Ich bin kein Freund des Bowdenextruders. Es mag schon sein, dass man sich die Bewegung der relativ hohen Massen von Steppermotor und Extruder sparen kann, aber da habe ich noch nie ein Problem gesehen. Vielleicht liegt es aber auch daran, dass ich nie versucht habe besonders hohe Geschwindigkeiten zu erreichen. Klarer Nachteil des Bowdenextruders ist aber der unpräzise Transport des Filaments. Je größer die Druckfläche wird, umso länger wird auch die Tube, durch die das Filament bewegt werden muss. Bei steifem Material wie PET-G und PLA führt das zwar nicht zu Kompression und Längung, aber in der Tube hat der Filamentdraht genug Platz ein paar Milimeter zu „verstecken“. Bei weichem Material, wie beispielsweise TPU kommt dann noch Wandreibung und Kompression dazu. In der Regel wird auch von anderen Makern vom TPU-Druck mit Bowdenextrudern abgeraten.
Deshalb werde ich auch diesen Drucker auf Direktextrusion umrüsten. Der Aufwand hält sich speziell beim X5SA-400 PRO in Grenzen.
Aufgrund seiner verbesserten Linearlager erinnert der Aufbau des Druckschlittens schon ein wenig an ein Schnellwechselsystem.
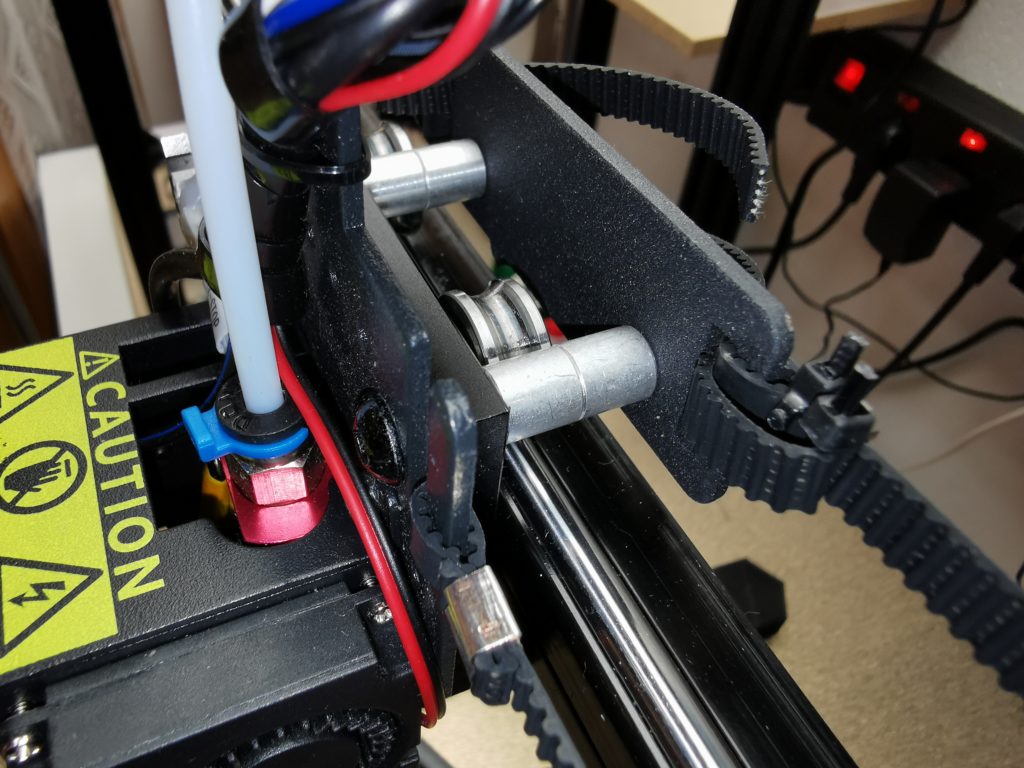
Die gesamte Drucktechnik mit Hotend, Ventilatoren und Abstandsfühler ist auf einer Metallplatte befestigt. Die Metallplatte ist mit zwei längeren M5-Schrauben an einer Kunststoffplatte fixiert. Diese Kunststoffplatte stellt den X-Schlitten dar. Auf der Hinterseite sieht man dann nochmals eine Metallplatte, die die beiden hinteren Riemen aufnimmt. Den Abstand hat man über insgesamt 4 Aluminiumhülsen realisiert.
