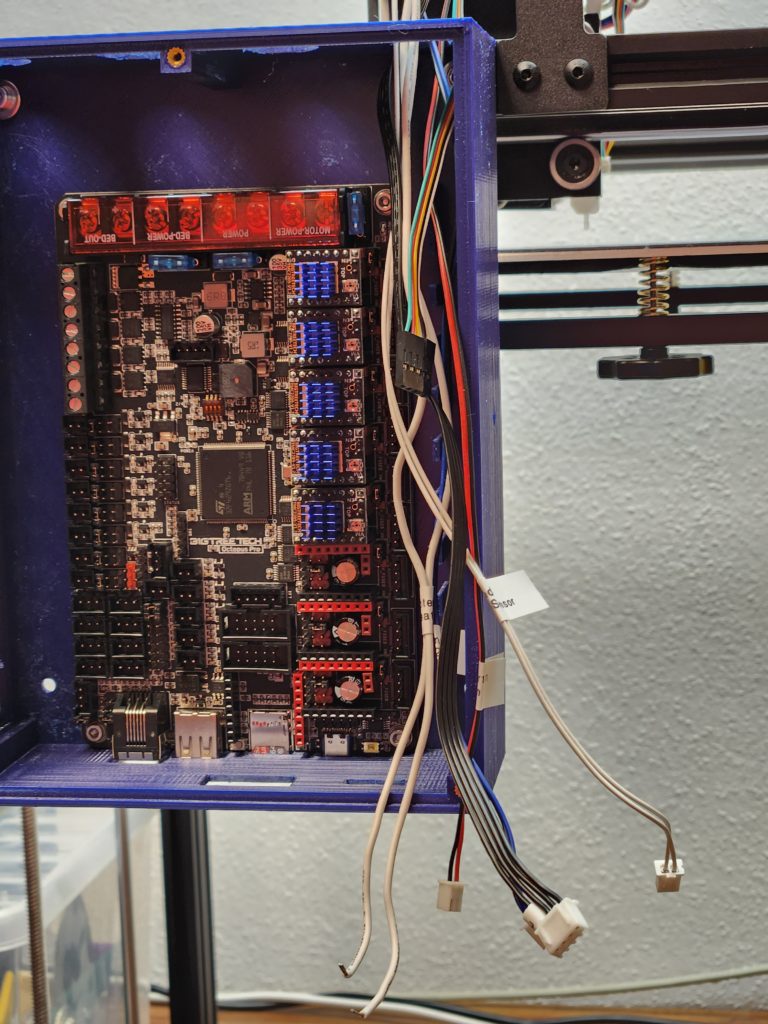
Die meisten Kabel sind ja lang genug. Nur das bunte Kabel vom BL-Touch macht mir Sorgen.
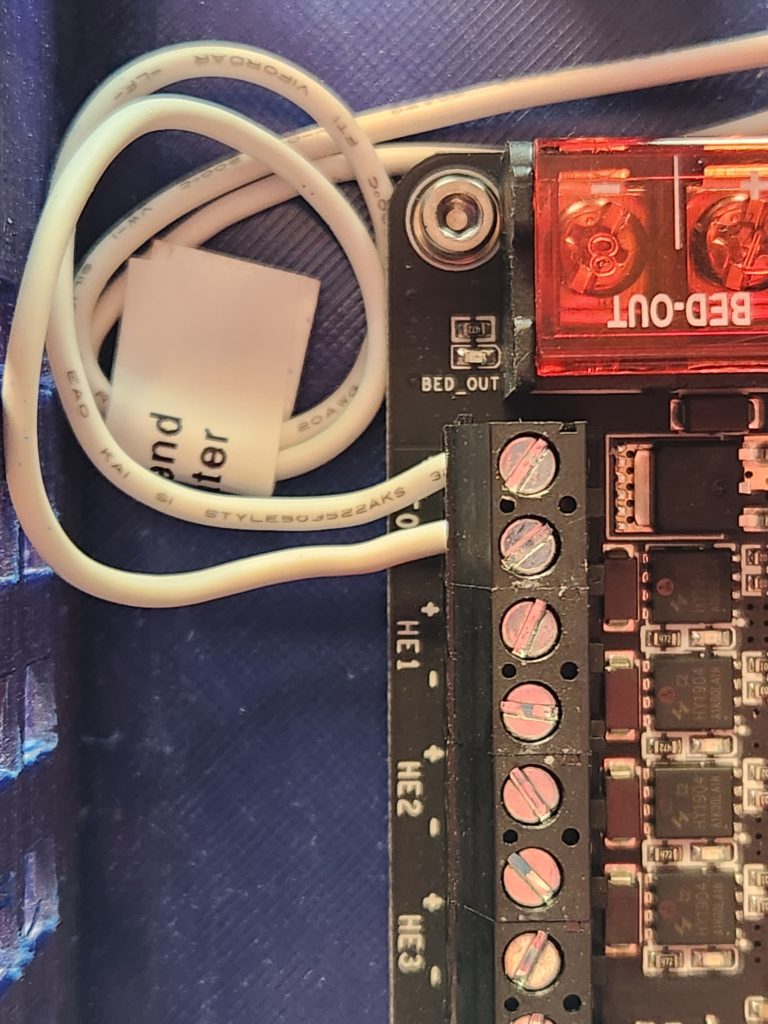
Die Heizung vom Hotend findet ihrenPlatz. Polarität spielt weder beim Sensor (Zweidraht-Typ) noch bei der Heizung selbst eine Rolle.