Nimmt man jetzt die beiden selbstsichernden Muttern auf der Rückseite ab, kann man die gesamte Konstruktion zerlegen. Vorher sollte man sich natürlich um die Riemen kümmern.
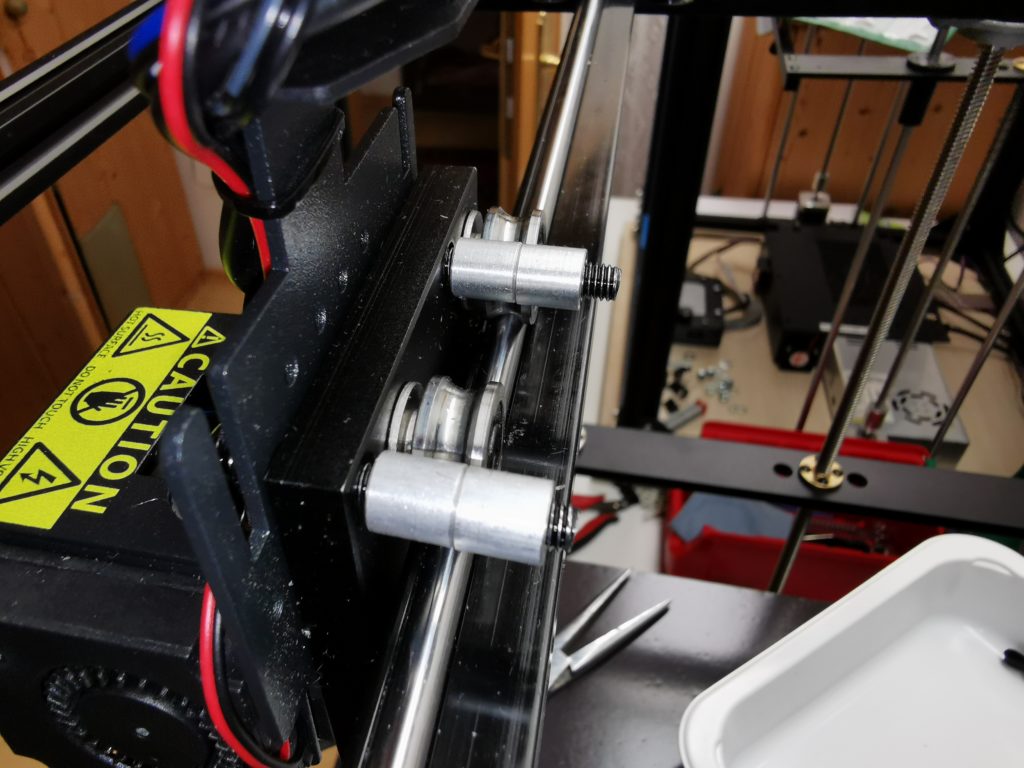
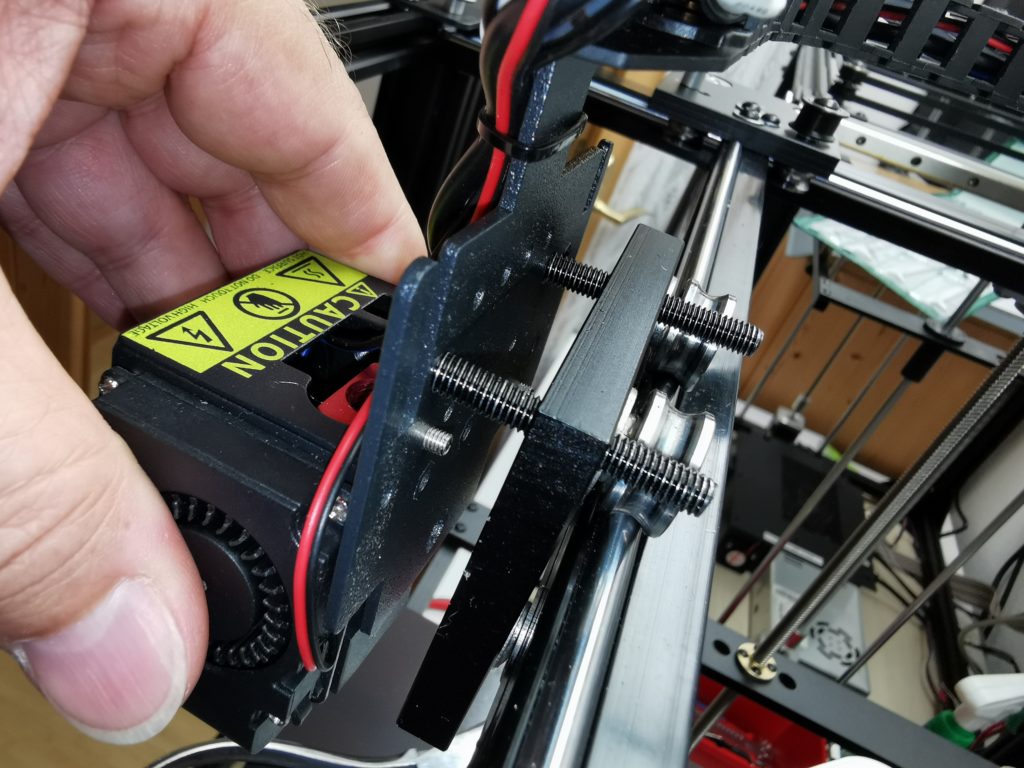
Jetzt hat man mit dem vorderen Blech die Drucktechnik komplett in der Hand. Nimmt man die aktiven Komponenten