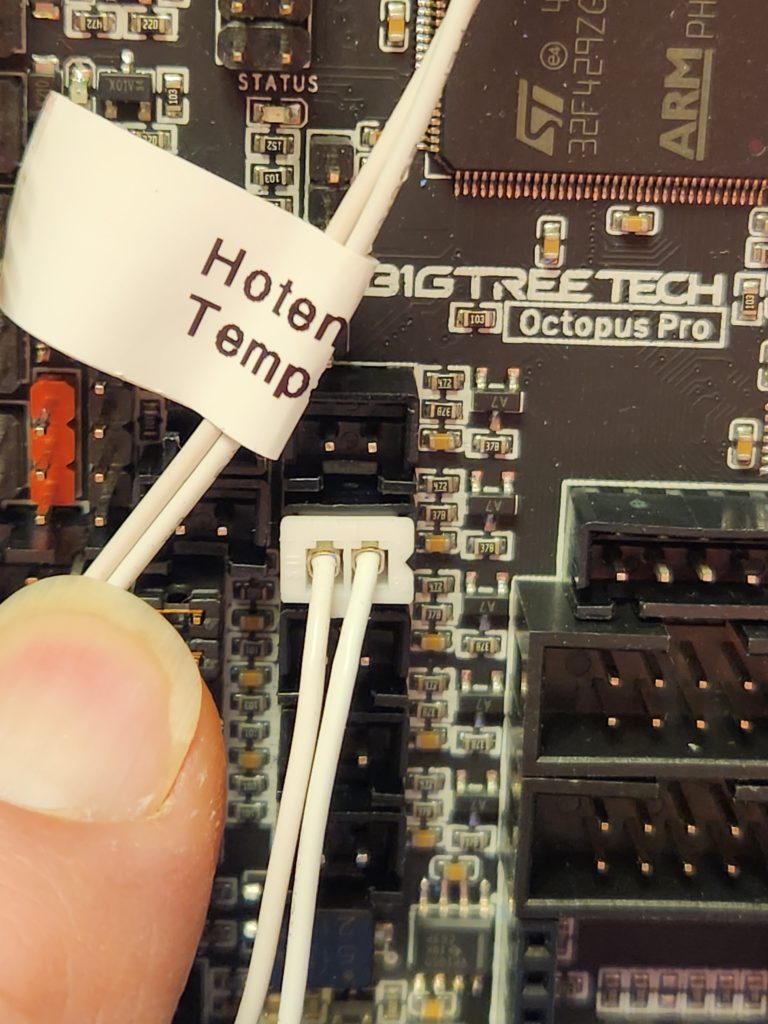
Der obere Steckplatz ist für den Temperatursensor des beheizten Druckbetts. Der zweite Platz gehört zum Hotend 0.
Eine kleine Falle stellt uns Tronxy dann auch noch, denn die Kontaktierung der Lüfterstecker weicht vom Standard ab. Bitte an dieser Stelle selbst nochmal alles diesbezüglich überprüfen, denn die Lüfter nehmen ein Verpolen krumm.
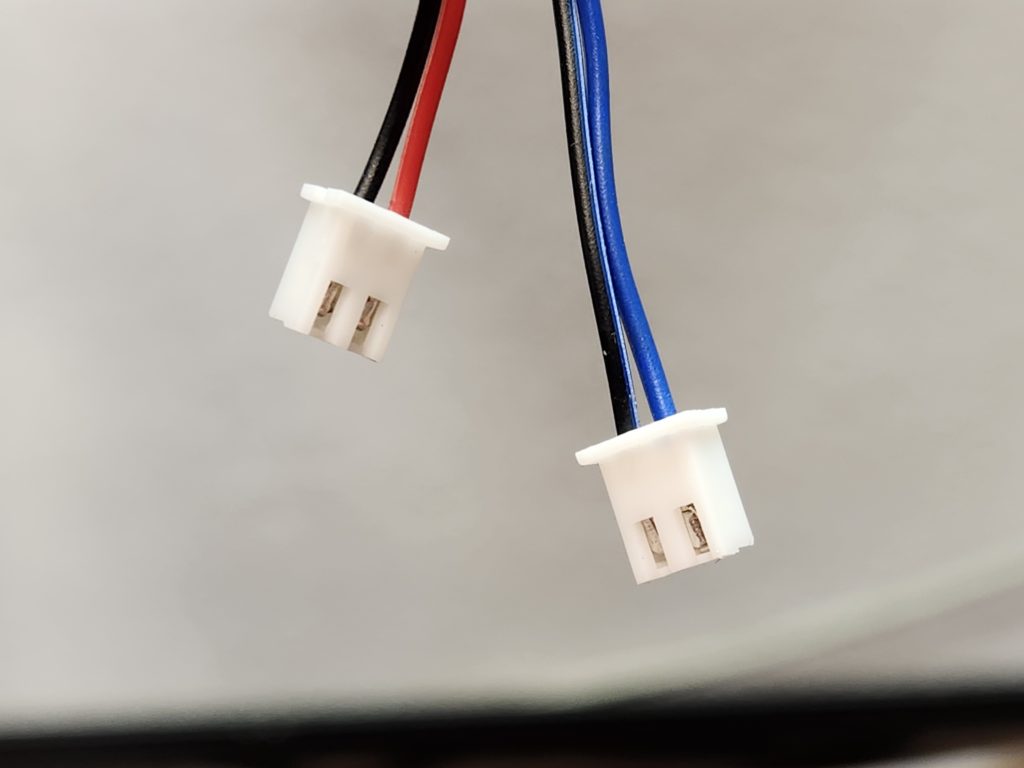
Das ist die Belegung bei Tronxy. Der schwarze Draht ist immer GND. Rot bzw. blau ist Plus.