von diesem Blech ab, können die Maße für einen neuen Träger abgenommen werden, der dann auch den Stepper und den Extruder aufnimmt.
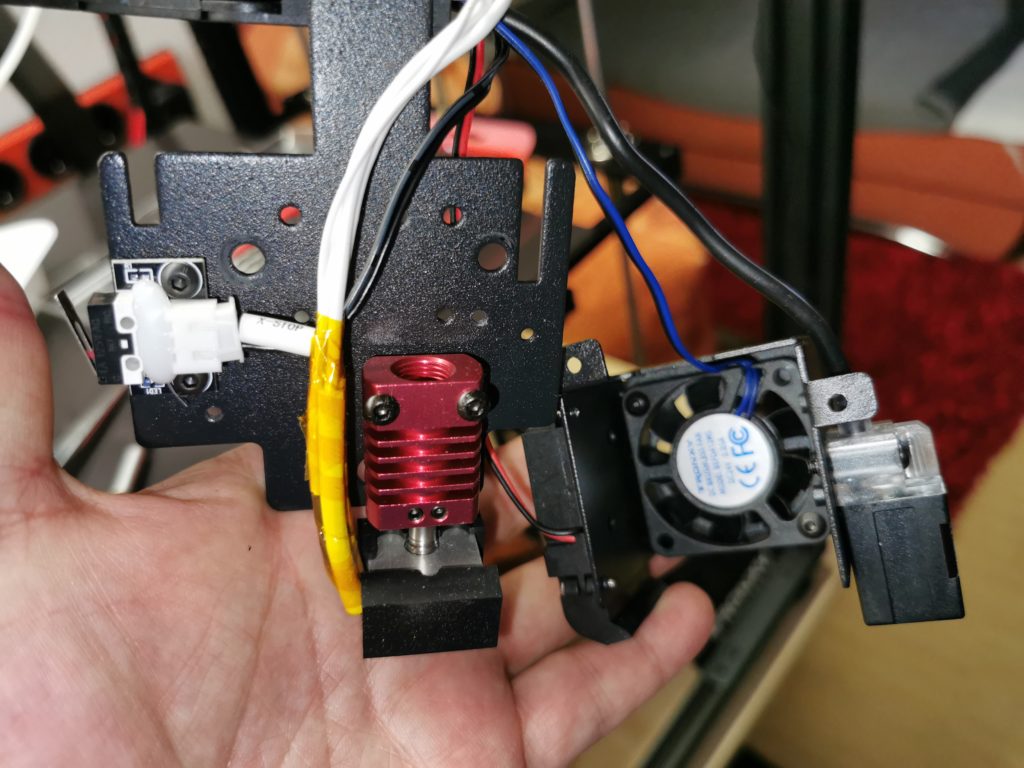
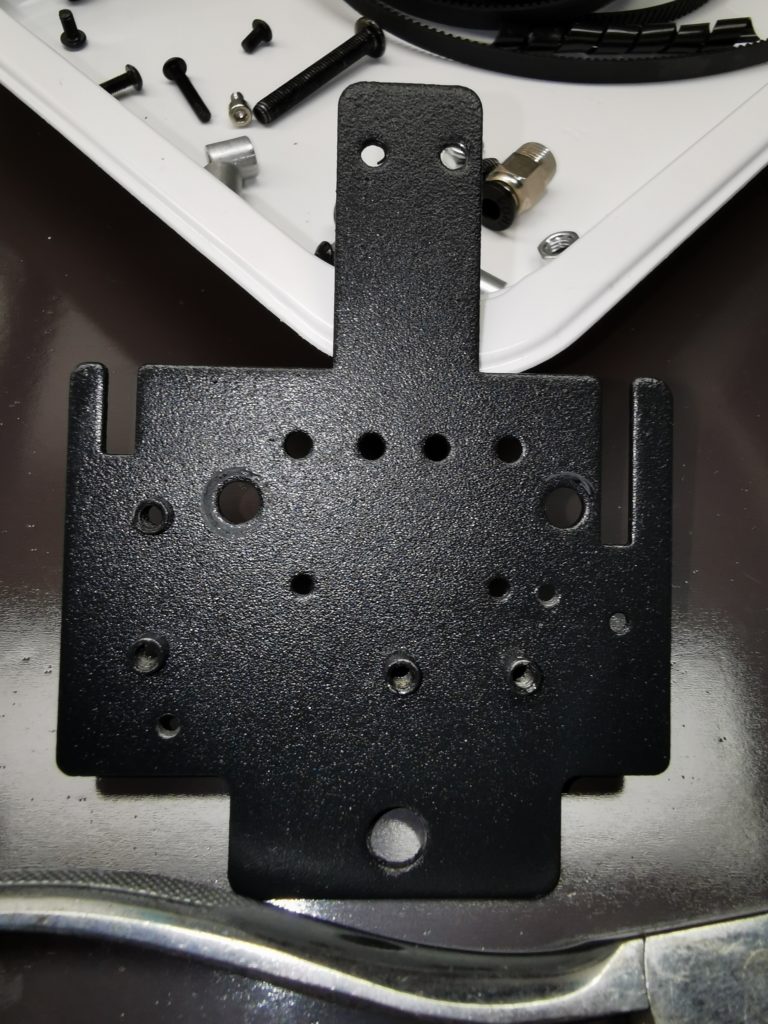
Es werden nicht alle Löcher in dem Blech benötigt. Notwendig sind die beiden Löcher, die das Hotend halten und die beiden Löcher für den Lüfterkäfig. Natürlich werden auch die beiden großen Löcher für die erneute Montage am Schlitten gebraucht. Mit Ausnahme der Letztgenannten sind alle Löcher mit M3-Gewinde ausgestattet. Andere Konstruktionen erscheinen zunächst mal schwierig, da ja die Platte direkt auf der Kunststoffplatte des Schlittens aufliegt. Dort sind aber wenigstens die Löcher für die Schrauben weitergeführt.
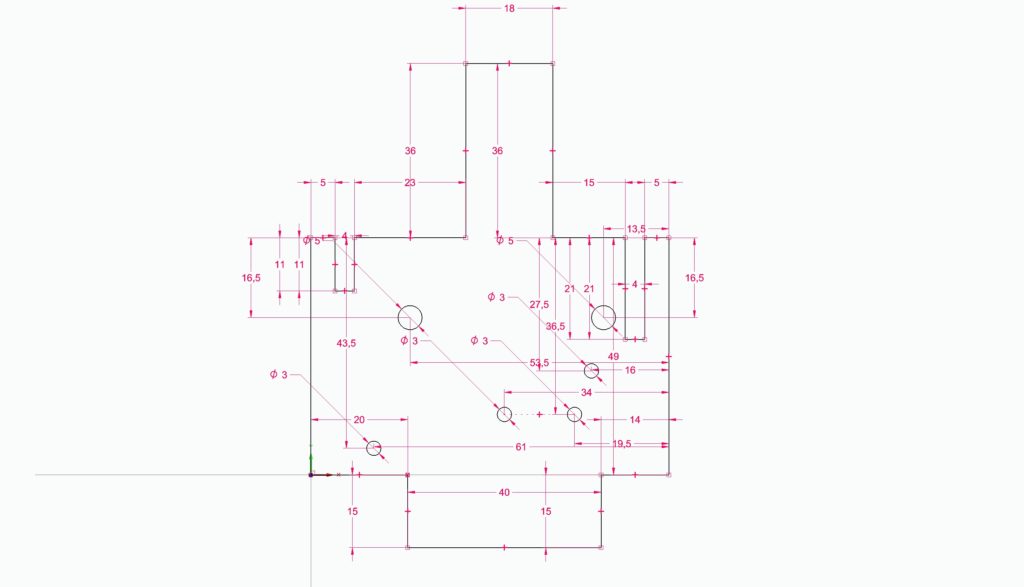
Ich habe mir die Mühe gemacht und alle Abmessungen in eine Zeichnung gebracht. Wer die Löcher mit der Bohrmaschine bohren will, kann natürlich einfach das alte Blech auf den neuen Träger auflegen und die Löcher dann übertragen. Wichtig: M3-Löcher bohrt man kleiner als 3mm. Wieviel der richtige Durchmesser beträgt, ist meist in der Dokumentation der Gewindeschneider enthalten.
Damit kommen wir dann auch schon zur Materialfrage für die neue Montageplatte. Dass es ein Winkel sein muss, dürfte klar sein, weil ja der Steppermotor befestigt werden muss. Gewisse Minimalgrößen ergeben sich auch aus der Motorhalterung und der vorhandenen Drucktechnik. Ich habe ein Aluminiumwinkelprofil aus dem Baumarkt genommen: 50mm x 50mm x 3mm. Da einerseits die Stabilität wichtig ist und andererseits Gewinde eingeschnitten werden sollen, sollte es auf keinen Fall weniger als 3mm Dicke sein.
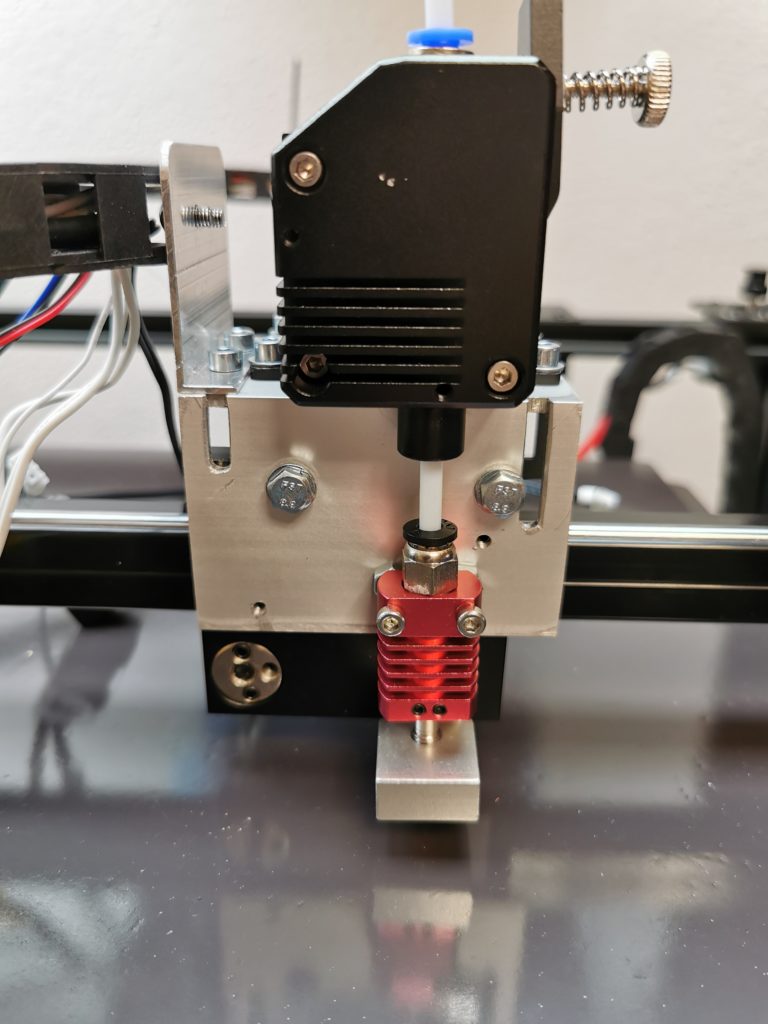
Fertig aufgebaut, – allerdings noch ohne Lüfter sieht das dann bei mir so aus. Die beiden Schlitze links und rechts oben sind für die Riemen vorgesehen. Sie sind wieder an exakt der gleichen Stelle mit der gleichen Größe wie vorher. Hier ist darauf zu achten, dass die Kanten verrundet werden, sonst werden sich die Riemen recht schnell zerlegen. Ich habe alles auf meiner Optimum BF20 Vario Fräse bearbeitet. Machbar ist das aber wahrscheinlich auch bei entsprechender Erfahrung und ordentlicher Arbeit mit einem Bohrständer. Die Schlitze lassen sich sicherlich auch mit einem Dremel oder Ähnlichem erstellen.