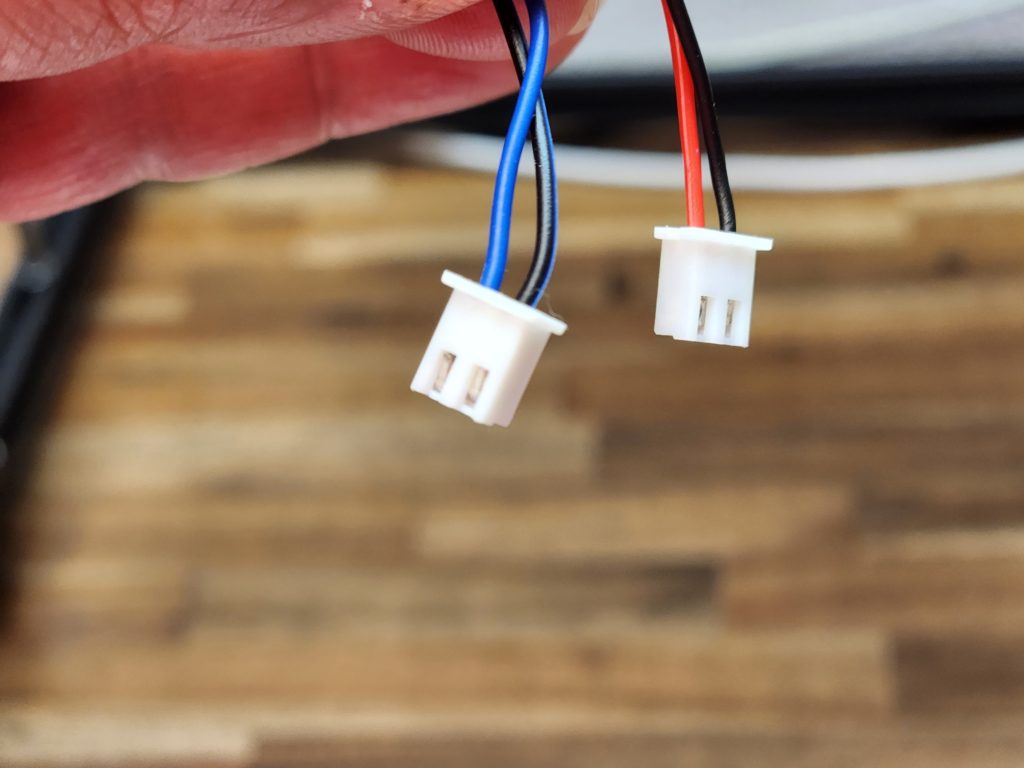
Nach dem Wechsel der Belegung.
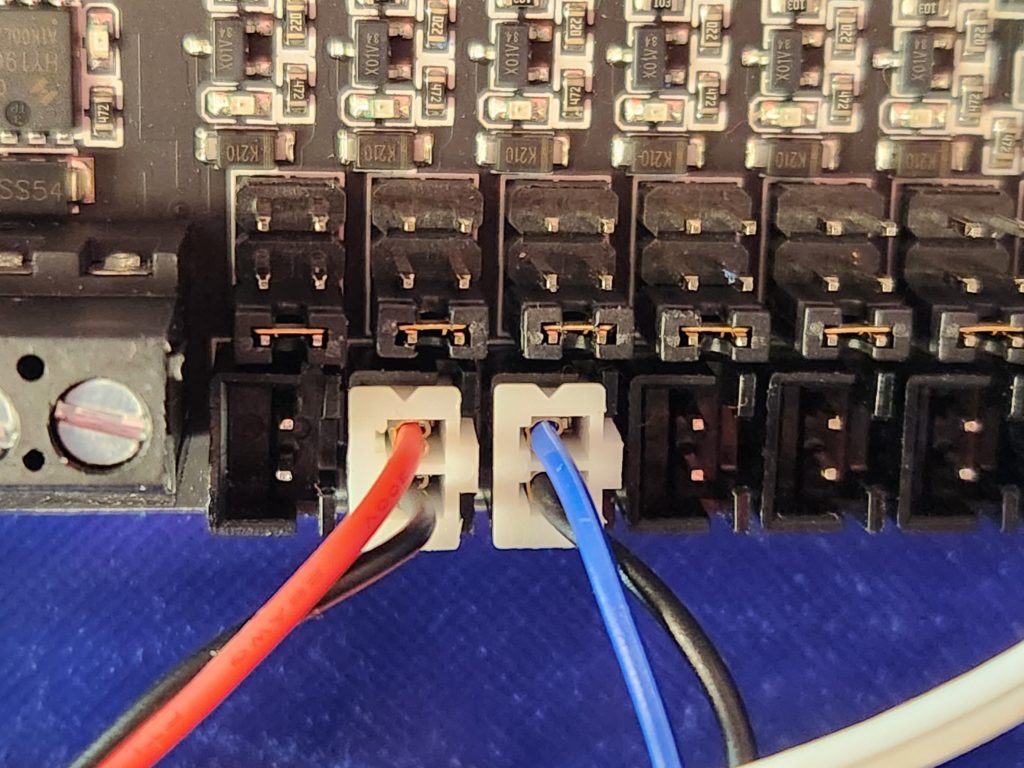
Im entsprechenden Steckplatz angekommen. Auch hier beginnt die Zählung mit FAN0. Der Definition nach ist aber FAN1 der Bauteilkühler und FAN2 der Hotendkühler. Das wurde schon in einem der ersten Beiträge dieser Serie in der Firmware so definiert.
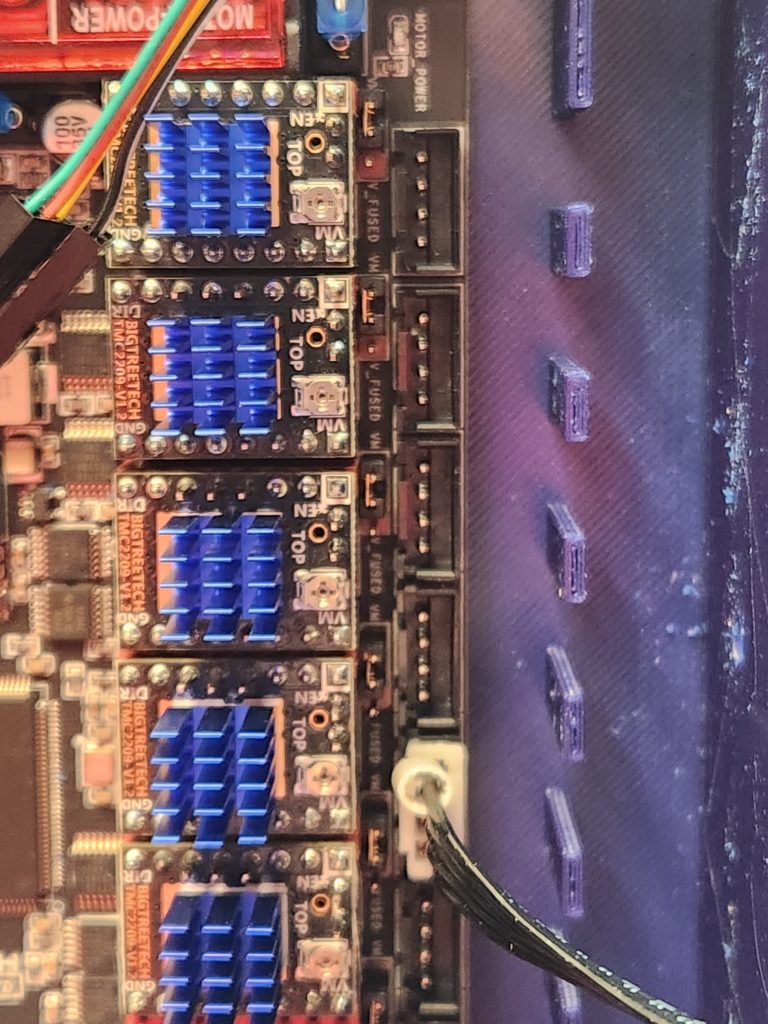
Der Extruder-Stepper kommt an den 5. Steckplatz. Das ist ebenfalls in der Firmware so definiert und stellt auch einen gewissen Standard dar. Die Reihenfolge der Steckplätze ist: X, Y, Z, Z‘ (bei mir ungenutzt), Extruder, Z2.
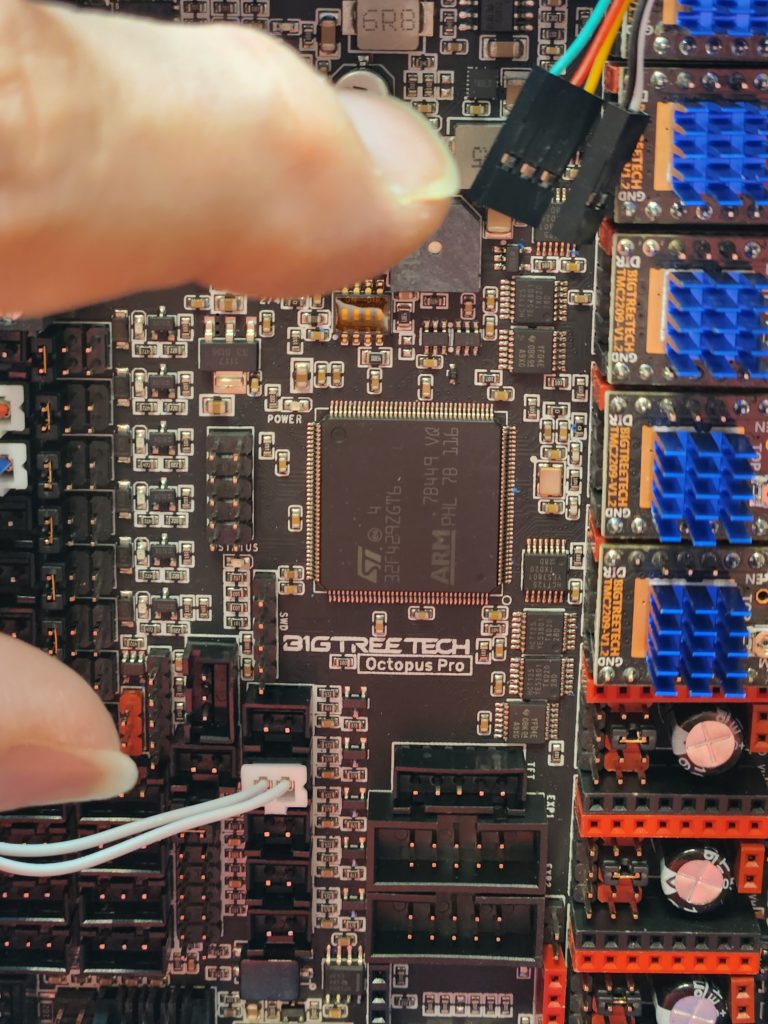
Wie schon bemerkt reicht die Kabellänge des BL-Touch nicht aus. Das war aber auch beim alten Tronxy so. Dem Lieferumfang des BL-Touch liegt ein kurzes und ein langes Kabel bei. Ich habe das kurze Kabel kurzerhand geändert und damit dann die Länge erreicht.