Sowohl für die Bohrlöcher des Motorhalters als auch für den Winkel der Energiekette habe ich keine ordentliche Zeichnung erstellt. Da reichten mir Skizzen, die ich hier gern zum Besten gebe …
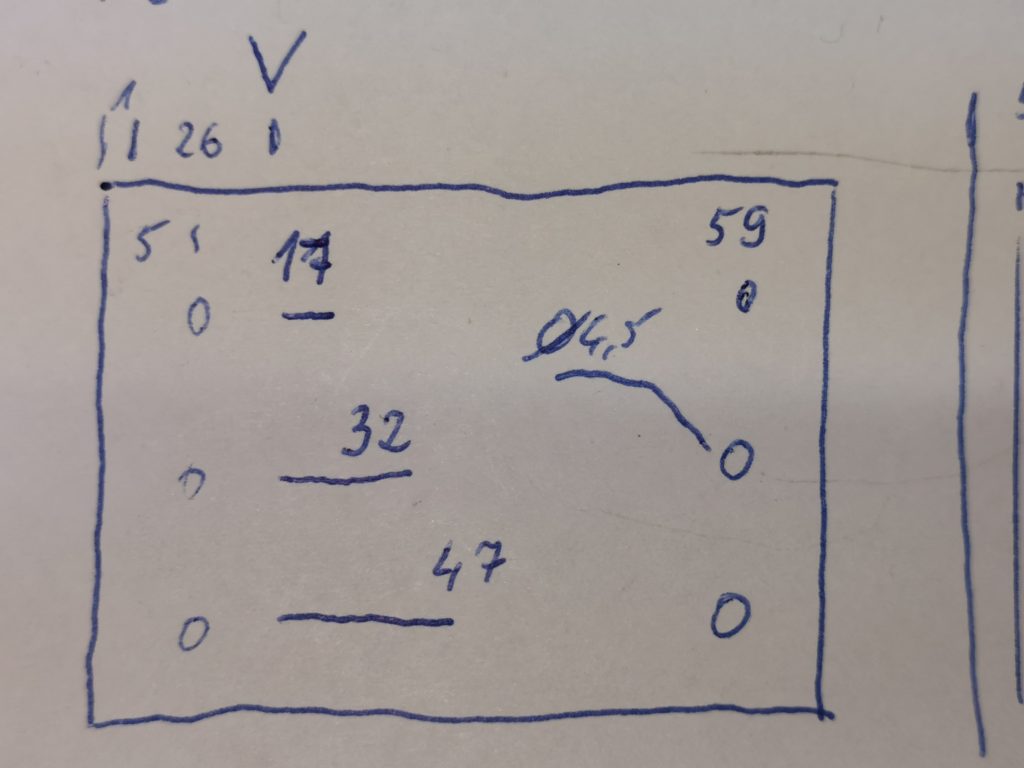
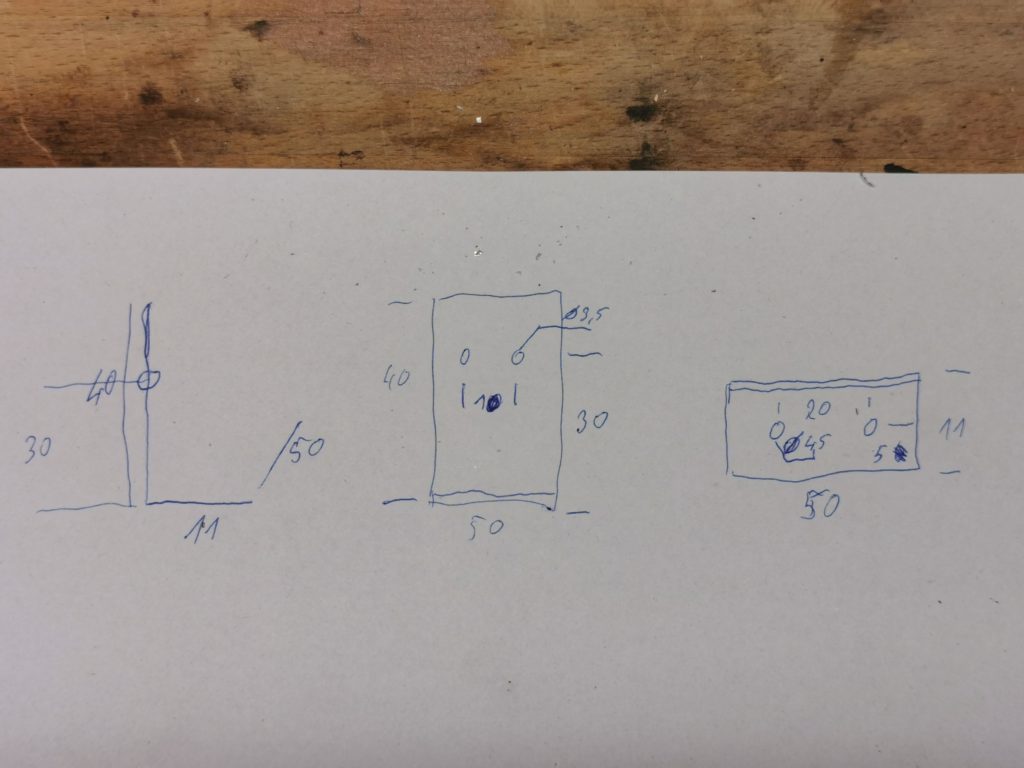
Die Oberkante des hinteren Blechs (hintere Riemenhalterung) musste ich allerdings an der Oberseite etwa 2mm kürzen, weil es sonst nicht mehr passte. Die seitlichen Schlitze