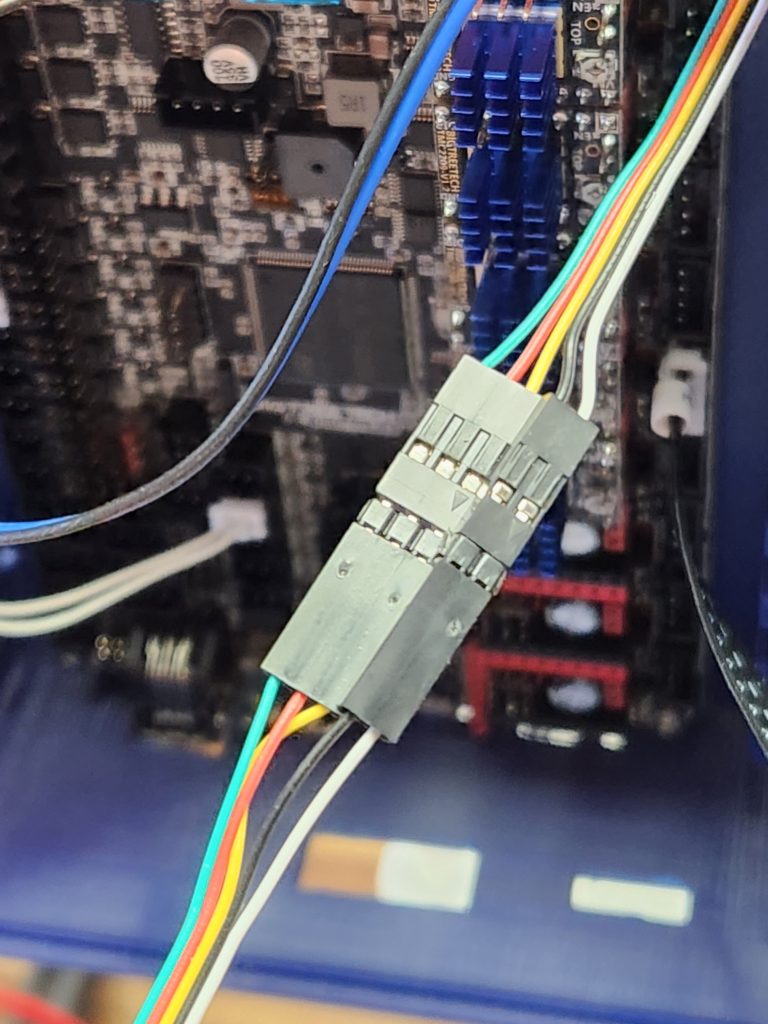
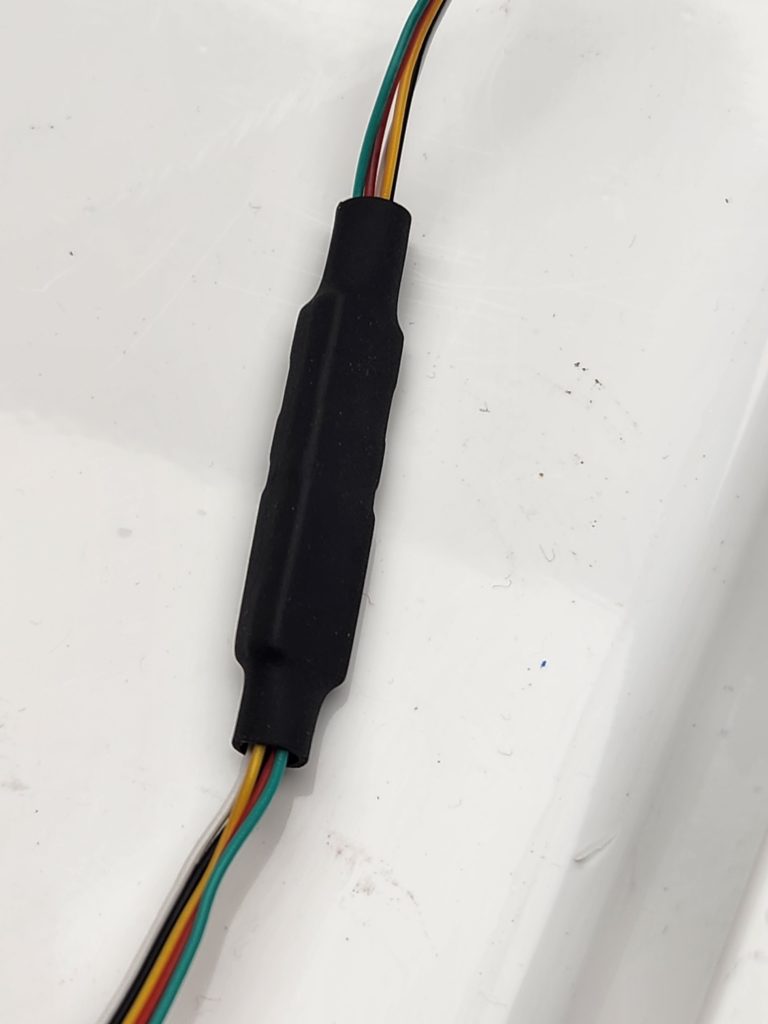
Der Schrumpfschlauch erfüllt hier nur mechanische Zwecke. Er sichert ab, dass sich die beiden Verbindungen nicht lösen können.
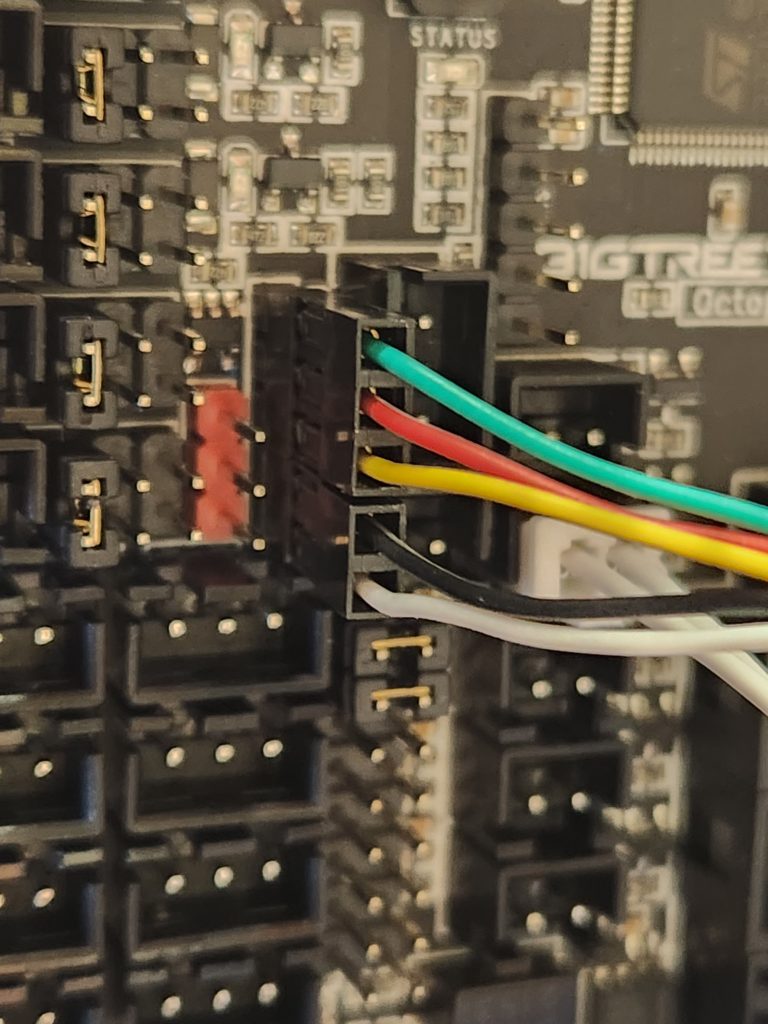
Beim Verbinden ist wieder Vorsicht geboten. Die verschiedenen Hersteller des BL-Touch oder 3D-Touch oder … verwenden unterschiedliche Farben an unterschiedlichen Kontakten bzw. Signalen. Da hilft nur die Dokumentation zu lesen.

Diese Belegung und genauere Erklärungen hatte ich im Firmwarebereich schon gezeigt.
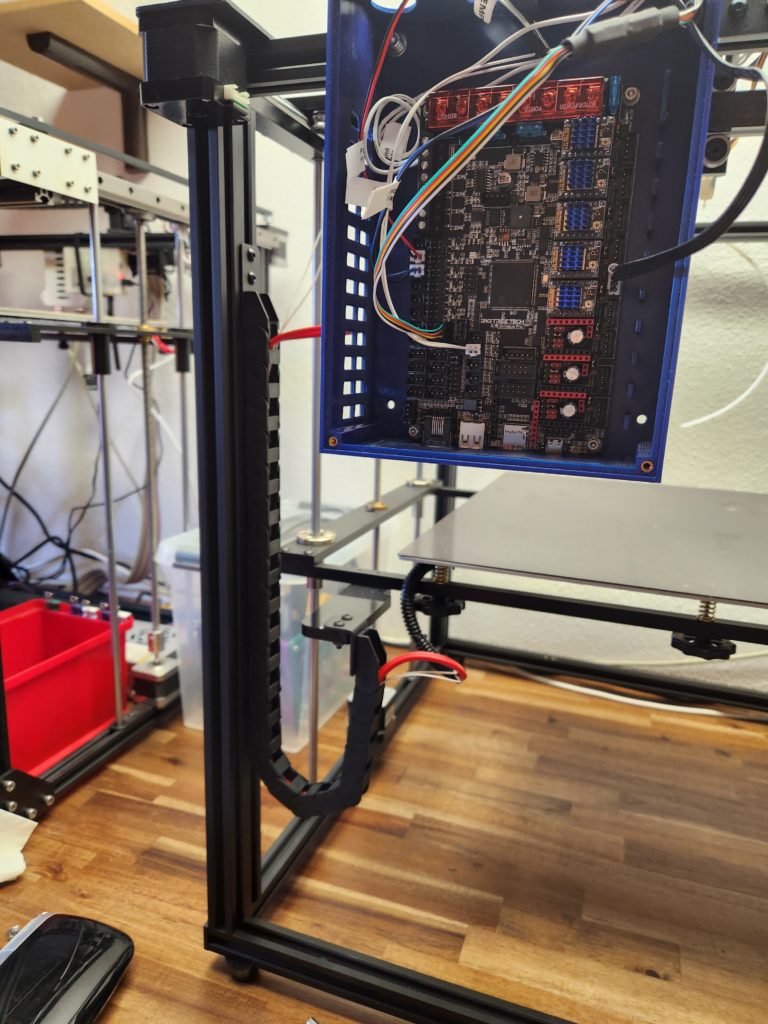
Die Energiekette zwischen Strebe hinten rechts und Druckbett muss umgedreht werden. Ursprünglich war die Elektronikbox unten. Jetzt ist sie oben. Hier muss man ausprobieren, wo der beste Befestigungspunkt an der Strebe liegt indem man das Druckbett einmal runter und wieder hoch dreht und dabei die Energiekette im Auge behält.