für die Riemen blieben dabei aber trotzdem geschlossen. Die mittleren Schrauben der Motorhalterung können aus dem gleichen Grund nicht gesetzt werden. Es käme sonst zu Kollisionen. 4 Schrauben reichen aber locker aus.
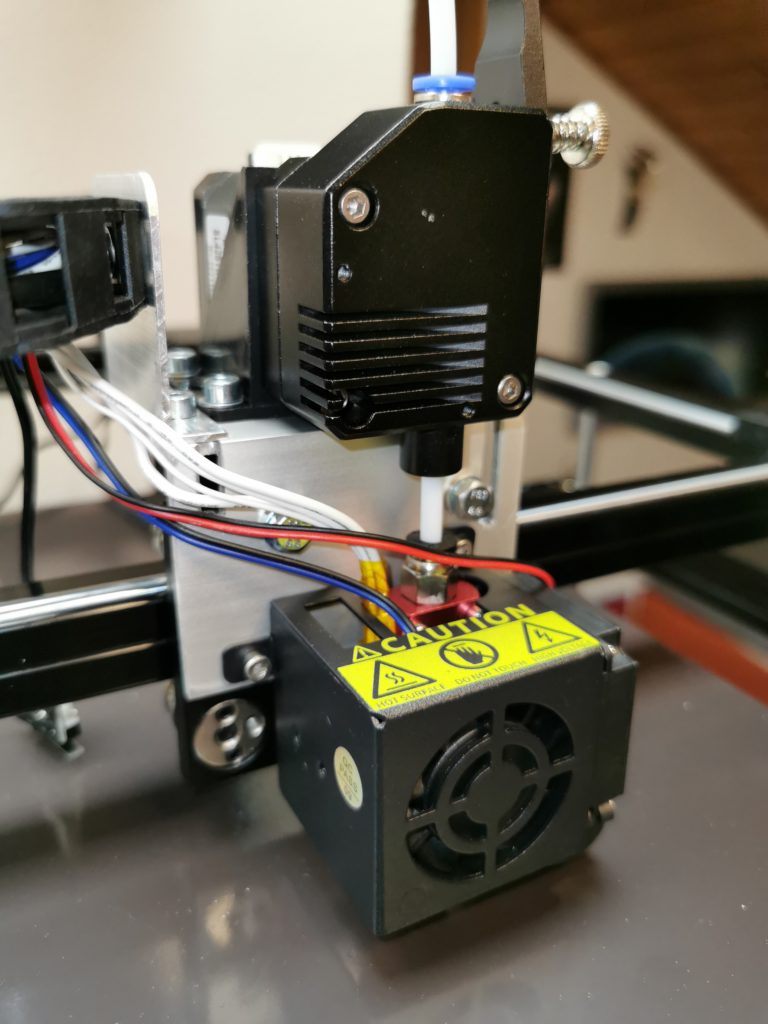
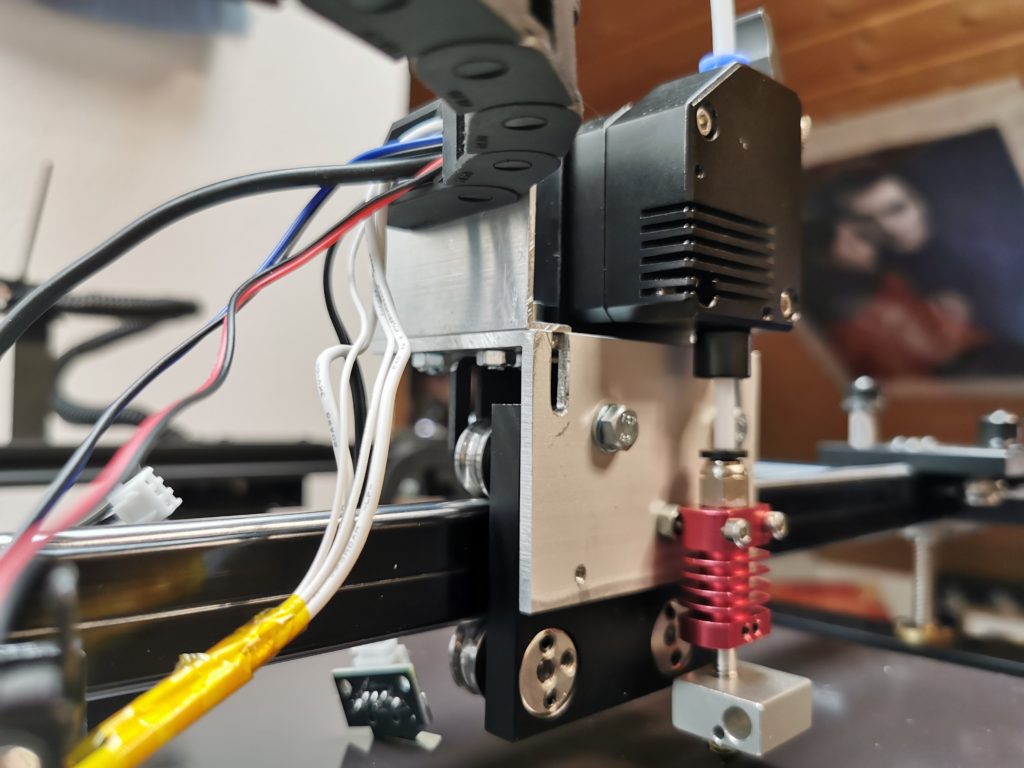
Man darf hier aber nicht vergessen, dass das gerade mal die Hardwarearbeit war. Der Motor ist jetzt natürlich nicht mehr verdrahtet. Dafür muss man entweder ein entsprechendes Kabel selber bauen oder aber lange etwas Passendes suchen.
Im nächsten Beitrag geht es um den Tausch des TRONXY Näherungssensors gegen ein 3D Touch (oder auch BL Touch).
Mittlerweile gehe ich stark davon aus, dass ich auf dem OctopusPro-Board Klipper fahren werde. Damit entspräche ich dann auch dem Wunsch vieler Leser dieses Blog, die mich speziell dazu angeschrieben hatten.
Stay tuned …
Es bleibt spannend !