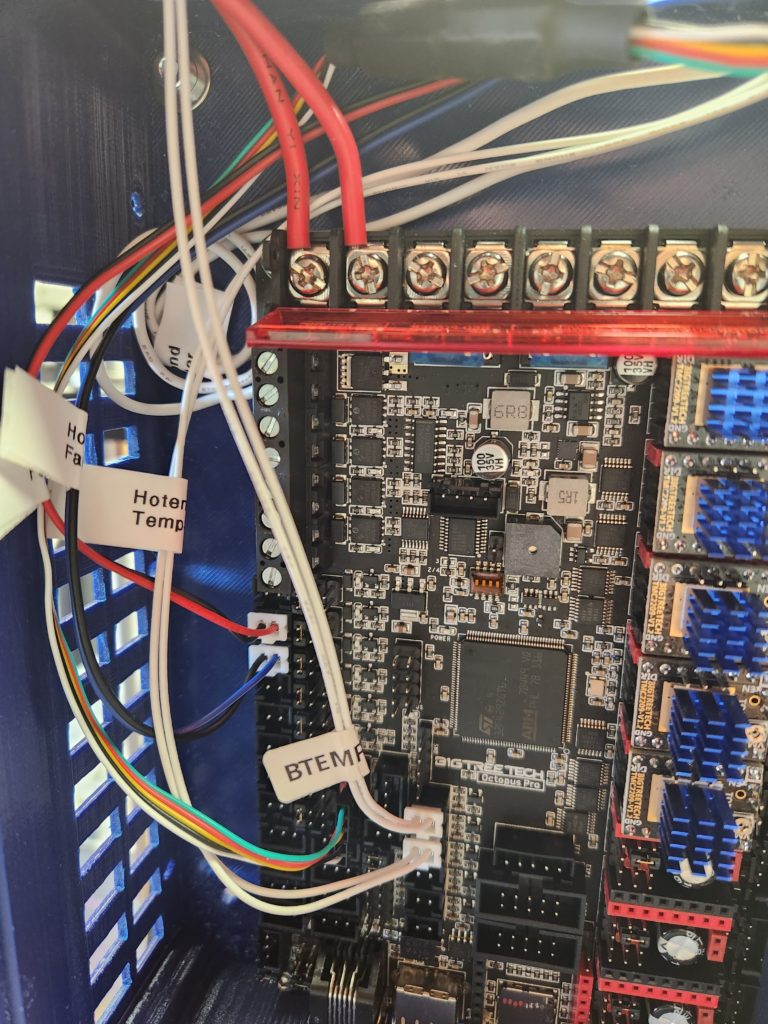
Danach finden auch Heizung des Druckbettes und der entsprechende Temperaturfühler ihren Platz auf der Platine. Auch wenn der Anschluss anderes suggeriert: Die Polung der Heizung ist völlig egal.
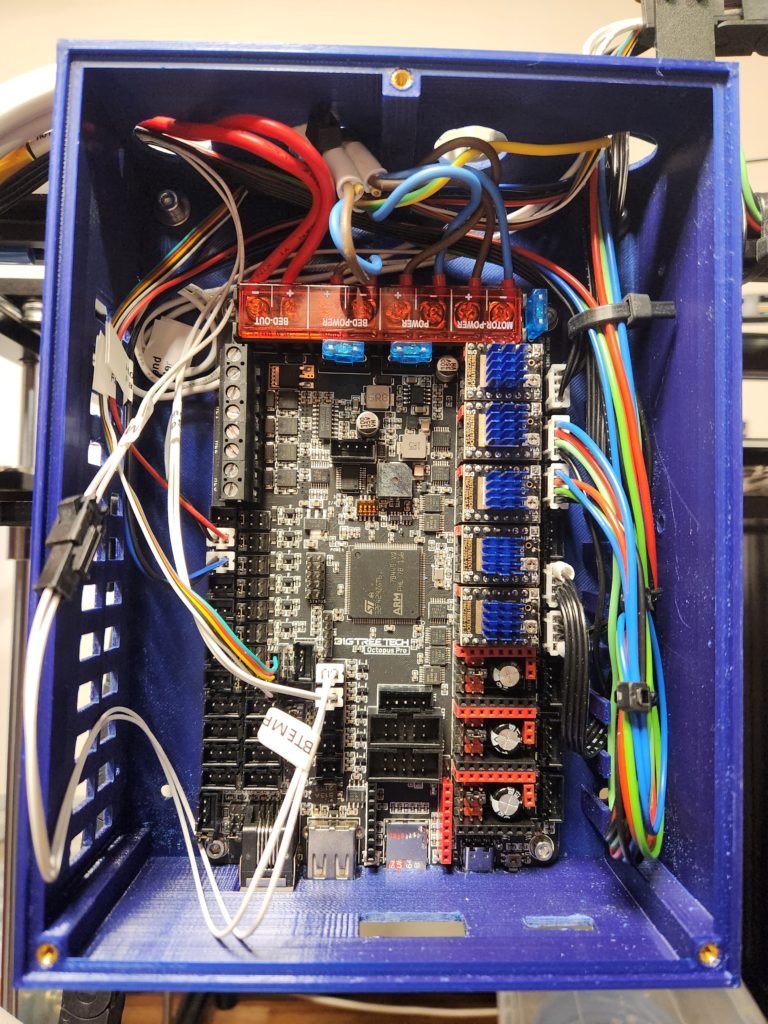
Für die Stepperanschlüsse musste ich teilweise neue Kabel konfektionieren. Die platinenseitigen Stecker sind problemlos, sofern man die notwendige Crimpzange hat. Bei den 6-poligen Steckern an den Steppern verzweifle ich regelmäßig und bin jetzt schon dazu übergegangen sie lieber zu löten. Trotzdem ist das nicht gerade einfach.
Man sollte in der Box unbedingt für Ordnung sorgen und mit Kabelbindern die einzelnen Leitung etwas „zähmen“. Rechts habe ich das bei den Stepperleitungen schon getan.
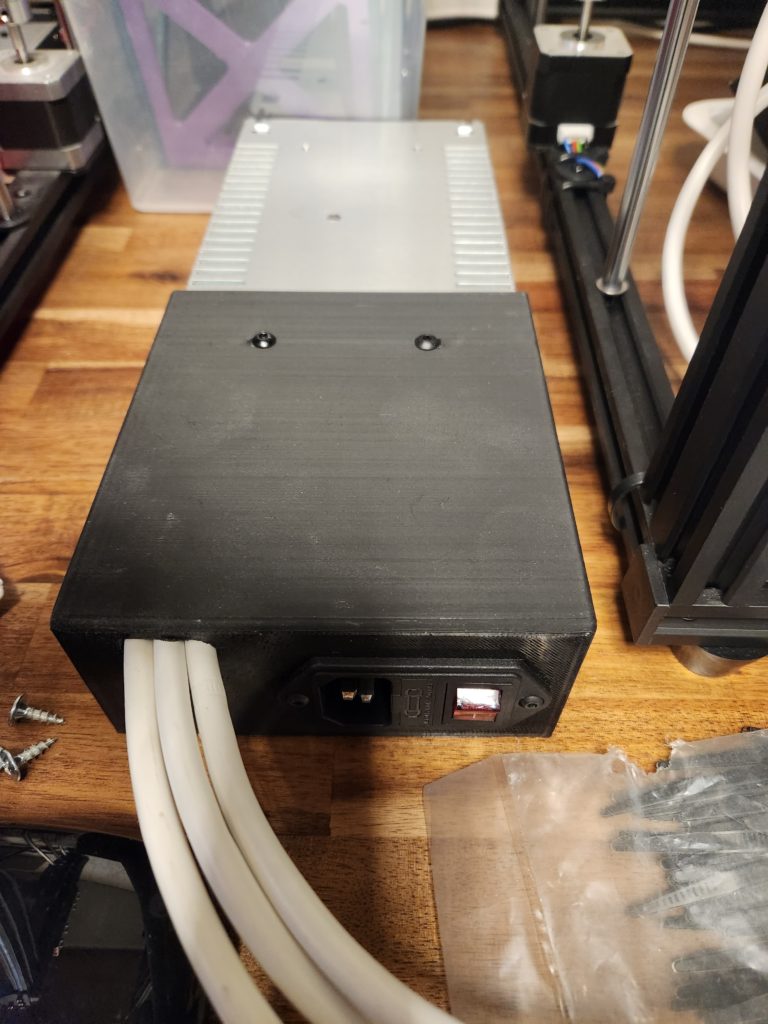
Ich habe die Stromquelle doch noch einmal etwas angepasst. Anstatt eine Leitung in die Octopus-Box zu führen und dort zu verteilen, nutze ich die drei Anschlüsse am Netzteil und gehe mit drei Leitungen nach oben. Dort bekommt dann jede Bedarfsstelle ihr eigenes Kabel: Board, Heizung, Motoren.
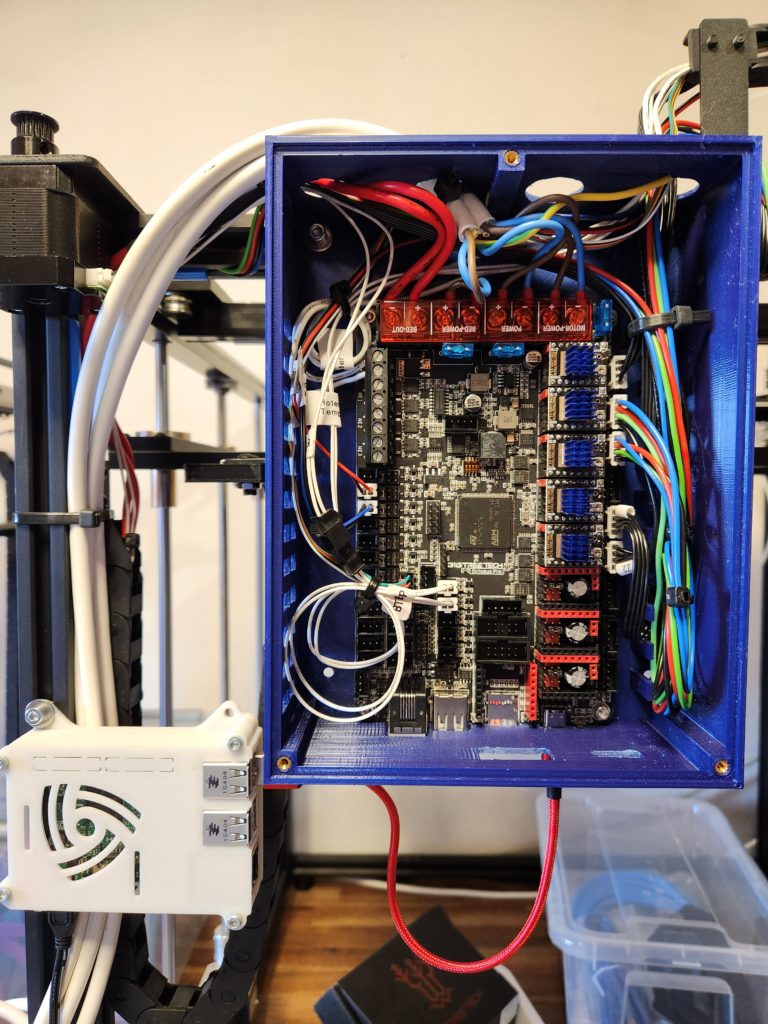
Auch der Raspberry-Pi, der die Steuerung des OctopusPro übernehmen wird, ist mittlerweile angebracht und angeschlossen. Eine abschließende Prüfung auf sicheren Sitz aller Stecker und Terminals ist unbedingt anzuraten. Speziell die Stecker für die Motoren dürfen sich im Betrieb auf gar keinen Fall lösen, denn das wäre der sichere Tot des betreffenden Treiberbausteins (TMC2209).
Wer sich an dieser Stelle wundert, wo denn der Smart-Filament-Sensor ist, dem kann ich versichern, dass ich ihn nicht vergessen habe. Aus der Erfahrung heraus, dass der Sensor auch seine Tücken in der Anfangsphase hat, wollte ich zunächst mal bei „Anfahren“ eine Störquelle ausschließen. Der Drucker lässt sich auch ohne den Sensor problemlos betreiben. Er kommt später und bedarf auch noch einer Firmwareänderung.
Einer Inbetriebnahme steht nun nichts mehr im Weg.
Sehr gute Beschreibung. Wirklich klasse.
Hättest du eventuell noch ein Foto davon, wie es in deinem Netzteil aussieht?
Hallo Nick,
danke für das Lob. Ich habe einfach das ursprüngliche Netzteil vom Drucker wieder genommen. Ein Foto habe ich jetzt nicht davon. Was speziell möchtest Du denn sehen?